Tantalum, a rare and exceptional metal, possesses unique properties that make it highly sought-after in various industries, including aerospace, electronics, and medical devices.
[custom_pricing]
View our Tantalumetching production facility
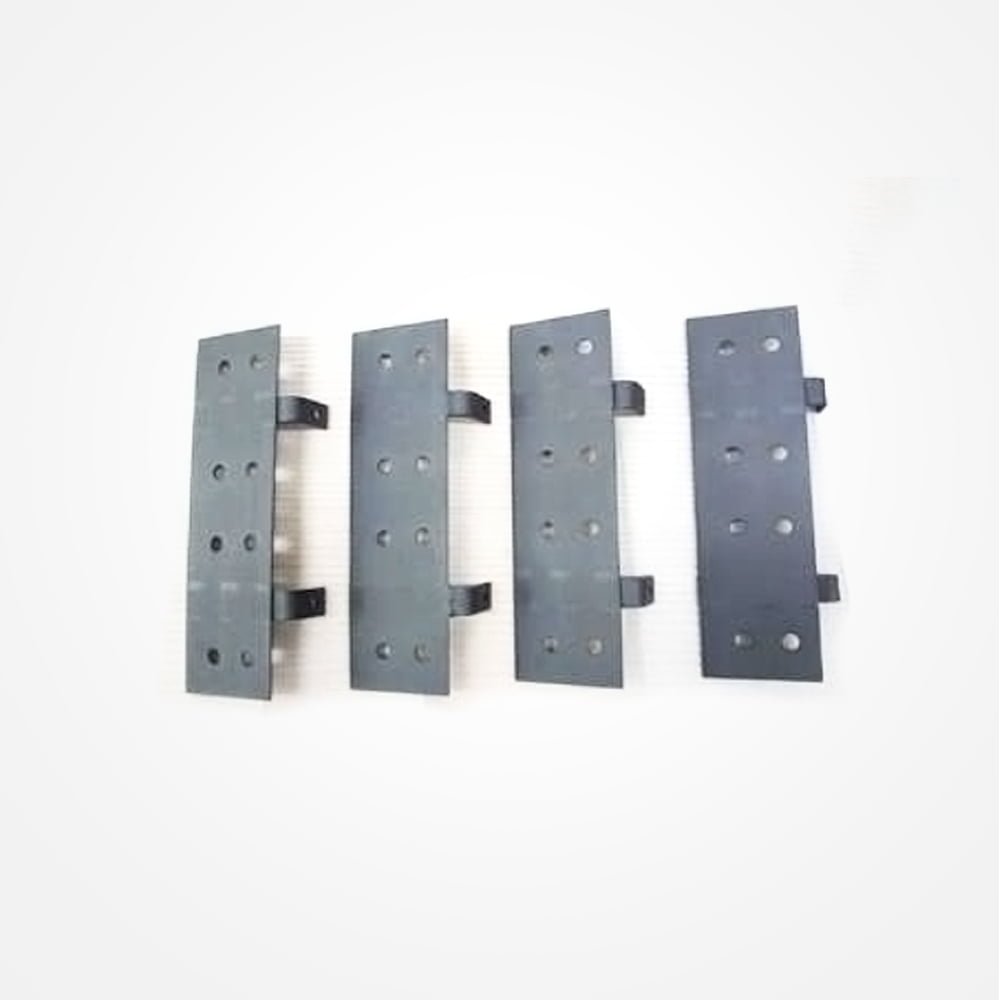
Types of Tantalum and Alloys: Advantages and Disadvantages for Wet Processing
Tantalum comes in various forms, and alloying it with other elements can enhance specific attributes. Let’s explore the advantages and disadvantages of each alloy for wet processing:
- Pure Tantalum: Advantages include excellent corrosion resistance, making it ideal for chemical processing equipment and medical implants. However, its high ductility can lead to deformation during certain etching processes.
- Tantalum-Tungsten (Ta-W): This alloy offers increased strength and hardness, making it suitable for high-stress applications such as jet engine components. However, its hardness may require careful consideration during etching to avoid cracking.
- Tantalum-Niobium (Ta-Nb): The addition of Niobium improves Tantalum’s formability and helps reduce the risk of embrittlement during the etching process. This alloy is commonly used in the production of superalloys and electronics.
