Chemical engraving of stainless steel is a precise process that requires specialized equipment and meticulous attention to detail. This article explores the essential equipment required, estimated costs, surface treatment processes, and the selection of engraving solutions. Understanding these key elements will help you make informed decisions for your stainless steel engraving projects.
Table of Contents
- Equipment and Cost Evaluation
- Surface Treatment Processes and Equipment
- Selection of Stainless Steel Engraving Solutions
- Stainless Steel Grades and Engraving Parameters
- Chemical Engraving Stainless Steel: Detailed Steps
- If you need a OEM factory to realize your project, please do not hesitate to contact us.
- Wet Stainless Steel etching
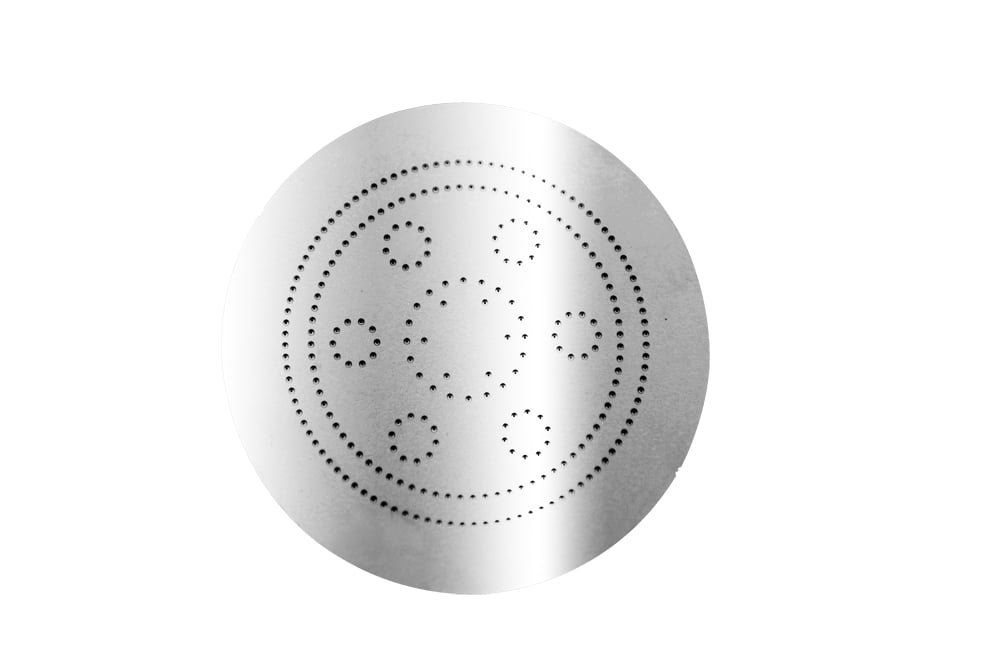
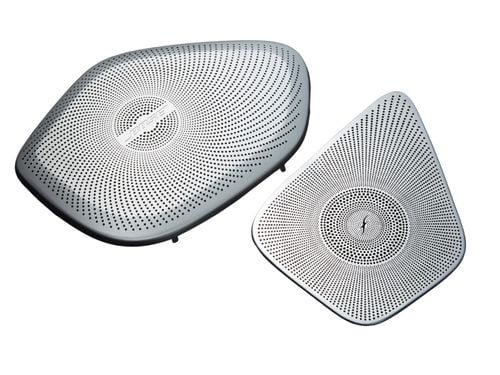
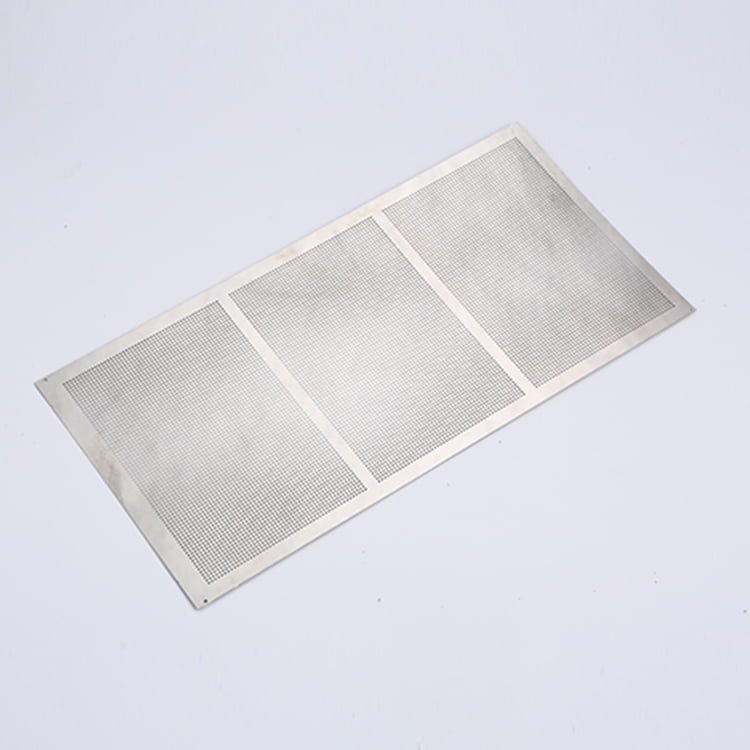
Equipment and Cost Evaluation
For a chemical engraving facility processing 5000 square meters per month, the following equipment is necessary:
Equipment Name | Estimated Price | Usage Description |
---|---|---|
Cleaning line | $4000/M | Used to clean the stainless steel surface before engraving. This ensures that any contaminants are removed, providing a clean surface for the engraving process. |
Manufacturer: Dragonetching <br> Manufacturer Website: www.dragonetching.com | ||
Painting and drying line | $25,000 | Applies a resist paint to the stainless steel surface and dries it, preparing it for the exposure process. |
Manufacturer: Dragonetching <br> Manufacturer Website: www.dragonetching.com | ||
Exposure line | $18,000 | Exposes the resist-covered stainless steel to light through a photomask, transferring the desired pattern onto the stainless steel. |
Manufacturer: Dragonetching <br> Manufacturer Website: www.dragonetching.com | ||
Developing line | $4000/M | Develops the exposed stainless steel by removing the unexposed resist, revealing the areas to be engraved. |
Manufacturer: Dragonetching <br> Manufacturer Website: www.dragonetching.com | ||
Stainless Steel Engraving line | $4000/M | The core of the process, this equipment engraves the exposed stainless steel areas using the selected engraving solution. |
Manufacturer: Dragonetching <br> Manufacturer Website: www.dragonetching.com | ||
