Horn mesh etching plays a vital role in various industries, particularly in manufacturing stainless steel components like speaker grilles, automotive air filters, and architectural panels. For process engineers and technical experts, optimizing parameters in high-volume manufacturing is essential to enhance etching efficiency and quality while minimizing scrap rates. This article explores key aspects of horn mesh etching, including etchant chemistry, masking materials, critical process parameters, and a real-world case study demonstrating how optimization can reduce waste.
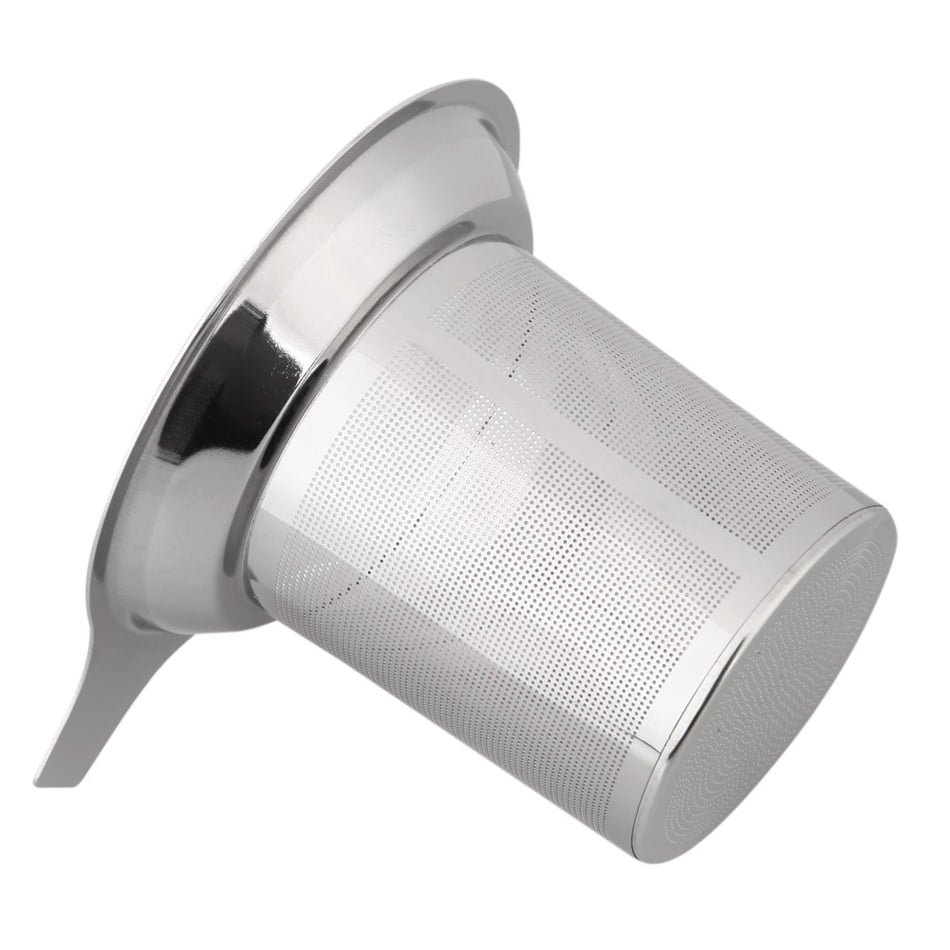
Etchant Chemistry: Nitric Acid vs. Ferric Chloride for Stainless Steel Horn Mesh
Nitric Acid (HNO₃)
Nitric acid is a commonly used etchant in horn mesh etching, especially for stainless steel. It offers several advantages, particularly in terms of speed:
- Faster Etching: Nitric acid tends to work quickly, especially at higher concentrations, making it suitable for high-volume production where time is a critical factor.
- Fine Detail Reproduction: It produces clean edges, which is essential for intricate mesh patterns in applications like speaker grilles.
However, there are some risks associated with nitric acid:
- Overcorrosion: If left for too long or at too high a concentration, nitric acid can cause overcorrosion, which degrades the quality of the mesh and leads to dimensional inaccuracies.
- Health and Safety Concerns: Nitric acid is highly corrosive and requires careful handling, including appropriate personal protective equipment (PPE) and ventilation.
Ferric Chloride (FeCl₃)
Ferric chloride is another widely used etchant, known for its more controlled etching compared to nitric acid:
- Slower, More Controlled Process: Ferric chloride etches more slowly, which can result in more precise control over the depth of the etching, reducing the risk of overcorrosion.
- Lower Etch Rate: The slower etching speed may not be ideal for high-volume manufacturing that demands faster processing times.
- Less Aggressive: It’s less aggressive on stainless steel compared to nitric acid, making it a safer choice for prolonged etching processes.
However, ferric chloride also has some downsides:
- Extended Processing Time: The slower etch rate can increase production times, making it less ideal for high-volume manufacturing without optimization.
- Handling and Disposal: Ferric chloride can be challenging to handle and dispose of, especially in large volumes.
Conclusion: Which Etchant is Better?
For high-volume manufacturing, the choice between nitric acid and ferric chloride comes down to the balance between speed and control. Nitric acid offers speed but comes with the risk of overcorrosion, while ferric chloride provides greater control but at the cost of a slower process. Depending on the specific application and production needs, manufacturers may opt for a combination of both, adjusting parameters to optimize the etching process.