Metal Etching Tantalum
Metal etching is a fundamental process used to shape, pattern, or remove material from Tantalum surfaces. In the wet processing process, metal etching machines are commonly employed. Let’s explore the key aspects of metal etching for Tantalum:
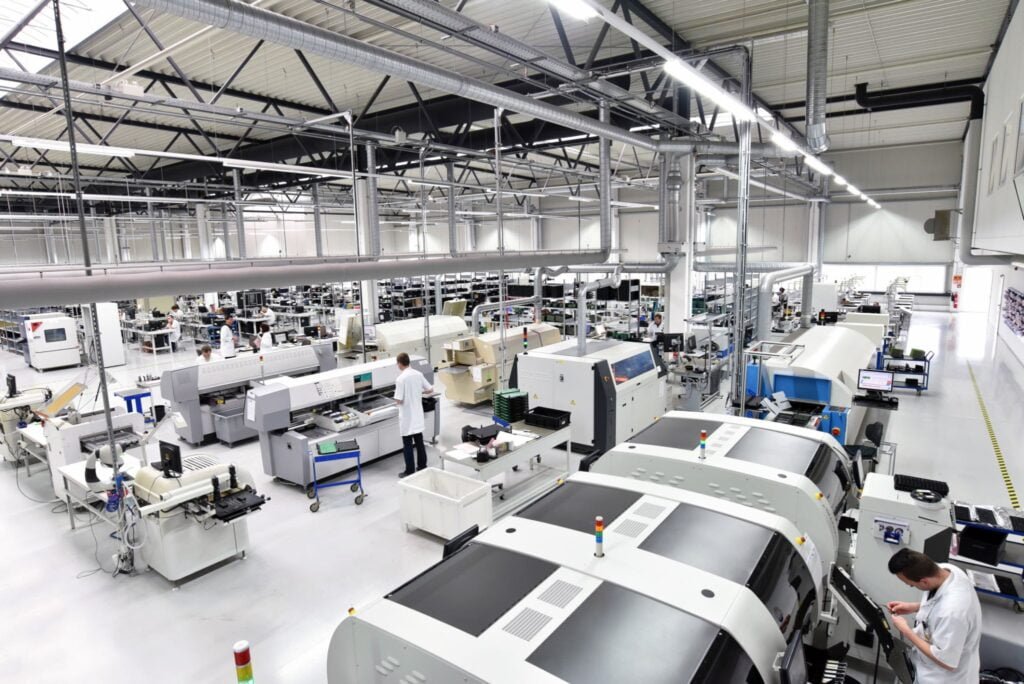
- Etching Difficulty: Tantalum’s resistance to corrosion poses challenges during etching. Hydrofluoric Acid (HF), Ferric Chloride Etchant, and Cupric Chloride Etchant are common etchants used for Tantalum. HF is highly corrosive and requires careful handling to achieve precise etching, while Ferric Chloride Etchant offers deep and well-defined patterns. Cupric Chloride Etchant provides controlled etching and is commonly used in electronic applications.
- Precautions: Due to the corrosive nature of etchants, strict safety precautions are essential. Proper ventilation, personal protective equipment, and adherence to handling protocols are necessary to prevent exposure to hazardous fumes and chemical burns.
One of the recommended alkaline etchants for etching Tantalum is a solution of Potassium Hydroxide (KOH). Potassium Hydroxide is a strong base and can effectively etch Tantalum by removing thin layers of the material.
The etching process with Potassium Hydroxide is typically performed at elevated temperatures to enhance its etching capabilities. The etching rate and selectivity can be controlled by adjusting the concentration of the Potassium Hydroxide solution and the temperature.
It’s important to handle Potassium Hydroxide with care as it is caustic and can cause skin and eye irritation. Proper safety measures, including the use of protective equipment and good ventilation, should be observed when working with Potassium Hydroxide for Tantalum etching.
Tantalum etching equipment
Photo Etching Tantalum
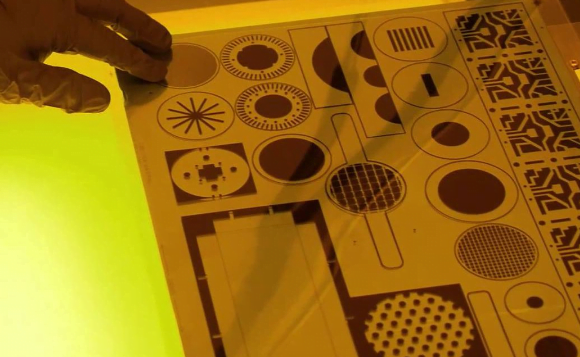
Photo etching, also known as chemical milling, offers precise and intricate patterns on Tantalum surfaces. The process involves using light-sensitive masks to protect specific areas while etching the exposed regions. Let’s explore the key aspects of photo-etching for Tantalum:
- Processing Difficulty: Photo-etching demands exceptional accuracy and control. The photoresist must be carefully applied and developed to ensure accurate pattern transfer onto the Tantalum surface. The use of advanced photolithography techniques and skilled expertise is crucial to achieving the desired precision.
- Precautions: Handling of the photoresist requires a clean and controlled environment to prevent contamination. Careful adherence to processing times and temperatures during development ensures precise pattern transfer without overreaching or under etching.
Etching precision-machined Tantalum materials is a highly specialized process that requires a thorough understanding of the different types and alloys of Tantalum, as well as the intricacies of electroforming, surface treatment, metal cleansing, and etching techniques. By selecting the most suitable processes and adhering to necessary precautions, Tantalum materials can continue to revolutionize industries and offer innovative solutions to complex engineering challenges.
View our metal etching products
how to etch Tantalum?
Etching Tantalum Process Guidelines
Metal Alloy | Etchant | Etching Temperature (°C) | Etching Concentration (%) | Estimated Etching Depth (microns) | Etching Quality |
---|---|---|---|---|---|
Etching Pure Tantalum | Hydrofluoric Acid (HF) | Room temperature | 5% HF | 10-40 | High-quality (smooth) |
Etching Tantalum-Tungsten (Ta-W) | Ferric Chloride Etchant | Room temperature | 10% FeCl3 | 10-50 | High-quality (smooth) |
Etching Tantalum-Niobium (Ta-Nb) | Cupric Chloride Etchant | Room temperature | 10% CuCl2 | 10-50 | High-quality (smooth) |
Etching Tantalum-Niobium (Ta-Nb) | Potassium Hydroxide (KOH) | Room temperature | 10-20% KOH | 10-50 | High-quality (smooth) |
The values provided are approximate and can vary depending on specific etching conditions, including exposure time and the condition of the tantalum or tantalum alloy surface. Always conduct test etches and adjust parameters as needed to achieve your desired results. Additionally, safety precautions should be followed when handling these chemicals, especially in the case of Hydrofluoric Acid.
