Thermal Performance: PI’s High Heat vs. PET’s Affordability
When selecting the right substrate for a film heating element, the thermal performance of the material is crucial. Polyimide (PI) and Polyethylene Terephthalate (PET) offer distinct advantages depending on the temperature range required for your application.
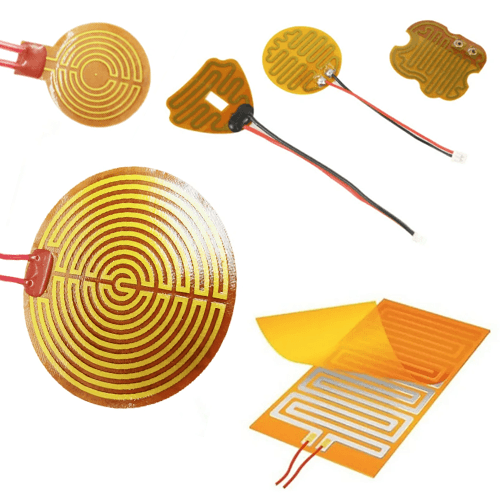
- PI (Polyimide): Known for its exceptional thermal stability, PI can withstand temperatures up to 260°C without losing its structural integrity. This makes it ideal for high-performance applications, such as automotive heaters, aerospace components, and industrial machinery, where the heating element must perform in extreme conditions.
- PET (Polyethylene Terephthalate): PET, on the other hand, has a much lower maximum operating temperature, typically around 90°C. It is suitable for low to medium-temperature applications, making it a popular choice for consumer goods such as heated mugs, beauty devices, or wearable products, where temperature requirements are not as demanding.
When deciding between PI and PET, consider the heat demands of your application. If you need high heat resistance for automotive or industrial use, PI is the preferred choice. However, for cost-effective solutions in consumer electronics or low-temperature heating, PET can provide a more affordable yet reliable option.
Durability in Harsh Environments
Durability in extreme conditions is another important factor in choosing the right material. Both PI and PET have distinct properties that make them suitable for different environments.
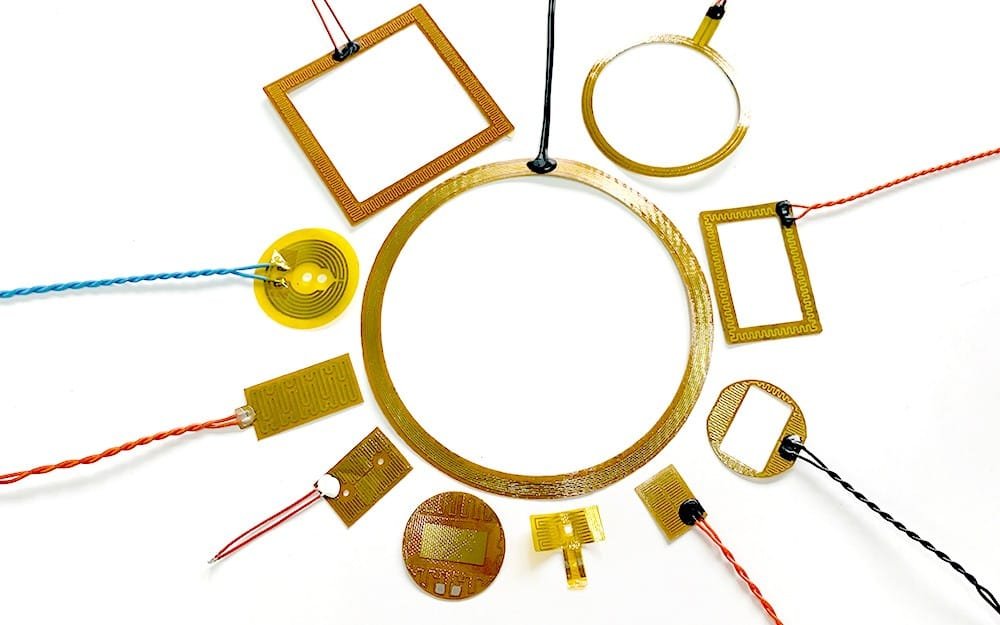
- PI: One of the standout features of PI is its chemical resistance, making it ideal for use in harsh chemical environments. It is commonly used in medical sterilization, industrial cleaning systems, and aerospace applications where exposure to chemicals, high temperatures, and even radiation is common. Its ability to maintain structural integrity under these conditions makes it a top choice for demanding, high-end applications.
- PET: While PET does not have the same high level of chemical resistance as PI, it offers semi-transparency and a high tensile strength, making it an excellent option for screen heaters and other applications where visibility and mechanical strength are important. For example, PET-based heaters are commonly used in electronic devices where the heater needs to be lightweight and efficient, but the environment is not as chemically harsh.
For medical devices, PI is more suitable due to its durability in sterilization environments. In contrast, for consumer electronics and light-duty applications, PET provides a balance between durability and functionality, especially when transparency is required.
Flexibility and Weight Considerations
When designing a heating element, flexibility and weight are key factors, especially when the heater needs to fit into compact or curved spaces.
