Why Nano-Level Etching is a Game Changer
As electronic devices shrink in size while increasing in complexity, lead frame technology must evolve. The demand for ultra-precise, high-performance lead frames is pushing traditional etching methods to their limits. Nano-level etching, with its ability to achieve sub-micron accuracy (<1μm), is now at the forefront of next-generation semiconductor packaging.
This article explores the latest advancements in etching techniques, materials, and Industry 4.0-driven innovations that are redefining lead frame manufacturing.
Pushing the Limits of Precision
1. Laser-Assisted Etching: Enhancing Accuracy Beyond Traditional Methods
Traditional photochemical etching offers high precision, but combining laser-assisted techniques can further reduce overlay errors to <1μm.
Etching Method | Accuracy | Key Advantages |
---|---|---|
Conventional Chemical Etching | ±5μm | Cost-effective, scalable |
Photo-Chemical Etching with Multi-Layer Alignment | ±2μm | High resolution, suitable for fine-pitch designs |
Laser-Assisted Chemical Etching | <1μm | Extreme precision, minimizes undercutting |
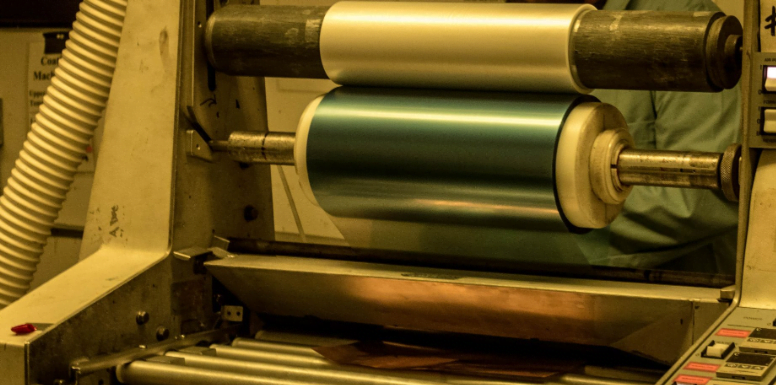
🔹 Case Study: Companies like Mitsubishi Electric have pioneered hybrid laser-assisted etching for ultra-fine interconnects, enhancing signal integrity in high-speed electronics (source).
2. Multi-Layer Alignment: Tackling Complex Lead Frame Structures
Multi-layered lead frames, crucial for 3D packaging and high-frequency RF applications, require perfect alignment to prevent signal loss or electrical interference.
✔ Solution: New optical alignment systems now ensure multi-layer etching errors stay below 1μm, a 10x improvement over traditional methods.
The Rise of Ultra-Thin Clad Metals
With the rise of 5G, IoT, and automotive radar, lead frames need to handle higher frequencies and harsher environments. This has led to the adoption of ultra-thin clad metals, combining the best properties of multiple materials.