If you have metal wet etching Tantalum needs, please feel free to contact us.
FAQs
[FAQS]
Etching Tantalum Samples
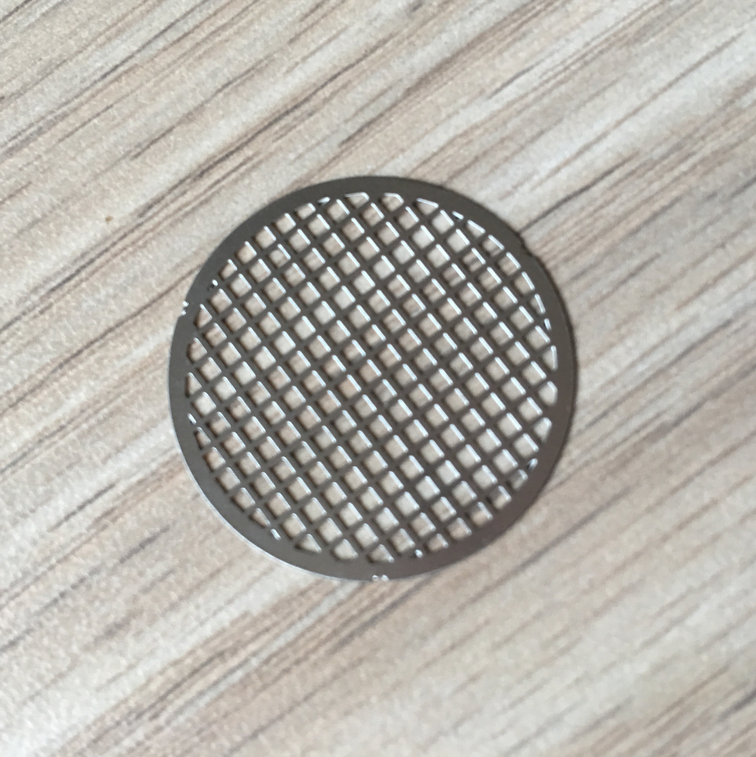
