AI-Driven Process Optimization
The integration of Artificial Intelligence (AI) into the aluminum etching process is transforming the industry. Here are a few ways AI is enhancing etching:
Machine Learning for Etch Rate Prediction
AI and machine learning (ML) algorithms can now predict etch rates with greater accuracy. These systems analyze historical data to forecast how various factors such as etchant composition, temperature, and dwell time will influence the etch process, allowing for optimized etching conditions. By adjusting parameters in real time, AI ensures consistency and precision in the final product.
Real-Time Defect Detection with Vision Systems
Vision systems powered by AI are also enabling real-time defect detection during the etching process. These systems utilize high-resolution cameras and image analysis algorithms to identify anomalies like under-etching, over-etching, or uneven patterns, allowing operators to make immediate adjustments to maintain quality.
IoT-Enabled Etching Machines
The application of Internet of Things (IoT) technologies in aluminum etching is enhancing operational efficiency and reducing downtime. Key developments include:
Remote Monitoring of Etchant pH and Temperature
IoT-enabled etching machines can continuously monitor critical parameters like pH and temperature in the etching solution. This allows operators to adjust the chemical environment remotely, ensuring optimal etching conditions and improving consistency in large-scale production.
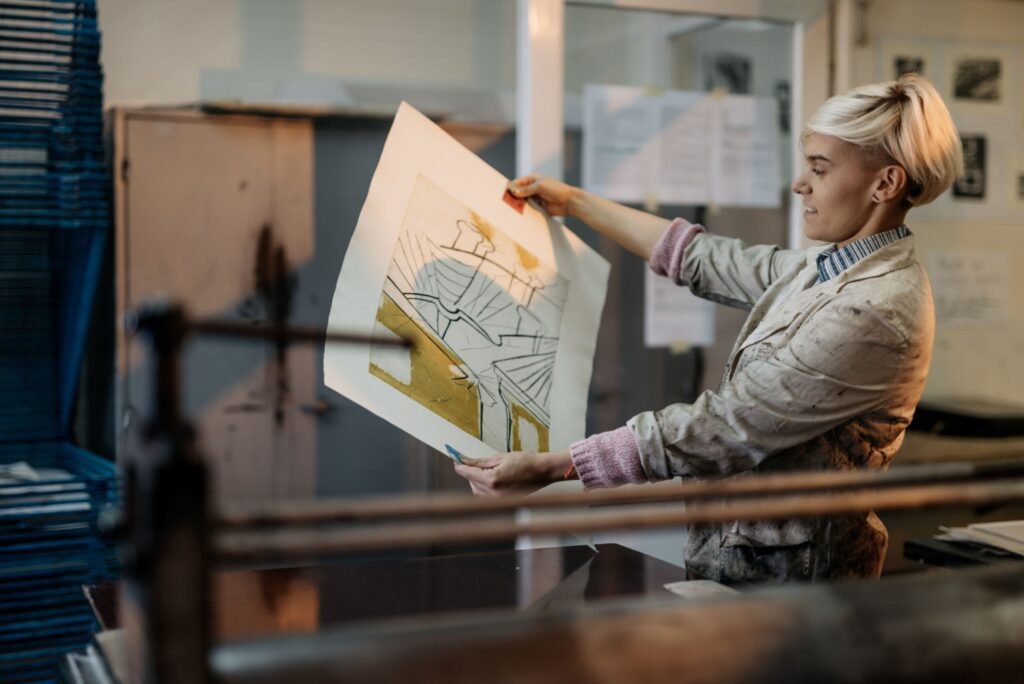
Predictive Maintenance to Reduce Downtime
IoT devices can also track the performance of etching machinery, providing data on wear-and-tear, vibrations, and other operational metrics. By utilizing predictive maintenance algorithms, manufacturers can predict machine failures before they occur and schedule timely maintenance, reducing unexpected downtime and ensuring smoother production cycles.
