Customizing wet chemical etching machines offers significant advantages for industries that require precision, flexibility, and efficiency. By tailoring machines to meet specific production needs, manufacturers can improve throughput, achieve higher precision, and reduce operational costs. Whether it’s incorporating automated material handling systems, temperature controls, or multi-stage etching processes, the ability to customize etching equipment has made it an invaluable tool for manufacturers across industries like electronics, semiconductors, and aerospace.
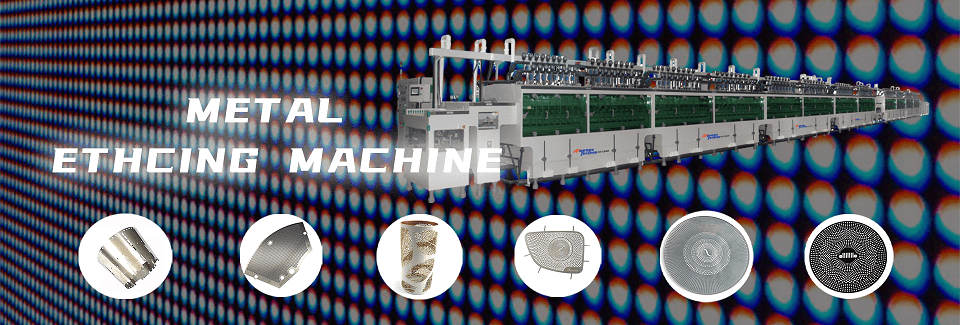
The Importance of Customization in Etching Machines
In industries where precision and quality are paramount, having a one-size-fits-all approach to etching machines simply isn’t enough. Customizing wet chemical etching machines to meet specific production requirements can drastically improve efficiency, precision, and flexibility. Customization can range from simple modifications, such as adjusting the size of the etching bath or adding temperature controls, to more complex modifications like integrating automated loading systems or multi-stage etching processes.
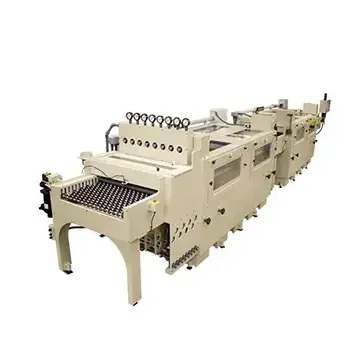
Available Conveyor Widths 20″ 30″ 40″ 50″ 60″ | Common Processes Custom Size (1 to as many chambers as you want) DES (Develop – Etch – Strip) Etcher (Stand Alone) SES (Strip – Etch – Strip) | Common Materials Etched Aluminum Copper Glass Steel Titanium And more | Common Chemicals Alkaline Etchant Cupric Chloride Etchant Ferric chloride Etchant Hydrofluoric Acid (HF) Micro etch |
For instance, Chemcut, a leading manufacturer of etching systems, has developed a range of customizable solutions designed for industries such as semiconductor manufacturing and precision PCB fabrication. Their systems allow for unique configurations, including different etching chamber sizes, multi-process capabilities (e.g., strip-etch-strip,SES Etching Machine), and temperature management options. According to Chemcut’s blog, their custom machines have significantly improved operational efficiency and precision for customers, particularly in the aerospace and defense sectors, where small tolerances and exacting specifications are crucial.
The need for customization arises in response to the diverse requirements of different industries. For example, manufacturers involved in high-precision applications, such as medical device production or fine metalworking, may require etching machines with ultra-high resolution, automated cleaning stations, and special etching baths to process exotic materials. Customization allows manufacturers to integrate features such as inline filtration systems, pH controllers, or recipe-driven operation to enhance consistency across varied production batches.
Common Customizations and Add-ons for Wet Etching Machines
Wet etching machines are typically designed to be highly flexible, and a variety of customizations can be incorporated to better suit specific applications or improve overall performance. Some of the most common customizations include:
Dragon Etching Machine Equipment
Application Field: Used in the production of precision parts for electronics, aerospace, medical devices, and automotive industries. Characteristics: Utilizes chemical solutions to selectively remove material. Provides high precision and repeatability. Ideal for intricate designs and fine details. | ![]() |
- Inline Filtration Systems: Adding an inline filtration system helps ensure that the etching solution remains free of contaminants that could cause clogging or uneven etching. This is especially important for high-precision processes, where even the smallest particles can result in defects. For example, MEC (Metal Etching Corporation) offers a custom filtration system designed to ensure the solution stays clean and maintains consistent etching rates throughout production.
- Automated Loading and Unloading Systems: For high-volume production, automated loading and unloading systems can save time and reduce labor costs. These systems can be configured to handle different sizes and types of substrates, improving overall throughput. R.E. Miller & Co., another leader in the etching machine market, has developed automated material handling solutions that increase the productivity of their chemical etching machines, making them ideal for mass production environments.
- Multi-Stage Etching Chambers: For processes that require multiple stages, such as DES (Develop, Etch, Stripping) or SES (Strip, Etch, Strip), having the flexibility to configure multiple chambers in one system can help streamline production. Dragon Etching, a well-known supplier of wet etching equipment, offers machines that can be customized with multiple chambers, enabling businesses to run continuous production lines. Their machines are popular in PCB manufacturing, where multi-stage etching is required for high-precision designs.
- Temperature Control and Heating Systems: Accurate temperature control is crucial for ensuring uniform etching. Adding a heating system or an SST316 titanium heater (used by Dragon Etching) helps maintain the correct temperature for optimal etching speeds and quality. This is particularly useful in high-precision applications, where even minor fluctuations in temperature can impact the final product quality.
Customization is an essential part of ensuring that wet etching machines are capable of handling specific materials or achieving precise results. By tailoring the machine’s features and capabilities, manufacturers can not only improve the efficiency of their production process but also meet the unique demands of their customers.
How to Customize Wet Etching Machines Based on Production Needs
To customize a wet chemical etching machine effectively, it’s important to first understand the specific needs of your production line. This involves evaluating factors such as the type of material being processed, the volume of production, and the desired etching precision. Praxair Surface Technologies, known for their highly specialized equipment, works closely with their customers to design etching machines that are tailored to specific production needs. They offer custom solutions for industries such as aerospace and semiconductor manufacturing, where the etching process must meet highly detailed and exacting standards.
For example, if you’re working with very thin materials, such as flexible PCB substrates or materials that require low-temperature etching, a customized system might include features like thin material transport to handle delicate substrates or low-temp etching baths to avoid material degradation. Manufacturers like Praxair specialize in creating these customized systems to meet high-precision needs.
Another consideration when customizing your etching system is how to handle waste and chemicals. Waste management and chemical recycling systems, such as those offered by Wet Etched, ensure that used etchants are properly filtered and recycled for reuse, reducing both costs and environmental impact. This is particularly important for large-scale production environments where waste disposal can become a significant concern.
Real-World Examples of Customized Wet Etching Solutions
Several manufacturers have successfully implemented customized wet chemical etching machines to optimize their production lines. For instance, PCBWay, a well-established PCB manufacturing company, uses customized wet etching machines that integrate recipe-driven operation and automated temperature control. This customization has allowed PCBWay to streamline its production, achieving higher throughput and more consistent results across varied production runs.
Similarly, Chemcut has worked with semiconductor companies to design custom etching solutions that meet the high precision required for microelectronics. Their machines feature enhanced etching baths that can handle the demands of advanced semiconductor etching and integrate automated rinsing stations to prevent contamination during production. This ensures that delicate components like semiconductor wafers are etched with micron-level precision, making them suitable for use in high-performance electronics.