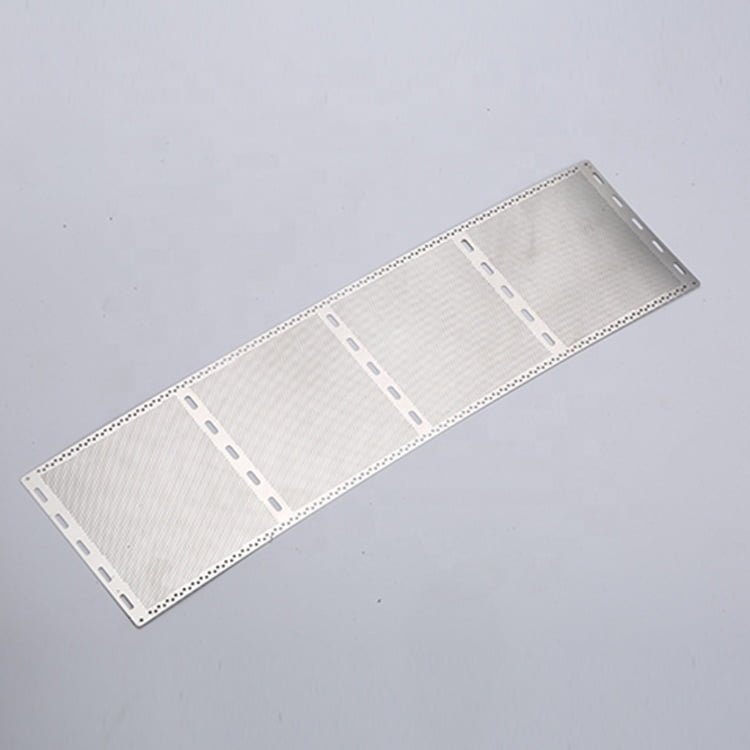
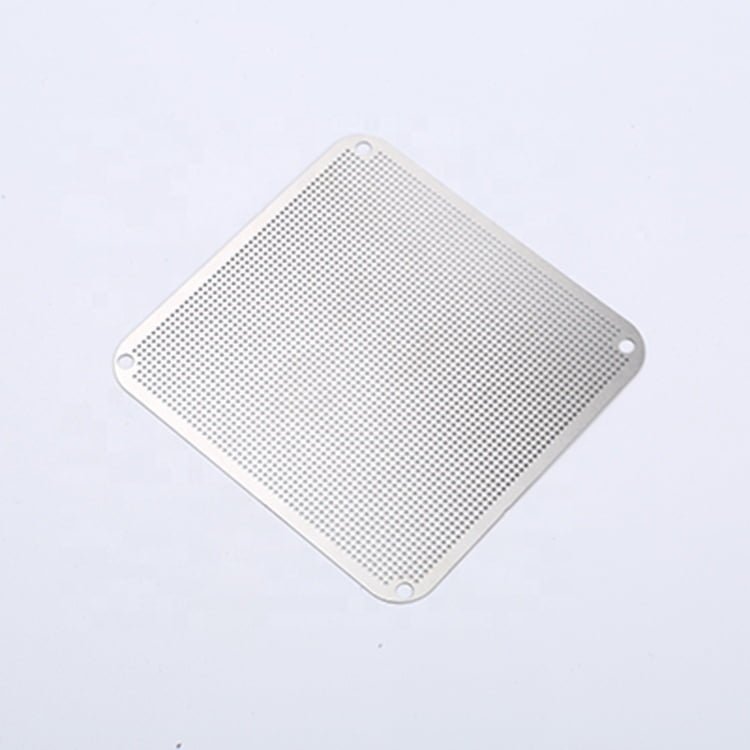
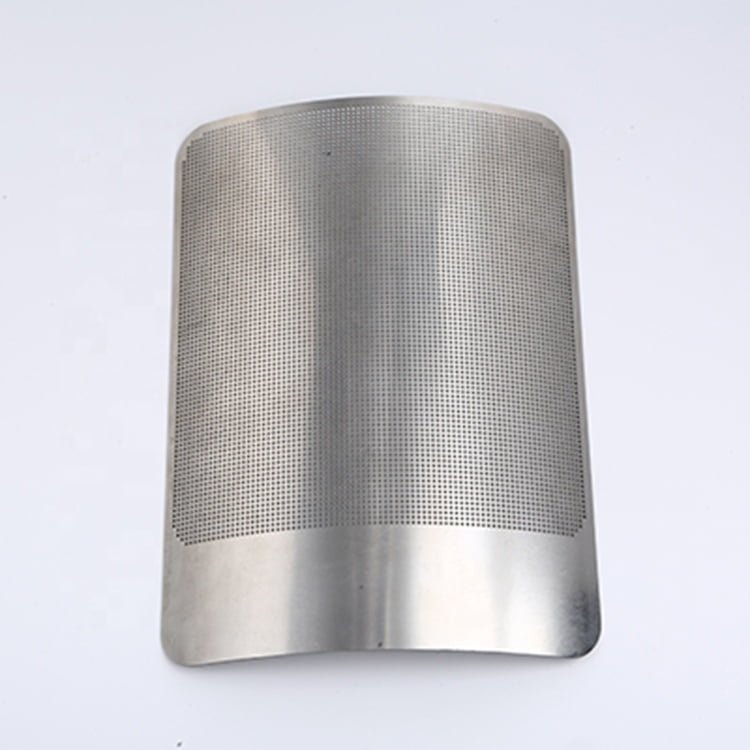
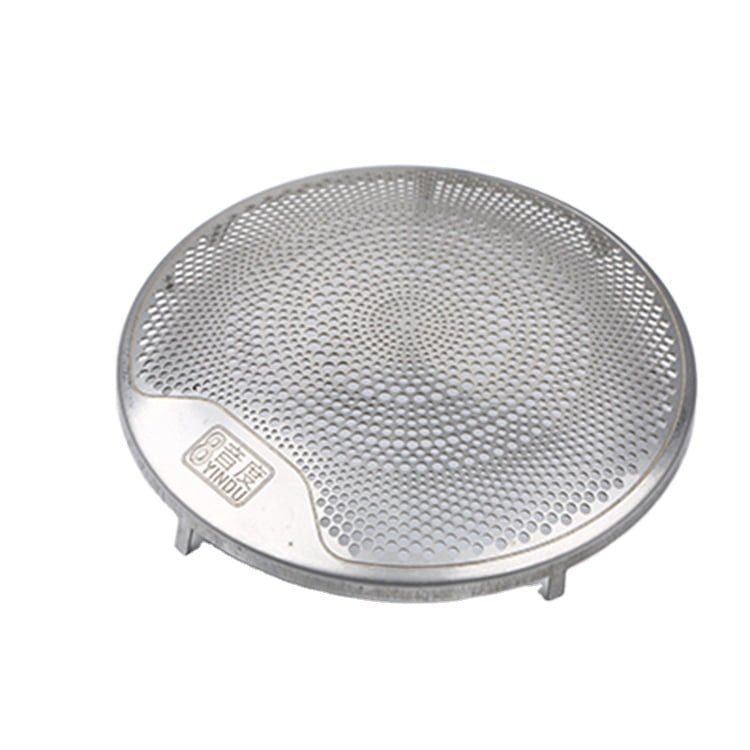