Stripping line | $4000/M | Removes the remaining resist after the engraving process, leaving behind the final engraved stainless steel pattern. |
Manufacturer: Dragonetching <br> Manufacturer Website: www.dragonetching.com |
Surface Treatment Processes and Equipment
Surface treatment is essential for preparing the stainless steel surface and achieving the desired finish. Here are recommended surface treatment processes and equipment:
Equipment Name | Estimated Price | Usage Description |
---|---|---|
Grinding machine (Automatic) | $140,000 | Used to grind the stainless steel surface, ensuring a smooth and uniform finish before engraving. |
Manufacturer: Dragonetching <br> Manufacturer Website: www.dragonetching.com | ||
Grinding machine (Manual) | $70,000 | Provides a manual grinding option for smaller batches or specialized applications. |
Manufacturer: Dragonetching <br> Manufacturer Website: www.dragonetching.com |
Selection of Stainless Steel Engraving Solutions
Engraving stainless steel using chemical solutions involves careful selection of etchants. The choice depends on the specific application and desired engraving characteristics. Here are some commonly used etchants for stainless steel:
- Copper Chloride (CuCl2) Engraving Solution: Effective for stainless steel, copper chloride provides a controlled engraving rate and is commonly used for detailed and intricate designs.
Stainless Steel Grades and Engraving Parameters
The table below lists different stainless steel grades, along with their engraving parameters and estimated results. All samples have the same thickness, width, and length for uniform comparison.
Stainless Steel Grade | Chemical Engraving Temperature (°C) | Chemical Engraving Solution Concentration (%) | Estimated Chemical Engraving Depth (µm) | Chemical Engraving Quality |
---|---|---|---|---|
304 | 45 | 40 | 20 | High |
316 | 45 | 40 | 18 | High |
430 | 45 | 40 | 22 | Medium |
201 | 45 | 40 | 25 | Medium |
410 | 45 | 40 | 15 | High |
Chemical Engraving of Stainless Steel: Detailed Steps
1. Raw Material Selection
Start with selecting high-quality stainless steel. Common grades include 304 and 316 due to their corrosion resistance and durability.
2. Cleaning Line
Proper cleaning is crucial to remove any contaminants that could affect the engraving process.