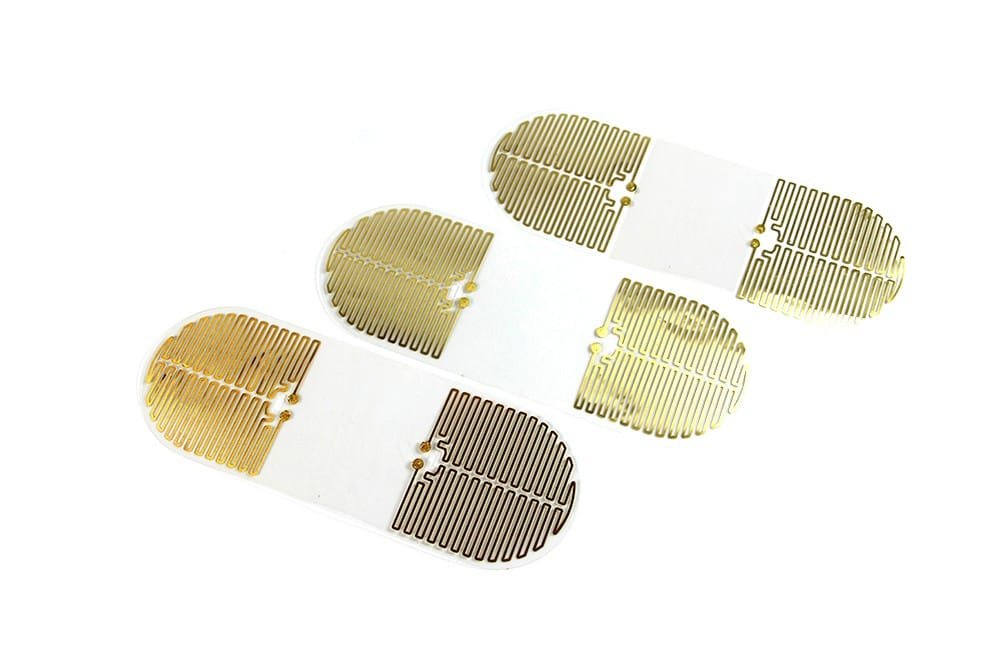
- PI: PI-based heaters are highly flexible, making them perfect for applications that require the heating element to conform to curved surfaces. Beauty tools, for example, often use PI heating films because they can bend around the contours of a device, ensuring even heat distribution. Additionally, PI is lightweight, which is essential when designing devices that need to remain portable and easy to use.
- PET: While PET is also flexible, it is not as bendable as PI. This makes PET heaters ideal for flat applications like ceramic mugs or screen heaters. PET offers rigidity and mechanical strength, which are important in situations where the heater will be placed on a flat, stable surface and must maintain its shape over time.
If the application involves curved or flexible surfaces, such as in wearable tech or beauty equipment, PI is a better fit. For flat applications, like in kitchen appliances or consumer electronics, PET offers the required rigidity and strength.
Cost Analysis: When to Choose PET
The choice between PI and PET is not only determined by performance but also by cost considerations. PET is generally much more affordable than PI, making it an attractive option for high-volume, low-temperature applications.
- PET is ideal for mass-produced products where low-cost and high efficiency are the primary concerns. Heated cups, wearable devices, and heating pads often use PET-based heaters because they provide an affordable solution that meets the required heating performance without breaking the budget.
- PI, while offering superior thermal performance, is a more expensive material, making it better suited for applications that demand high performance and can justify the higher cost, such as in automotive, aerospace, and high-performance medical devices.
For applications like heated mugs, wearable tech, or consumer products that need to be produced in large volumes, PET is often the best choice. PI, on the other hand, is more suited to niche markets where its high performance and durability justify the higher price.
Hybrid Solutions: Combining PI and PET
In some cases, the best solution involves combining the properties of both PI and PET to create a hybrid heater that balances performance and cost. A common approach is to use PI for the areas that need high heat resistance and PET for the insulation or non-heating areas.
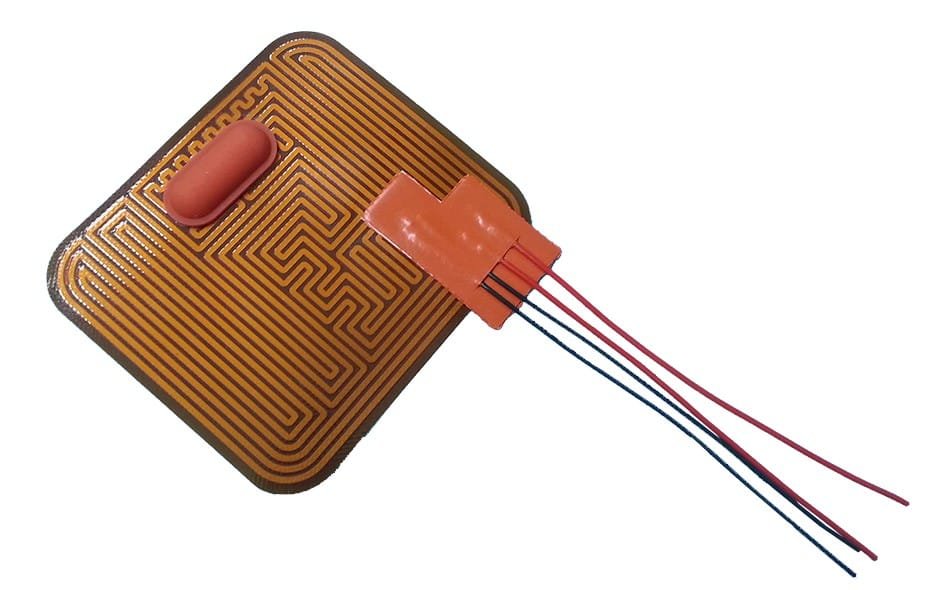
- PI for Heat Zones: The PI layer can be used in high-temperature zones or critical heating areas where high performance is needed, such as battery heating pads or aerospace applications.
- PET for Insulation: The PET layer can be used in areas where insulation is needed, ensuring that heat is not wasted or dissipated. PET can also serve as an economical outer layer, reducing overall costs while maintaining a high level of efficiency.
By layering PI and PET, manufacturers can create cost-effective, high-performance heating solutions that meet the exact needs of the application. This approach allows for the use of the superior properties of PI where necessary while keeping costs down with PET in less demanding areas.