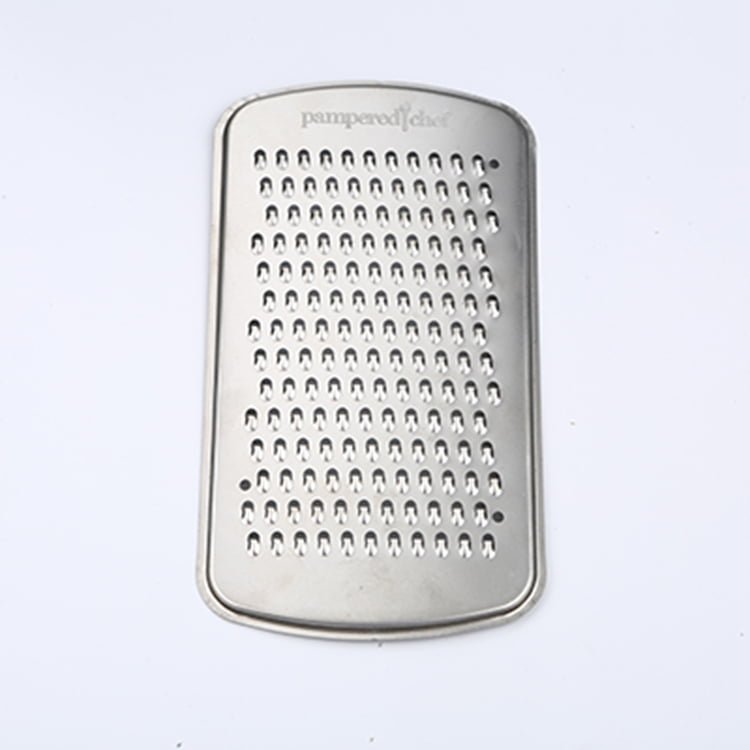
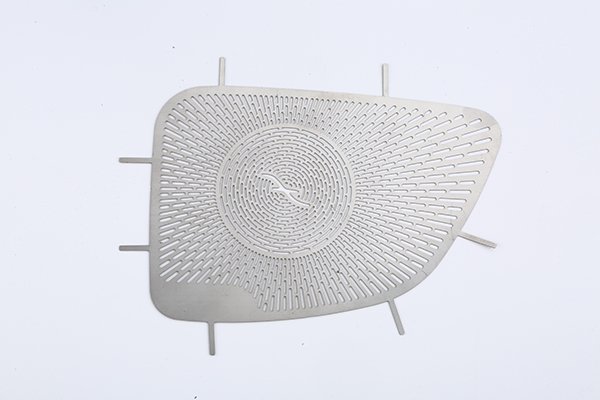
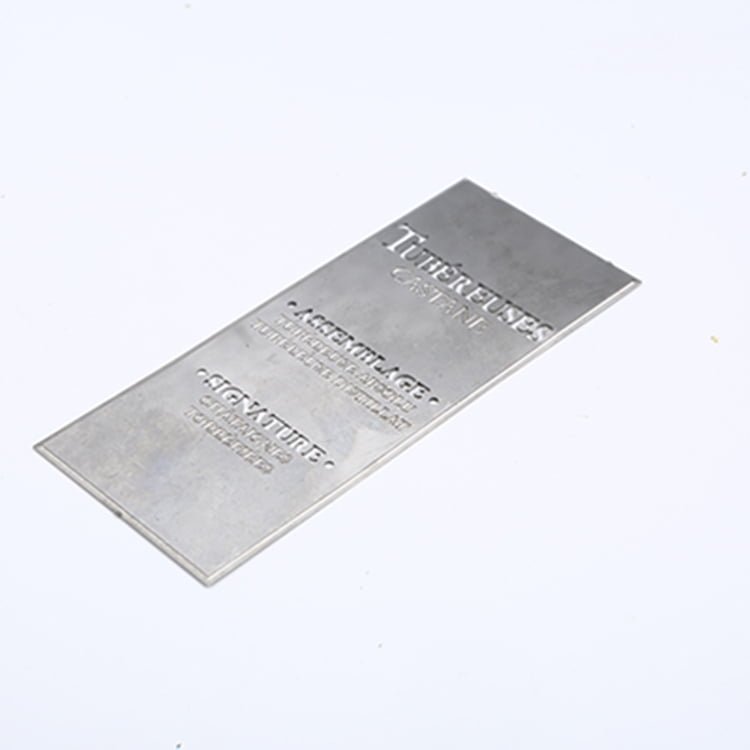
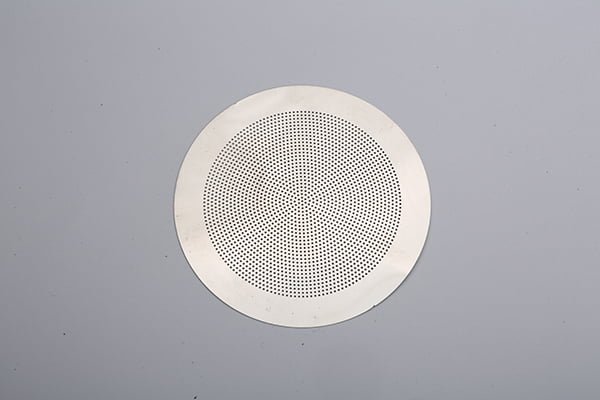