Advanced Applications
Aluminum etching is expanding beyond traditional applications, leading to the development of advanced materials and innovative devices:
Nanotextured Surfaces for Anti-Reflective Coatings
Etching is being used to create nanotextured surfaces for applications like anti-reflective coatings. These surfaces can reduce light reflection, making them ideal for use in solar panels, cameras, and optical devices. The precision of chemical etching allows for the creation of highly defined microstructures at the nanoscale, leading to better performance in these industries.
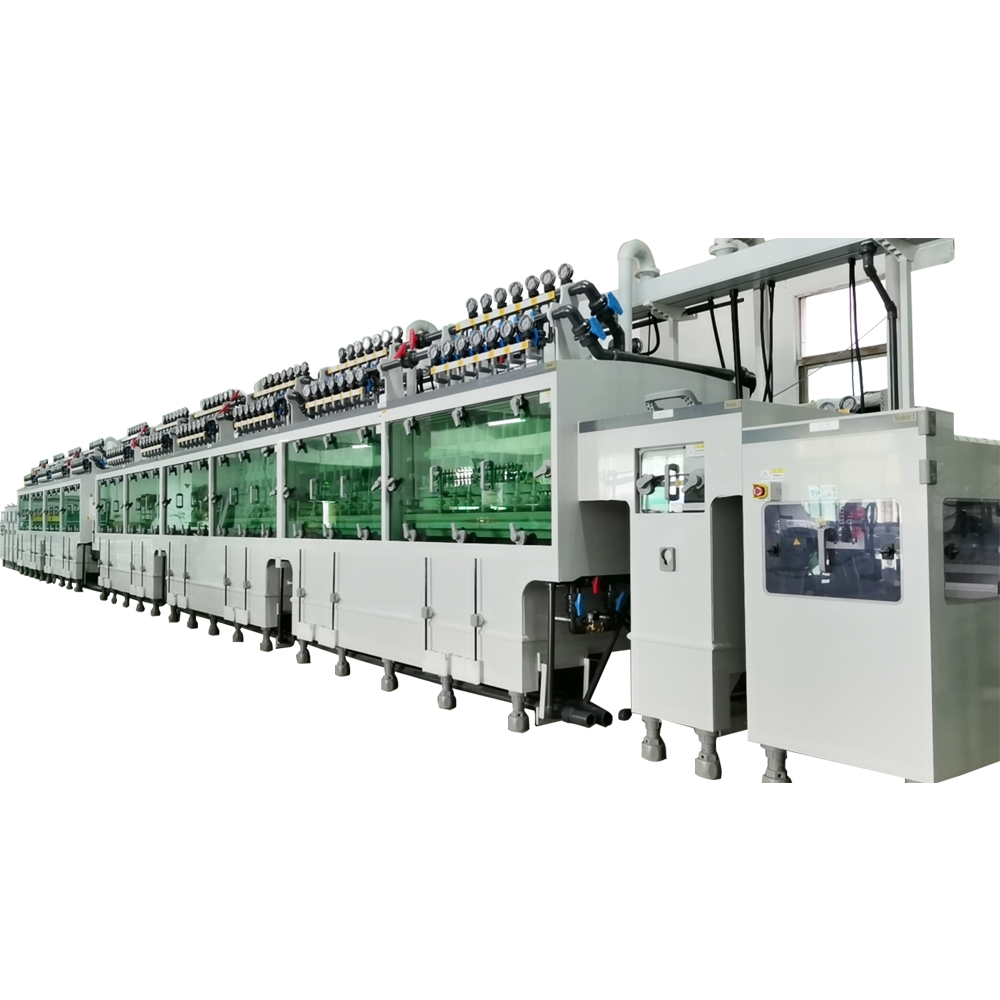
Biomedical Devices (Etched Microfluidic Chips)
In the biomedical sector, etched microfluidic chips are gaining popularity. These chips are essential components of diagnostic tools and lab-on-a-chip devices, enabling precise fluid control for biological assays. Aluminum etching is used to create the intricate channels required in these chips, offering high precision and cost-effectiveness compared to alternative manufacturing methods.
Hybrid Manufacturing Techniques
The future of aluminum etching also involves hybrid manufacturing techniques, combining the strengths of multiple technologies to create innovative products.