Material | Composition | Application |
---|---|---|
Cu/Fe/Ni Composite | Copper core for conductivity, iron for rigidity, nickel for corrosion resistance | 5G base stations, radar modules |
BeCu Alloy | Beryllium copper for high elasticity and fatigue resistance | Wearables, medical sensors |
Mo-Cu Alloy | Molybdenum for thermal management, copper for conductivity | High-power semiconductors, EV battery systems |
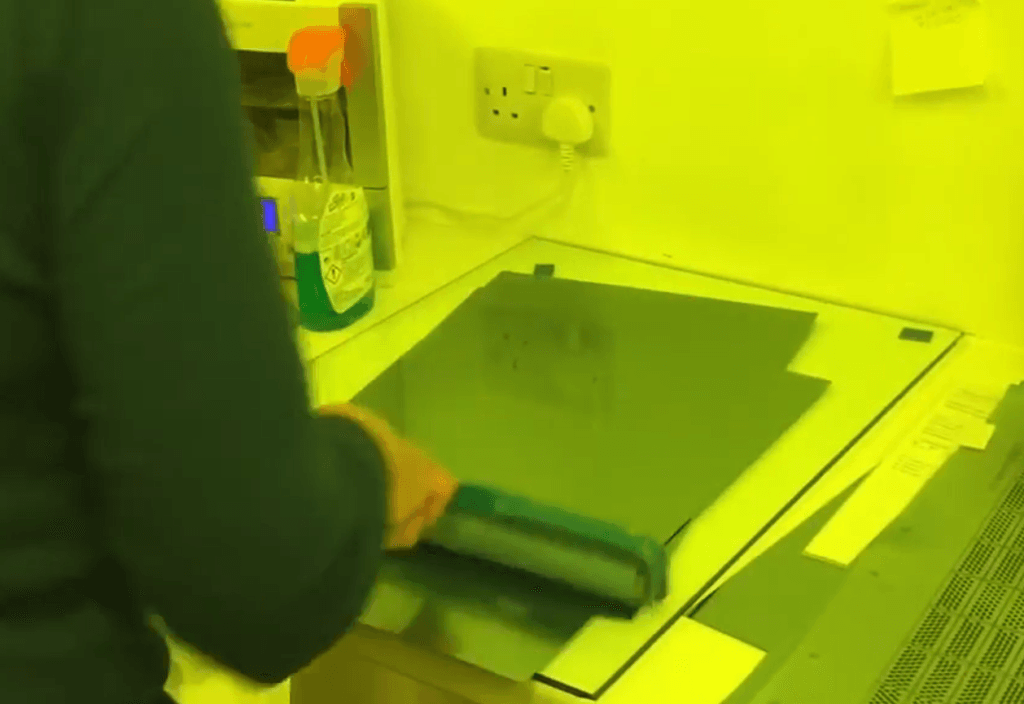
🔹 According to a recent study by Atotech, the use of Cu/Ni multilayered lead frames has led to 30% better thermal stability in automotive electronics (source).
FEM for Stress Distribution Analysis
As lead frames become thinner and more intricate, mechanical stress during etching and stamping must be carefully managed.
✔ Finite Element Method (FEM) simulations help predict stress concentration points, minimizing deformation.
✔ Hybrid manufacturing models (etching + micro-stamping) are now optimized using AI-driven FEM software, allowing manufacturers to reduce failure rates by up to 25%.
📌 Example: Engineers at Infineon Technologies use FEM-driven etching simulations to optimize high-reliability lead frames for automotive ICs (source).
Smart Etching Tanks for Real-Time Monitoring
With Industry 4.0, etching processes are becoming smarter and more efficient.
IoT-Enabled Etching Tanks: Key Innovations
✔ Real-time pH & ion concentration sensors – Ensure consistent etching quality.
✔ Automated chemical replenishment – Reduces waste and improves process control.
✔ AI-driven defect detection – Uses machine learning to spot inconsistencies before they cause defects.
🔹 Case Study: Texas Instruments has implemented IoT-enabled chemical etching in their lead frame production, resulting in 15% lower defect rates and 20% higher yield (source).
Anti-Corrosion Nanostructured Surfaces
A recent patent, US20230174521A1, details nanostructured coatings designed to improve the corrosion resistance of etched metal surfaces.
✔ Why it matters: Lead frames are exposed to harsh environments (moisture, oxidation, heat).
✔ Solution: Nano-coatings significantly improve durability, reducing corrosion-related failures by over 50%.
🔹 Patent Reference: US20230174521A1 – Anti-Corrosion Nanostructured Surfaces.
The Future of Nano-Level Etching in Lead Frames
The move toward nano-precision etching is breaking technological barriers, enabling smaller, faster, and more reliable lead frames for the next generation of electronics.
✔ Laser-assisted techniques & multi-layer alignment improve precision to sub-micron levels.
✔ Advanced clad metals enhance thermal & electrical performance for 5G and automotive applications.
✔ Smart, AI-driven etching systems drive efficiency and reduce defects.
✔ Patented nanostructured coatings ensure longer-lasting, corrosion-resistant lead frames.
🚀 With these innovations, the future of lead frame manufacturing is heading toward unparalleled precision and efficiency—powering the next wave of cutting-edge electronics.