Masking Materials: Laser-Cut Polymer Films vs. Screen-Printed Photoresist
When it comes to masking for micron-level precision in horn mesh etching, selecting the right masking material is critical.
Laser-Cut Polymer Films
Laser-cut polymer films are an excellent choice for high-precision etching. These films are typically polyimide or PET (polyethylene terephthalate), and they offer the following advantages:
- Micron-Level Accuracy: Laser cutting provides extremely high precision, allowing for intricate designs such as hexagonal mesh patterns to be etched with very fine details.
- Clean Edges: The laser cutting process produces clean, sharp edges without smudging, reducing the need for post-etching cleanup.
- Consistency: Laser-cut films ensure consistent results across multiple batches, which is essential for high-volume production.
Screen-Printed Photoresist
Screen-printed photoresist is another common method for masking, especially in industries where high-volume and continuous production are required.
- Ease of Application: Photoresist is typically applied using a screen printing process, which allows for quick and consistent coverage across large surfaces.
- Cost-Effective for Large Runs: While photoresist may not offer the micron-level precision of laser-cut films, it is highly effective for applications where very fine detail is not required.
Conclusion: Choosing the Right Masking Material
For high-precision etching (e.g., creating intricate patterns for speaker grilles or automotive air filters), laser-cut polymer films are generally the better choice. For more cost-effective, high-volume production where the level of detail is less critical, screen-printed photoresist can be a suitable alternative.
Critical Data: Etch Rates (µm/min) vs. Temperature (20°C–60°C) for 316L Stainless Steel
The etching rate is heavily influenced by both the etchant chemistry and temperature. Understanding the relationship between etch rate and temperature is crucial for optimizing the etching process. Below is a table showing typical etch rates (µm/min) at varying temperatures for 316L stainless steel using ferric chloride as the etchant:
Temperature (°C) | Etch Rate (µm/min) |
---|---|
20°C | 1.5 |
30°C | 2.0 |
40°C | 3.5 |
50°C | 5.0 |
60°C | 7.5 |
Key Insights:
- Temperature directly impacts the etch rate: As the temperature increases, the etch rate accelerates. However, pushing the temperature too high can lead to overcorrosion or uneven etching.
- Optimal Temperature Range: To balance speed and precision, manufacturers typically operate in the 40°C–50°C range for ferric chloride-based etching processes.
Case Study: Reducing Scrap Rates by 25% in Automotive Filter Production Using Real-Time pH Monitoring
In a recent case study from the automotive industry, a company producing air filters using horn mesh etching reduced scrap rates by 25% by implementing real-time pH monitoring during the etching process. Here’s how:
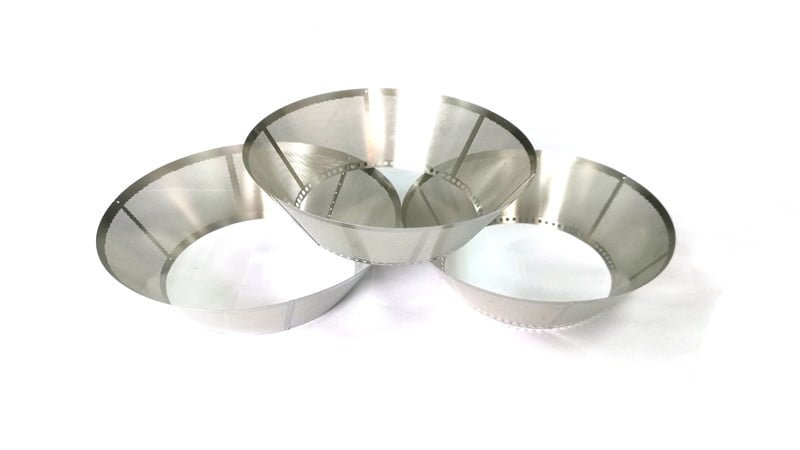
Problem:
- High scrap rates due to inconsistent etching results caused by fluctuations in the pH level of the etching solution.
Solution:
- The company integrated a real-time pH monitoring system to continuously track and adjust the pH of the etching solution during production. By maintaining the optimal pH range for the ferric chloride etchant, they achieved consistent etch rates, minimizing scrap and improving the overall quality of the etched mesh.
Results:
- 25% reduction in scrap: More consistent etching, fewer rejected parts.
- Improved Efficiency: Real-time monitoring reduced the need for manual adjustments and minimized downtime.
Pro Tip: “Maintain a 15° Spray Angle During Etching to Minimize Undercutting in Hexagonal Mesh Patterns”
When etching hexagonal mesh patterns, undercutting can occur if the etching solution is sprayed at too steep an angle. To minimize this effect and ensure clean, well-defined edges, maintain a 15° spray angle during the etching process. This angle helps control the direction of the etching solution and ensures uniform etching without excessive undercutting, especially in fine patterns.
In high-volume horn mesh etching, parameter optimization is key to improving efficiency, quality, and reducing waste. By selecting the right etchant chemistry, optimizing masking materials, and carefully controlling process parameters like temperature and pH levels, manufacturers can achieve consistent, high-quality results. Additionally, incorporating pro tips such as spray angle management and using real-time monitoring can significantly enhance the manufacturing process. These strategies lead to lower scrap rates and improved profitability in industries like automotive, electronics, and aerospace.