Combining Etching with 3D Printing for Hybrid Parts
The fusion of chemical etching with 3D printing technology is enabling the creation of hybrid parts with complex geometries and superior surface finishes. 3D printing can be used to create the base structure of a component, while chemical etching refines the surface, adds intricate details, and improves material properties. This combination has been especially beneficial in industries like aerospace and medical devices where both structural integrity and fine surface finishes are required.
Market Trends
Looking ahead, the aluminum etching industry is poised for significant growth, driven by technological advancements and rising demand in various sectors.
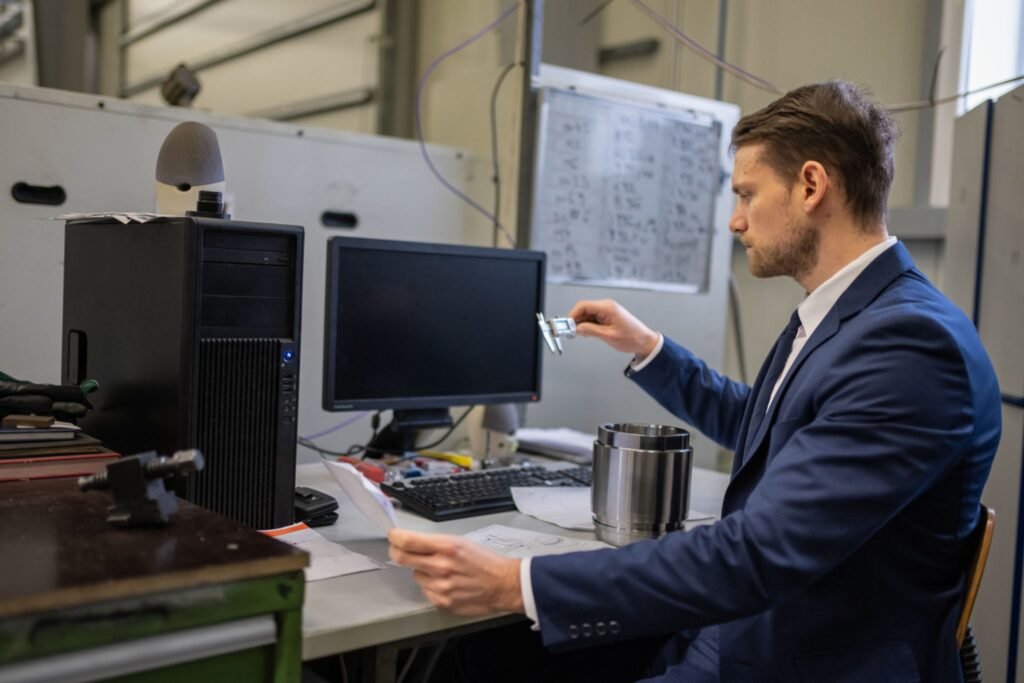
Rising Demand in EVs and Renewable Energy Systems
With the growing focus on electric vehicles (EVs) and renewable energy systems, aluminum etching is seeing a rise in demand for applications like battery housings, heat exchangers, and solar panel components. The light weight, corrosion resistance, and formability of aluminum make it a preferred material in these industries, while precision etching ensures that parts meet the high standards of modern manufacturing.
Asia-Pacific’s Dominance in Aluminum Etching Tech
The Asia-Pacific region, particularly countries like China, Japan, and South Korea, continues to dominate the aluminum etching market. These nations have a strong presence in electronics manufacturing, automotive production, and renewable energy, where aluminum etching is widely used. Innovations from these regions are expected to drive future growth in the global aluminum etching market.
For example, companies like Samsung and Toyota have integrated advanced etching technologies into their manufacturing processes, enhancing performance and reducing costs. Source: TechCrunch
In conclusion, AI, IoT, and hybrid manufacturing techniques are revolutionizing the aluminum etching process, leading to enhanced precision, efficiency, and new applications across industries. As demand grows in key sectors such as EVs and renewable energy, innovations in etching technology will continue to shape the future of manufacturing.