Technology Comparison
When comparing chemical etching and laser cutting for aluminum, it’s important to evaluate the specific strengths and limitations of each method. Let’s take a closer look at key differences between these technologies:
Thermal Impact: Laser Cutting vs. Cold Chemical Etching
Laser cutting generates heat as it melts or vaporizes the material, which can lead to issues like heat-affected zones (HAZ), oxidation, or material distortion.
In contrast, chemical etching is a cold process that doesn’t induce thermal stress, providing a clean, precise cut with no impact on the surrounding material.
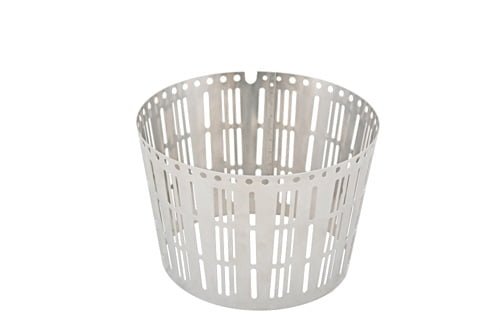
Aspect | Laser Cutting | Chemical Etching |
---|---|---|
Thermal Impact | High, leading to HAZ and potential distortion | No thermal impact, stress-free surface |
Edge Quality | May require post-processing (deburring) | Smooth, burr-free edges |
Material Deformation | Possible warping due to heat | No deformation |
Tolerance Precision
Laser cutting typically provides ±0.1mm tolerance, which is suitable for many applications. However, chemical etching achieves a finer level of precision, with tolerances as tight as ±0.05mm, making it ideal for intricate and detailed designs.
Material and Thickness Suitability
The suitability of each process depends on the thickness of the aluminum being used:
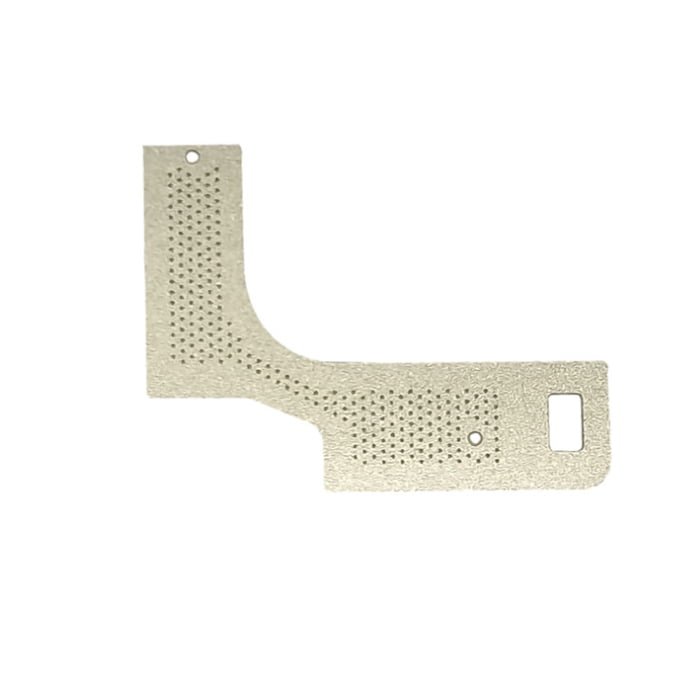
Thickness Range | Best Method | Comments |
---|---|---|
0.1–2.0mm | Chemical Etching | Ideal for thin sheets, fine details, no warping |
>3mm | Laser Cutting | Preferred for thicker materials, efficient cuts |
Etching for Thin Sheets (0.1–2.0mm)
Chemical etching is best suited for thin aluminum sheets ranging from 0.1mm to 2.0mm. It allows for precision patterning without causing distortion or heat damage, making it ideal for high-precision applications.
Laser Cutting for Thicker Aluminum (>3mm)
For thicker aluminum (greater than 3mm), laser cutting is typically preferred as it can easily handle the increased material thickness. Laser cutting offers the strength required to cut through thicker sheets with clean edges.
Surface Finish and Burr-Free Edges
Post-Processing Requirements for Laser-Cut Parts
Laser cutting often results in burrs and sharp edges, requiring post-processing (such as deburring or grinding) to smooth the parts.