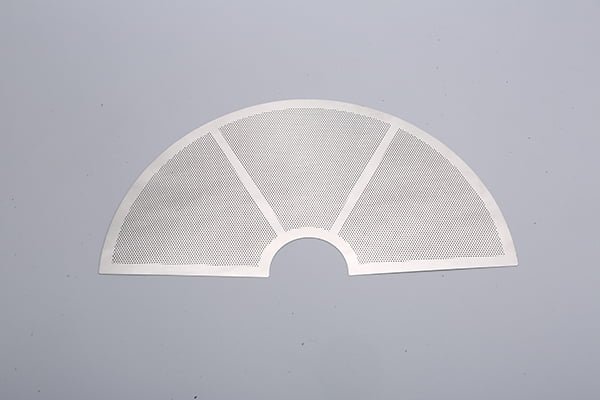
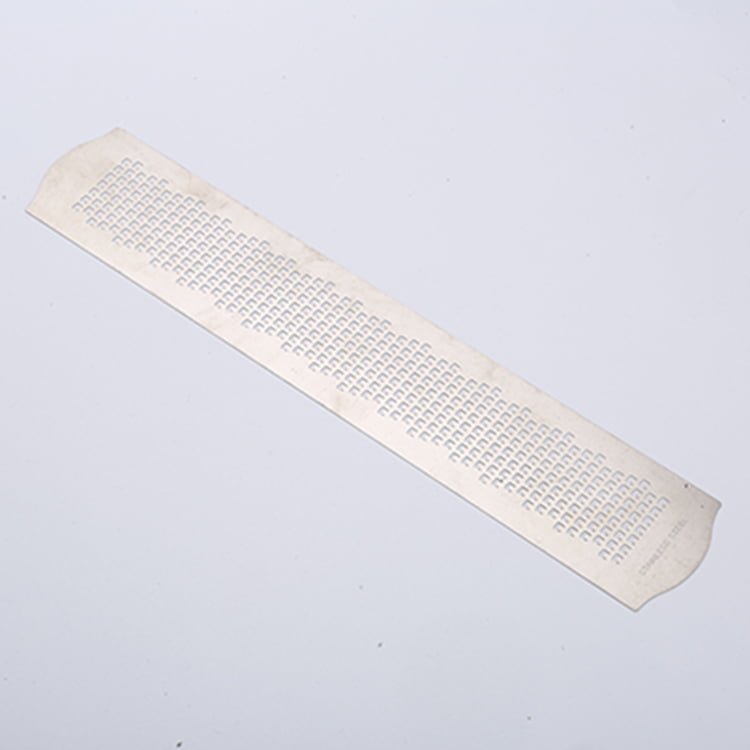
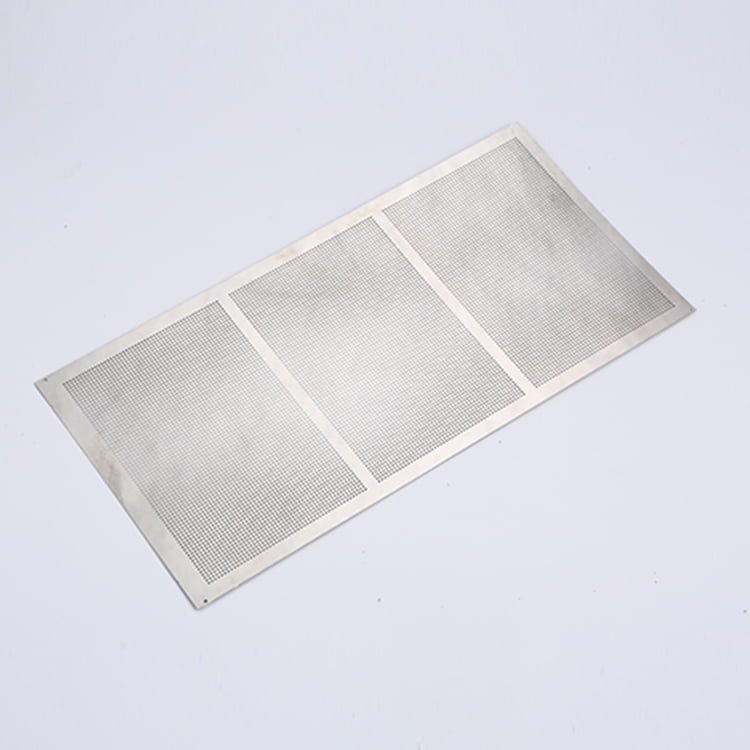
