The Art of Decorative Etching
Chemical etching offers stainless steel a unique blend of artistic expression and durability, making it an ideal choice for luxury design applications. This technique, often used in architectural cladding, high-end retail, and luxury branding, transforms ordinary stainless steel into striking, aesthetic masterpieces. In this article, we will explore how decorative etching enhances the appearance of stainless steel while providing lasting performance and functionality.
Techniques (Photochemical Etching, Laser Engraving)
When it comes to creating decorative patterns on stainless steel, two primary techniques are used: photochemical etching and laser engraving.
Technique | Description | Best For |
---|---|---|
Photochemical Etching | Uses acidic solutions to etch fine details | Intricate designs, patterns, logos |
Laser Engraving | Uses a laser to burn designs into the metal | Simple logos, surface marking |
Photochemical etching offers greater precision and is ideal for fine details and custom artwork, while laser engraving is more suited for simpler designs or surface marking. For luxury brands seeking complex, unique patterns, photochemical etching is typically the preferred method.
Popular Patterns (Floral, Geometric, Custom Artwork)
In decorative applications, chemical etching allows for the creation of intricate patterns that elevate the aesthetic appeal of stainless steel. Some popular design choices include:
- Floral Patterns: Soft, flowing designs ideal for high-end interior design and luxury architecture.
- Geometric Patterns: Sharp, modern designs perfect for contemporary retail displays and architectural facades.
- Custom Artwork: Unique and personalized designs that bring artistic expression to life, often used for luxury branding or exclusive interior features.
Surface Finishes and Textures
The surface finish plays a vital role in enhancing the overall aesthetic of etched stainless steel. Different finishes can be achieved, depending on the desired look and feel of the final product.
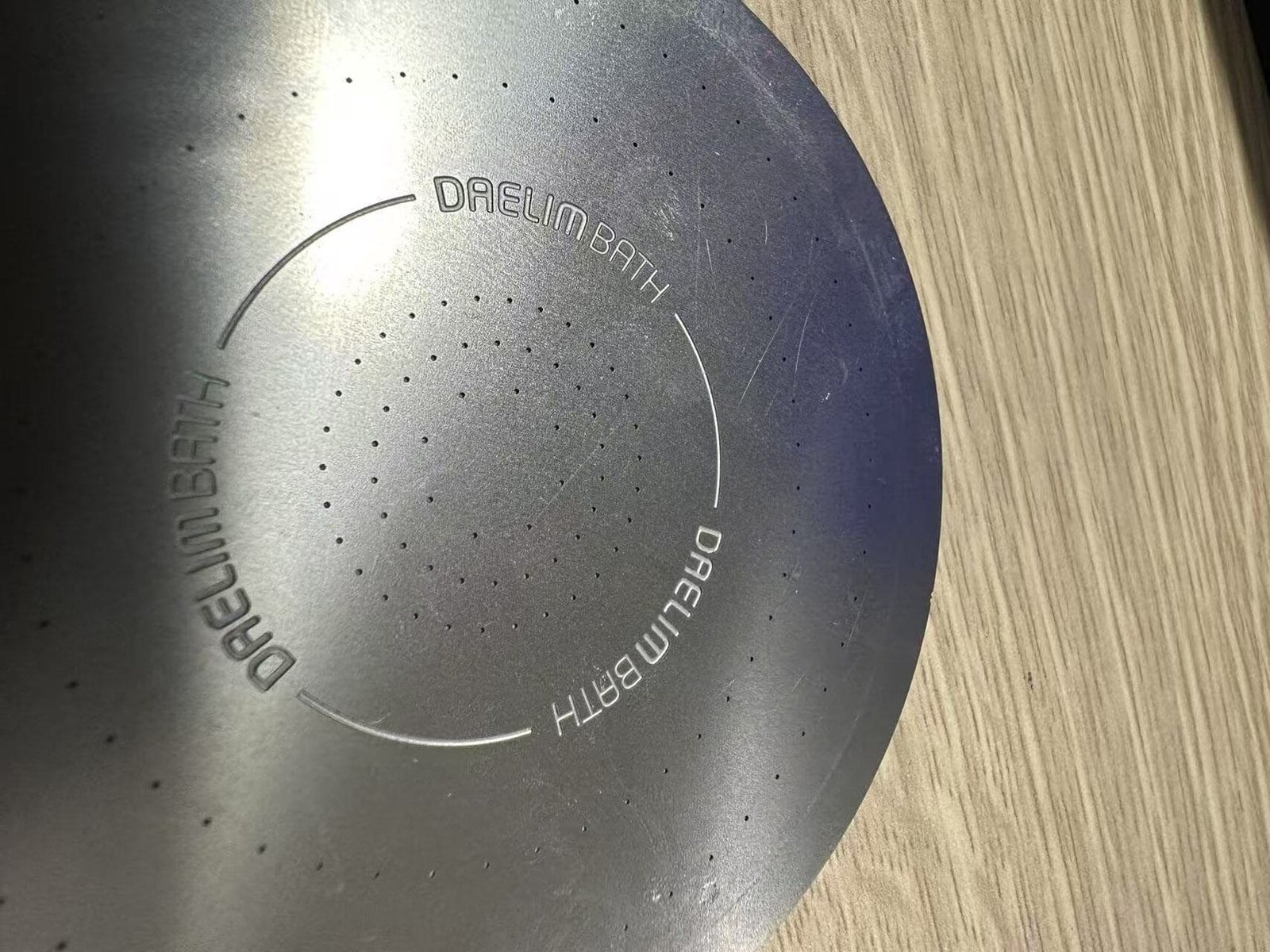
Matte vs. Glossy Etched Surfaces
Finish | Characteristics | Best For |
---|---|---|
Matte Etched Surface | Soft, non-reflective, smooth appearance | Modern, minimalist designs, industrial applications |
Glossy Etched Surface | Reflective, shiny finish, enhances intricate patterns | Luxury interiors, high-end branding |
A matte finish is often used in industrial or contemporary designs where a non-reflective surface is desired. A glossy finish is typically preferred for luxury applications, as it accentuates etched details and adds a touch of elegance and sophistication.
Combining Etching with Brushing/Polishing
To further enhance the texture and appearance of etched stainless steel, many designers combine etching with brushing or polishing. Brushed finishes offer a subtle texture, ideal for architectural cladding or luxury furniture, while polished finishes create a smooth, mirror-like appearance that adds a premium look to high-end designs.