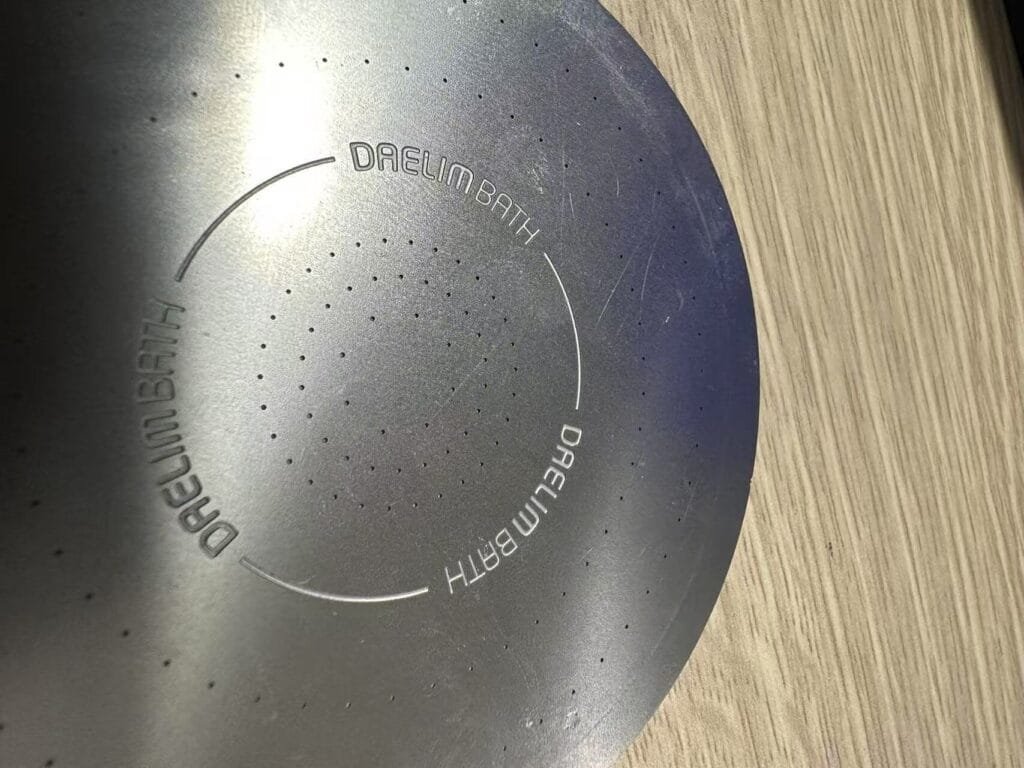
Etching’s Smooth, Stress-Free Results
Chemical etching produces parts with smooth, burr-free edges and a consistent surface finish, eliminating the need for additional finishing steps. This process also retains the material’s natural properties, preventing stress or deformation.
Cost Analysis
Here’s a breakdown of the cost differences between chemical etching and laser cutting:
Cost Aspect | Laser Cutting | Chemical Etching |
---|---|---|
Tooling Costs | High (laser programming, setup) | Lower (masks for pattern definition) |
Per-Part Pricing (Small Batches) | Higher (due to setup costs) | Lower (cost-effective for small runs) |
Per-Part Pricing (Large Batches) | Lower (economical for high-volume cuts) | Higher for large runs (setup for masks) |
Tooling Costs (Masks vs. Laser Programming)
- Chemical etching requires masks for pattern creation, which involves an initial cost but can be reused for multiple parts, making it cost-effective for small to medium batches.
- Laser cutting involves laser programming that requires more time and cost upfront, particularly for intricate designs, but it can be more economical for large-scale production.
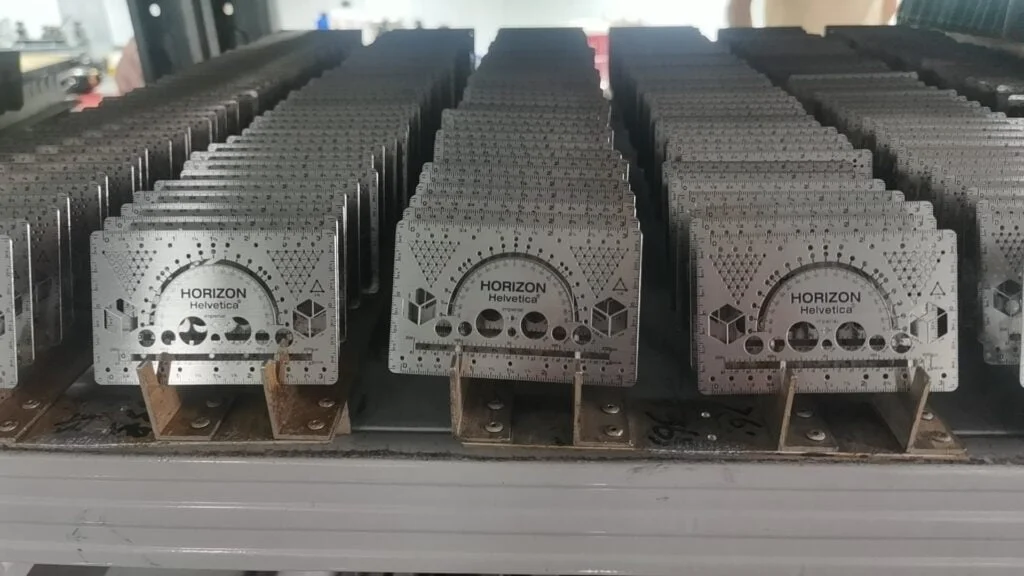
Per-Part Pricing for Small vs. Large Batches
- Chemical etching offers a significant cost advantage for small to medium-sized batches, where the tooling cost is spread over fewer parts.
- Laser cutting may become more cost-effective for large-scale production due to the high setup cost being distributed over a larger quantity of parts.
Industry Recommendations
Aerospace: Etching for Microfluidic Channels
Chemical etching is often preferred in aerospace for microfluidic channels used in various systems, where high precision and thin aluminum sheets are crucial. Etching ensures clean, burr-free channels without thermal distortion, ideal for applications that require exacting specifications.
For instance, NASA and Boeing have utilized chemical etching to create intricate fluidic pathways in aerospace components. This application demands high precision, making etching an optimal choice. You can read more about their projects in aerospace etching on NASA’s website.
Signage: Laser for Thick, Structural Letters
For industries like signage, laser cutting is favored for thicker aluminum when creating large, structural letters. The ability to cut through thicker materials quickly and efficiently makes laser cutting ideal for applications requiring large-volume production.
Companies like Vanguard Sign rely on laser cutting to produce durable 3D aluminum letters for signage. Their use of laser cutting ensures high-quality results for projects with complex designs and thick materials. Read more about their signage solutions at Vanguard Sign’s site.