The adoption of Photo Chemical Machining (PCM) by top automotive brands is rooted in its unmatched precision, superior material performance, and profound impact on supply chain efficiencies. From the development of burr-free fuel injector nozzles with 50μm precision to facilitating a dramatic 40% weight reduction in hybrid vehicle battery contacts, PCM is proving indispensable in modern automotive manufacturing. Its compliance with IEC 62561 standards ensures safety and reliability, while its ability to consolidate parts streamlines production and assembly.
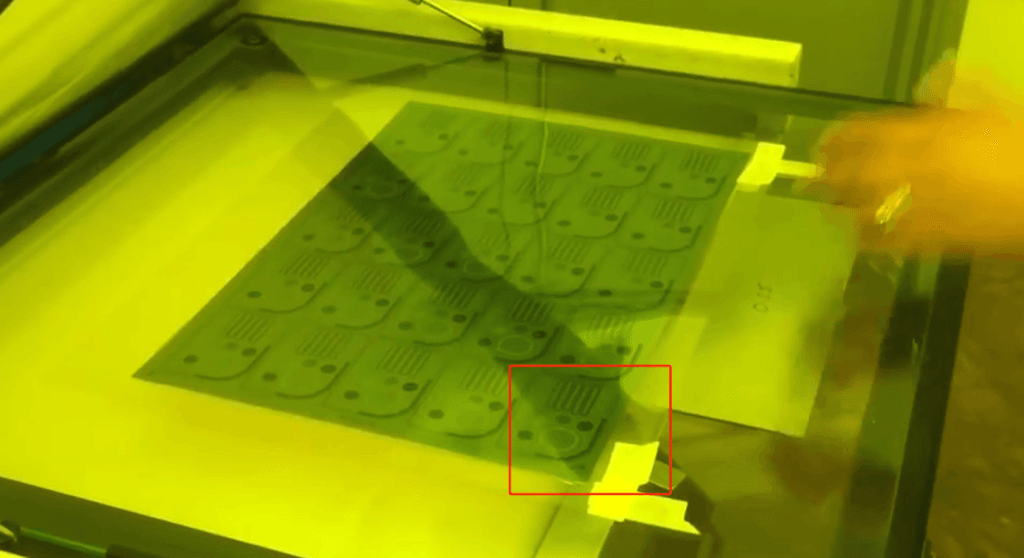
For decision makers seeking to optimize product performance and reduce manufacturing complexity, PCM offers a strategic advantage—paving the way for innovation and operational excellence in the competitive automotive industry.
Technical Spotlight: Precision Beyond Conventional Methods
Automotive systems demand uncompromised precision, especially when it comes to microcomponents. Consider burr-free fuel injector nozzles with a 50μm aperture precision produced using PCM. This level of accuracy is essential not only for optimal fuel atomization but also for ensuring consistent performance and reliability in high-pressure fuel systems. PCM’s capability to achieve such fine tolerances makes it an ideal choice for components where even minor imperfections could lead to reduced efficiency or component failure.
Material Performance: Enhancing Component Properties
Stainless steel is a material of choice for many automotive applications due to its durability and corrosion resistance. However, its performance can vary significantly based on the specific grade and fabrication process used. With 430 stainless steel, for example, PCM offers notable advantages by optimizing magnetic properties in EV motor laminations. This is particularly critical in electric vehicles, where motor efficiency and electromagnetic compatibility can be directly influenced by subtle changes in material properties. By maintaining a controlled chemical reaction during machining, PCM minimizes alterations in the microstructure, preserving the desired magnetic characteristics for EV applications.
Case Study: Weight Reduction in Hybrid Vehicle Battery Contacts
A recent case study highlights the transformative impact of PCM on hybrid vehicle battery contacts. Through selective etching, a manufacturer achieved a 40% weight reduction in battery contacts, a key factor in enhancing overall vehicle efficiency and performance. The controlled removal of material not only reduced the weight but also maintained the structural integrity required to handle high electrical loads and thermal stresses. This success story underscores PCM’s potential to deliver significant performance improvements while meeting the rigorous demands of automotive applications.
Regulatory Advantages: Meeting Industry Standards
Regulatory compliance is a major concern in the automotive sector, particularly for safety-critical components. PCM offers a distinct advantage in achieving IEC 62561 compliance for lightning protection systems. This standard ensures that components can withstand transient overvoltages and safeguard the vehicle’s electrical network. By delivering burr-free, precisely engineered components, PCM helps manufacturers meet stringent safety standards and streamline the certification process, ultimately reducing time-to-market for innovative safety solutions.
Supply Chain Impact: Streamlining Component Integration
Efficiency in the supply chain and manufacturing processes is essential for reducing costs and improving production flexibility. PCM’s ability to consolidate multiple stamped parts into a single, intricate component is a prime example of this efficiency. For instance, an HVAC sensor array—traditionally comprised of 12 separately stamped parts—can be manufactured as one integrated unit using PCM. This consolidation not only simplifies assembly processes but also reduces inventory complexity, lowers error rates, and minimizes potential points of failure across the system.
To further illustrate these advantages, consider the following comparative table:
Aspect | Traditional Stamping/Cutting | Photo Chemical Machining (PCM) |
---|---|---|
Precision | Limited by tool wear and mechanical tolerances | Achieves sub-50μm precision without physical tool degradation |
Surface Quality | Prone to burr formation and edge imperfections | Burr-free finishes critical for high-performance applications |
Material Integrity | Can alter magnetic and mechanical properties | Optimizes material performance (e.g., for 430 stainless steel) |
Component Integration | Multiple parts leading to complex assemblies | Consolidates 12 stamped parts into 1 integrated component |
Regulatory Compliance | May require additional processing for certification | Streamlines IEC 62561 compliance through precise fabrication |
Table: Comparative analysis of traditional manufacturing methods versus PCM in meeting automotive microcomponent requirements.
Industry Validation and Thought Leadership
Leading automotive brands and industry experts are increasingly validating PCM’s benefits through real-world applications and technical evaluations. Publications such as Automotive World and industry forums on SAE International frequently highlight PCM’s role in producing high-precision, reliable components that address the evolving demands of the automotive sector. These trusted sources provide further insights into how PCM is revolutionizing component manufacturing and supply chain management.