Combining etching with these finishes creates a balance between artistry and durability, offering a unique look that stands out in luxury spaces or high-end retail environments.
Applications in Luxury Design
Chemical etching is widely used in various luxury design applications, from architectural features to high-end retail items. The versatility of etching allows for the creation of both functional and decorative elements in stainless steel, making it an excellent choice for designers in the luxury market.
Architectural Cladding (Elevator Panels, Wall Art)
Architects frequently use etched stainless steel for cladding in elevators, wall art, and other architectural features. The ability to create custom designs and patterns makes etching an excellent choice for projects requiring unique visual appeal. Etched elevator panels or wall art can transform a space, combining art with functionality.
High-End Retail (Display Cases, Signage)
In the world of luxury retail, etched stainless steel is used to create elegant display cases and signage that stand out in high-end stores. The durability of stainless steel ensures that these pieces retain their premium appearance over time, even in high-traffic retail environments.
Durability in Harsh Environments
Stainless steel is already known for its durability and corrosion resistance, but chemical etching further enhances these qualities. When used in the right conditions, etched stainless steel can withstand harsh environments, including exposure to the elements, without compromising on appearance.
Corrosion Resistance (Marine and Outdoor Use)
Chemical etching enhances the corrosion resistance of stainless steel, making it suitable for marine environments and outdoor applications. Whether it’s for marine-grade signage or architectural elements exposed to the elements, etched stainless steel provides long-lasting performance while maintaining its aesthetic appeal.
UV Stability for Long-Term Color Retention
For outdoor or high-exposure applications, UV stability is an essential factor. Etched stainless steel maintains its color and finish even when exposed to direct sunlight for extended periods, ensuring that the artistic designs remain vibrant and intact for years to come.
Custom Branding Opportunities
Etched stainless steel offers significant potential for custom branding, providing luxury brands with the ability to create unique logos and markings on their products. This enhances brand identity while offering functional and aesthetic benefits.
Etched Logos and Serial Numbers
One of the most common applications of chemical etching is for creating etching logos and serial numbers on products, ensuring brand visibility and easy identification. This is especially useful for luxury goods, where branding is key to maintaining a premium image.
Anti-Counterfeiting Features
Chemical etching also offers a way to incorporate anti-counterfeiting features into products. Unique etched designs or serial numbers can help authenticate luxury items, protecting the brand and ensuring customers receive genuine products.