Wet etching is a fundamental process in microfabrication, allowing precise material removal to create intricate patterns and structures on substrates. The success of wet etching hinges on a series of design criteria that engineers and scientists must meticulously consider. In this blog, we will explore the key design criteria for wet etching, focusing on assumptions, dimensions, and the importance of hole size in achieving the desired results.
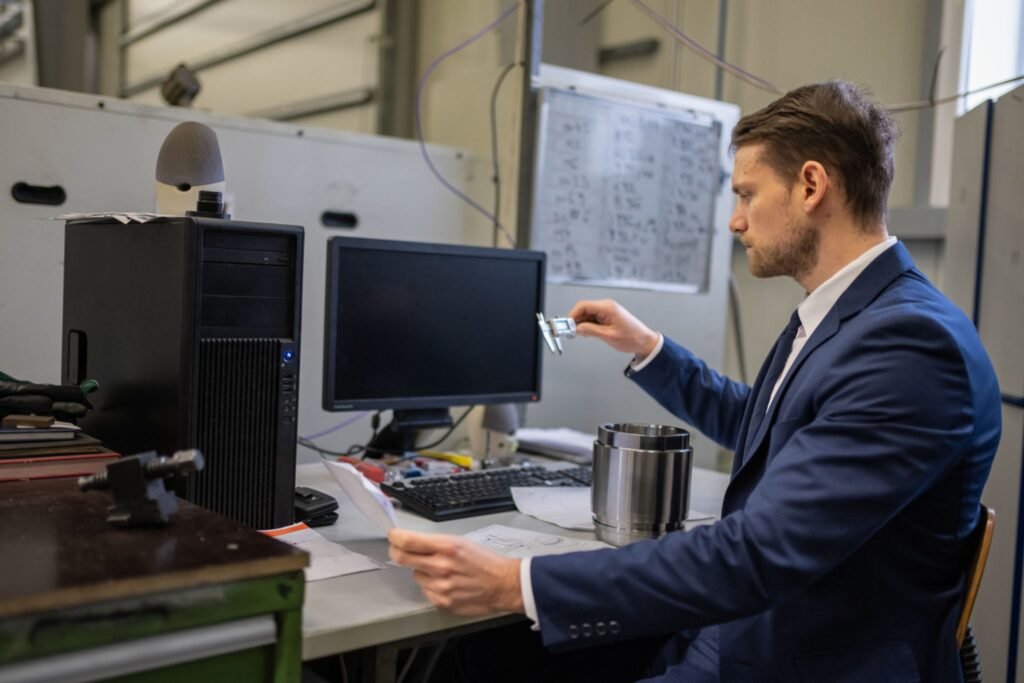
Design Criteria for Wet Etching
- Assumptions Matter: Before delving into the design criteria, it’s crucial to set the right assumptions. For instance, in the case of wet etching, we assume a specific thickness. For the purpose of this discussion, let’s consider a thickness ranging from 0.1mm.
- Etching design formulas versus material thickness: Assuming a material thickness of 0.1mm, one of the first design criteria to consider is the hole diameter. To ensure proper etching, it’s often recommended to make the hole slightly larger than the material thickness. In this case, 1.2 times the material thickness would be 0.1mm * 1.2 = 0.12mm. Therefore, if the material thickness is 0.1mm, the hole should be designed to have a diameter of at least 0.12mm.
- Material Choice: The choice of material plays a significant role in wet etching. Different materials react differently to etchants. Engineers must select materials that are compatible with the chosen etchant to ensure a successful process.
- Hole Size Matters: The size of the holes created during wet etching is a critical design criterion. Smaller holes may lead to incomplete material removal, while larger holes may compromise structural integrity. Typically, materials with a thickness of 100μm or less can accommodate holes with a diameter of 0.12mm or more. Larger holes often result in more aesthetically pleasing and structurally sound outcomes.
- Alignment and Precision: Achieving precise alignment of the etched features is vital. Design drawings should incorporate alignment markers or registration features to ensure accurate positioning during the etching process. This is particularly crucial when dealing with multilayer structures or when specific patterns must be aligned with pre-existing features.
- Minimum Feature Size: It’s advisable to establish a minimum feature size for your design drawings. For instance, it’s generally recommended that no marked details be smaller than 0.1mm. This corresponds to 100μm. Maintaining a minimum feature size helps ensure that the etching process can accurately replicate the desired patterns and structures without the risk of incomplete or distorted etching.
- Quality Control and Inspection: Design criteria should include provisions for quality control and inspection during and after the wet etching process. This involves specifying methods and tools for verifying that the final product meets the intended design specifications. Inspection processes may include optical microscopy, surface profilometry, or other measurement techniques to validate critical dimensions and surface finish.
Conclusion
Wet etching is a precise and versatile process used in microfabrication and nanotechnology. Proper design criteria are essential for achieving the desired results. By considering factors such as material thickness, hole size, material choice, alignment, surface finish, and etchant properties, engineers can ensure successful wet etching processes that meet the demands of various applications. The art of wet etching lies in the meticulous attention to these design criteria, resulting in finely etched structures that drive innovation across multiple industries.
If you have more discussions about etching standards, please contact me to add them and cite the source!