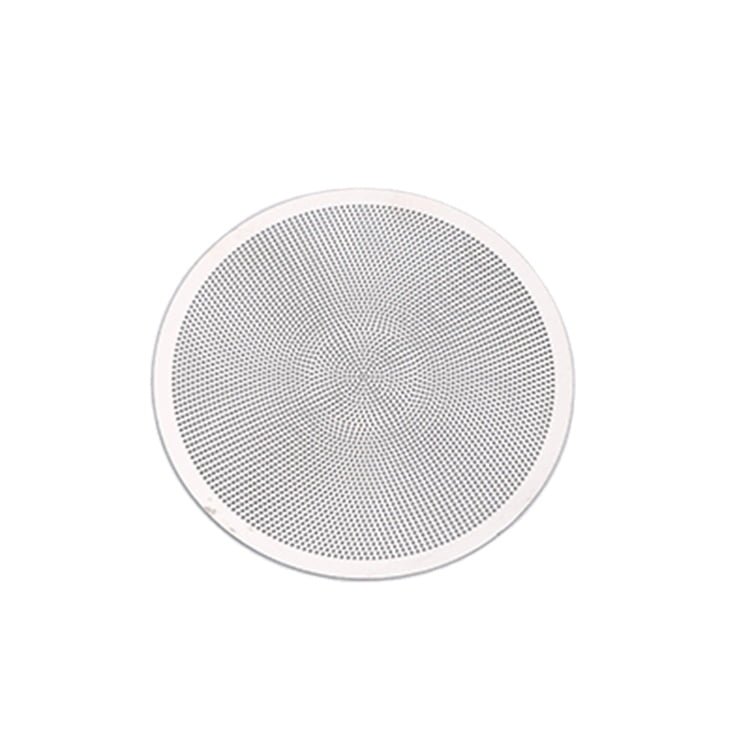
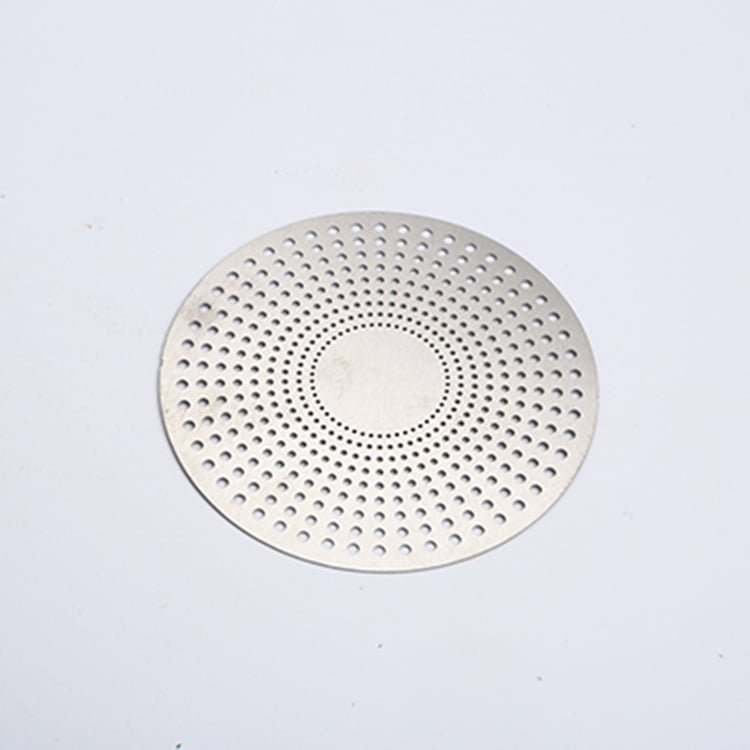
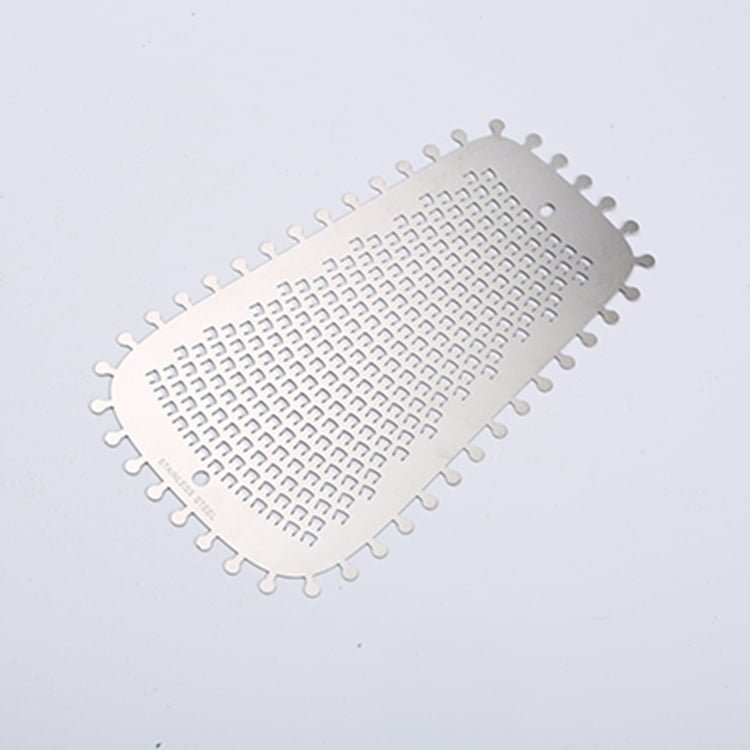
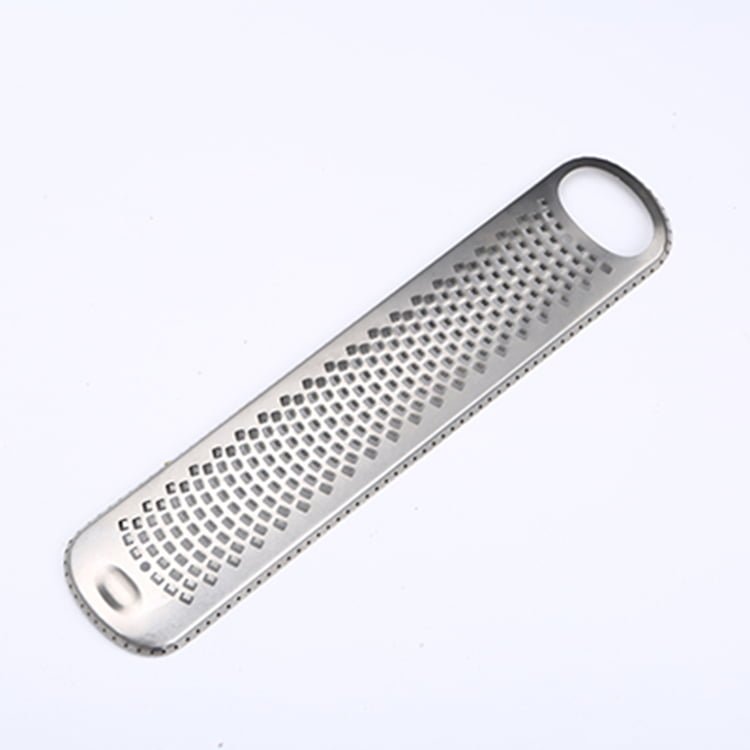
