In today’s fast-paced manufacturing environment, choosing the right fabrication method can make the difference between on‑time, on‑budget delivery and costly delays. Advanced chemical etching has emerged as the go‑to process for producing intricate, burr-free metal parts, outpacing traditional laser cutting in several key areas.
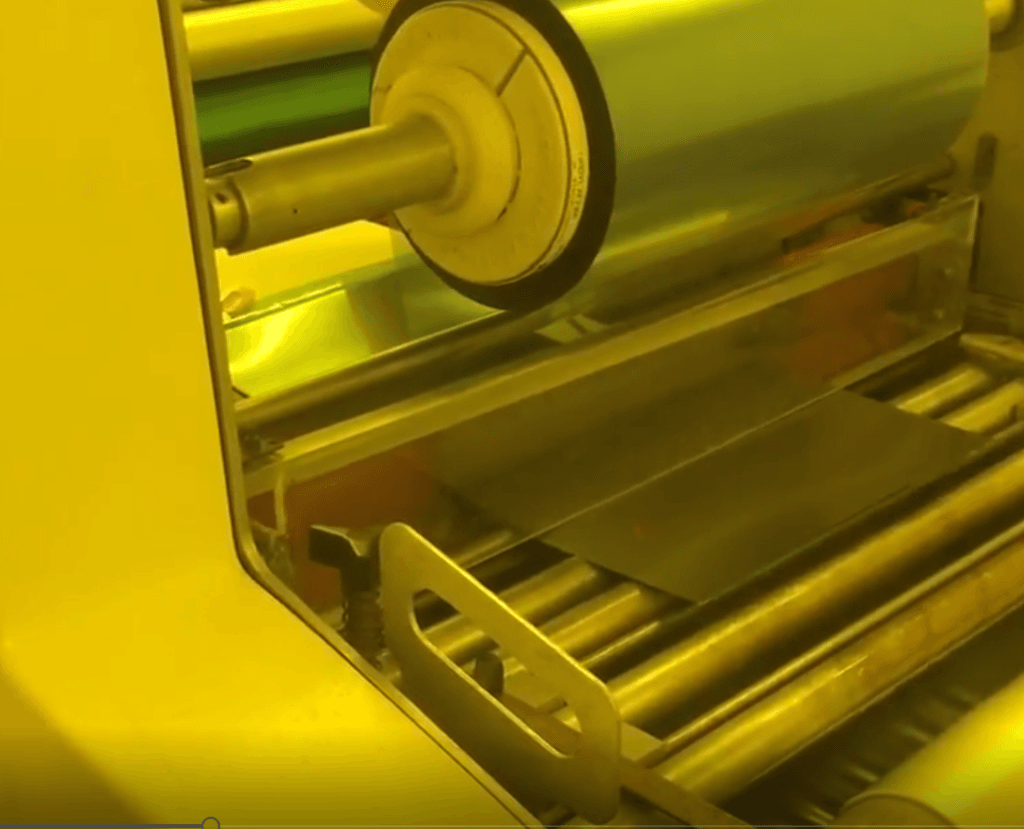
Head-to-Head Comparison
Below is a side‑by‑side look at how chemical etching stacks up against laser cutting for both low‑volume and high‑volume runs:
Aspect | Advanced Chemical Etching | Laser Cutting |
---|---|---|
Cost per Part | – Low-volume: $0.50–$2.00 per part (no hard tooling) – High-volume: $0.10–$0.50 per part | – Low-volume: $5–$20 per part (high setup costs) – High-volume: $0.50–$1.50 per part |
Lead Time | 3–7 days (tooling via photo tools) Rapid design iterations without downtime | 1–2 days per batch, but setup and edge‑quality validation can add extra days |
Design Limitations | No heat‑affected zone, enabling ultra‑fine features down to 20 μm Unlimited nest layouts | Heat‑affected zone (HAZ) may distort edges; minimum feature size ~100 μm |
Design Freedom for Intricate Patterns
Chemical etching’s greatest strength lies in design flexibility:
- Burr‑Free, Stress‑Free Parts: Since there’s no mechanical contact or heat input, etching delivers perfectly smooth edges and zero residual stress, critical for components like microfluidic channels or fine meshes.
- Ultra‑Complex Geometries: From high‑density perforation patterns to tortuous cooling channels, chemical etching can effortlessly produce features that would be impossible—or prohibitively expensive—with laser cutting.
“We switched to chemical etching for our mesh filters and saw a dramatic improvement in flow consistency and surface finish,” notes a design engineer at Acme Filters, an industry leader in precision filtration.
For more on design capabilities, see the deep‑dive at Modern Machine Shop on micro‑etching techniques.
Real-World Example: Reducing Prototyping Costs in Medical Devices
A prominent medical device company leveraged advanced chemical etching to produce prototype titanium surgical tool components:
- 40% Reduction in Prototyping Costs: By eliminating the need for expensive CNC setups and hard tooling, etching cut prototype expenses from $12,000 to $7,200 per design iteration.
- Faster Iterations: Photo tools were fabricated in under 48 hours, compared to 1–2 weeks for CNC fixtures, accelerating the design validation cycle.
This case illustrates how chemical etching not only slashes costs but also compresses development timelines, letting product teams move quickly from concept to clinical testing.
Sustainability Edge: Closed‑Loop Chemical Recycling
Environmental impact is no longer a secondary concern. Advanced etching lines now employ closed‑loop etchant regeneration, achieving up to 70% reduction in chemical waste:
- Etchant Regeneration: Spent ferric chloride is continuously filtered and re‑constituted, extending its usable life by up to 10×.
- Less Wastewater: Recycling systems minimize discharge, helping manufacturers meet stringent local and global regulations.
According to a report from Thomas Insights, companies implementing closed‑loop etching systems have reduced both operating costs and environmental footprint—without compromising precision.
Tooling Tips for Optimized CAD Files
To fully realize the benefits of chemical etching, design your CAD files with the following guidelines:
- Minimum Feature Size: Specify features no smaller than 20 μm to ensure consistent etch depth.
- Draft Angles: Avoid steep angles in mask layouts; use shallow tapers (1–2°) to facilitate clean resist application.
- Nest Layouts: Maximize sheet utilization by nesting parts closely—chemical etching supports virtually any 2D arrangement without added cost.
- Tolerance Bands: Define tolerances of ±5 μm for critical dimensions to match the process capability.
By adhering to these best practices, you’ll minimize rework and achieve the highest quality in your etched components.