Steps:
- Water Rinse: Use deionized (DI) water to rinse the stainless steel sheets. DI water helps avoid any impurities.
- Cleaning Solution: Immerse the stainless steel in an alkaline cleaning solution to remove oils, grease, and other contaminants.
- Rinse: Rinse again with DI water to remove any cleaning solution residues.
- Drying: Dry the stainless steel using hot air dryers.
Water Quality Recommendation: Use deionized water with a resistivity of at least 18 MΩ·cm to ensure no ionic contamination.
3. Painting and Drying Line
After cleaning, a photoresist is applied to the stainless steel surface to protect areas that should not be engraved.
Steps:
- Application: Apply a uniform coat of liquid photoresist or dry film photoresist using a roller or spray system.
- Pre-drying: Partially dry the photoresist to remove solvents without curing it completely, typically in a convection oven.
- Final Drying: Cure the photoresist in a controlled environment, typically in a conveyorized oven with precise temperature control.
Temperature Control:
- Pre-drying: 100-120°C for 1-2 minutes.
- Final Drying: 150-180°C for 5-10 minutes, depending on the specific resist material.
4. Exposure Line
The photoresist-coated stainless steel is exposed to UV light to create the desired pattern.
Steps:
- LED Exposure:
- Process: The stainless steel is placed in an exposure unit, and a photomask is aligned over it. UV LEDs expose the photoresist through the photomask.
- Workflow: Align photomask → Expose with UV LED → Move to developing line.
- Advantages: Cost-effective, suitable for less complex patterns.
- LDI Exposure:
- Process: Directly writes the pattern onto the photoresist using a laser, eliminating the need for a photomask.
- Workflow: Program design into LDI system → Expose photoresist with laser → Move to developing line.
- Advantages: High precision, ideal for complex and high-resolution patterns.
5. Developing Line
After exposure, the photoresist needs to be developed to reveal the pattern that will be engraved.
Steps:
- Developer Solution: Immerse the exposed stainless steel in a developer solution, typically a diluted alkaline solution.
- Rinse: Rinse with DI water to stop the development process and remove all developer residues.
- Drying: Dry the stainless steel using hot air dryers.
Why Developing is Necessary: Developing removes the exposed (or unexposed, depending on the type of resist) areas of the photoresist, creating the precise pattern needed for engraving.
6. Stainless Steel Engraving Line
The developed stainless steel is now ready for engraving, which removes the unprotected areas of the metal.
Engraving Solution Example:
Steps:
- Etchant Preparation: Prepare an appropriate etchant solution. Common solutions include ferric chloride (FeCl₃):
- Ferric chloride (FeCl₃): 400-500 g/L
- Temperature: 45-55°C
- Engraving Process: Immerse the stainless steel in the etchant solution. The unprotected areas will be dissolved, creating the desired pattern.
- Agitation: Use mild agitation to ensure even engraving.
- Duration: Engraving time depends on the desired depth and pattern complexity, typically 10-30 minutes.
- Rinse: Rinse thoroughly with DI water to remove etchant residues.
Parameters:
- Temperature: Maintain at 50-55°C for optimal engraving speed and precision.
- Proportion: Ensure the etchant solution is regularly monitored and replenished to maintain effectiveness.
7. Stripping Line
After engraving, the remaining photoresist must be stripped away to reveal the final metal pattern.
Steps:
- Stripping Solution: Use a photoresist stripper solution, often an alkaline or solvent-based solution.
- Immersion: Immerse the engraved stainless steel in the stripping solution until all photoresist is removed.
- Rinse: Rinse with DI water to remove any stripper residues.
- Final Drying: Dry the stainless steel using hot air dryers.
Details:
- Stripper Solution Temperature: Typically 40-60°C.
- Immersion Time: 5-10 minutes, depending on the resist thickness and type.
Chemical Engraving Stainless Steel: Detailed Steps
If you need a OEM factory to realize your project, please do not hesitate to contact us.
Wet Chemical Etching Company is a leading provider of wet chemical etching services, dedicated to delivering high-quality and precise etching solutions for the semiconductor, microelectronics, and precision manufacturing industries. Equipped with advanced technology and state-of-the-art equipment, our company can handle various materials and complex pattern requirements. Our professional team has extensive experience and expertise, ensuring that every project is delivered on time and meets the highest quality standards. Whether for prototype development or large-scale production, Wet Chemical Etching Company is committed to customer satisfaction, offering customized and efficient services to help your products succeed in the market.