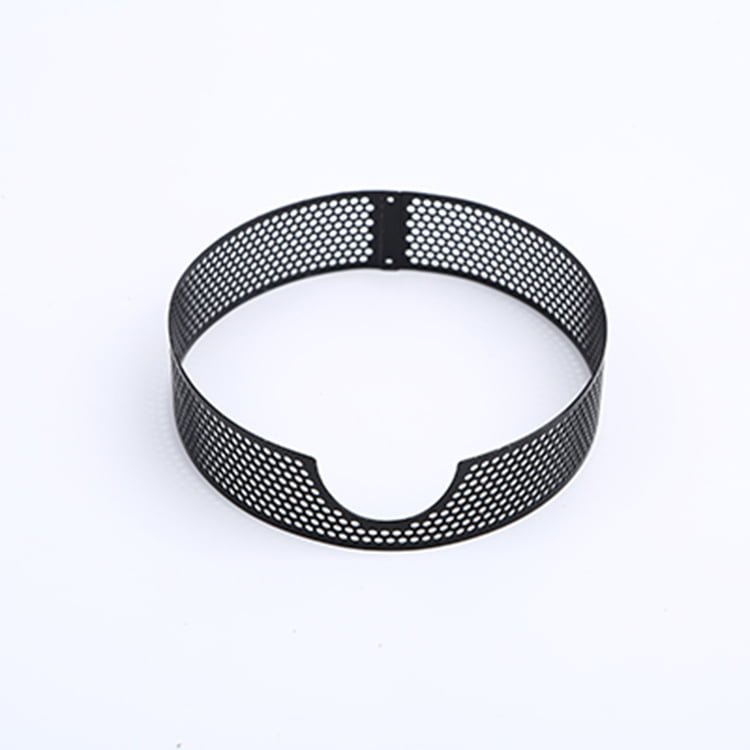

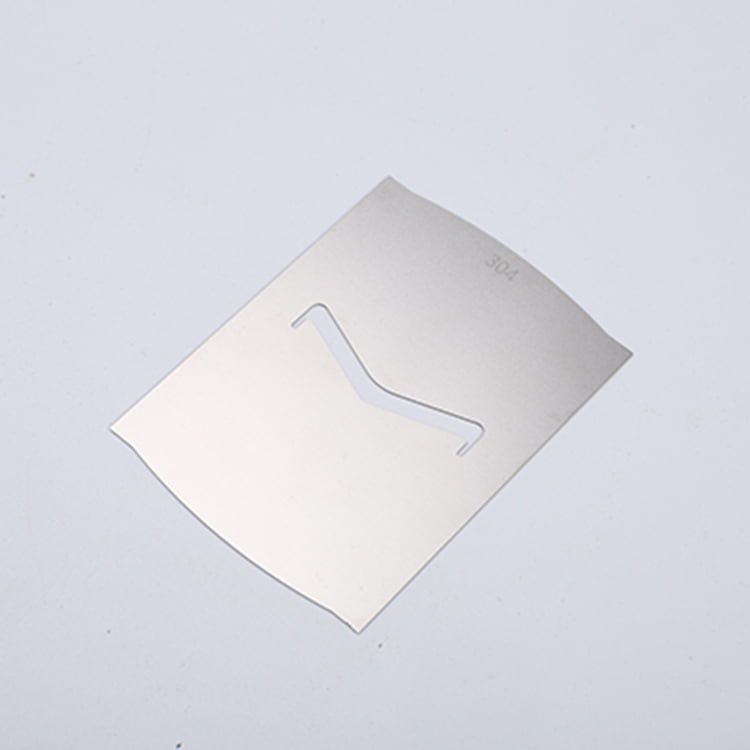

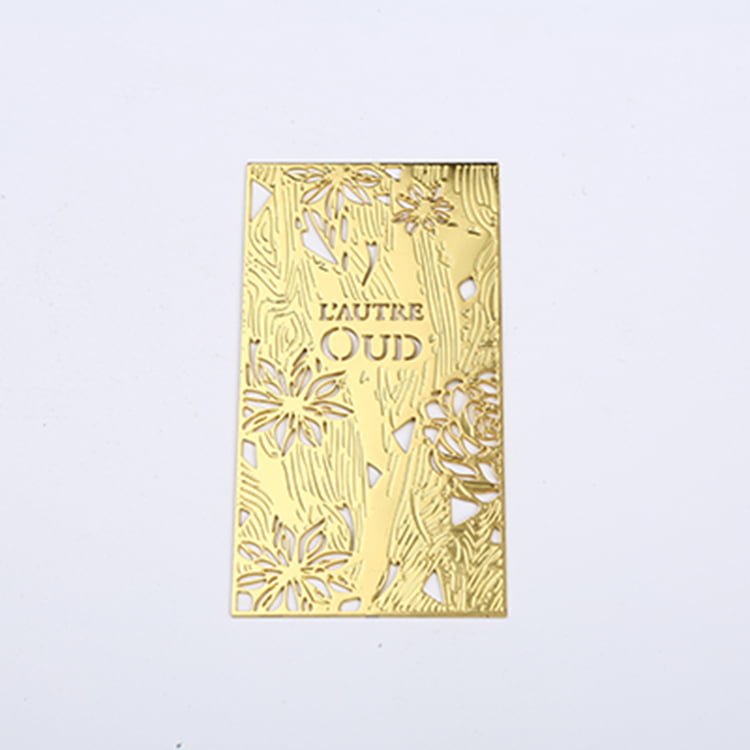

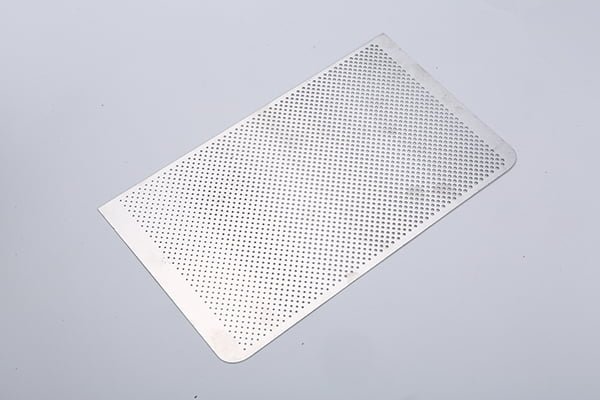