When it comes to manufacturing stainless steel components, two of the most commonly used processes are chemical etching and laser cutting. Each has its own set of advantages and ideal applications. In this article, we will compare the key differences in these two technologies, helping you decide which is better suited for your needs based on factors like precision, cost, and material integrity.
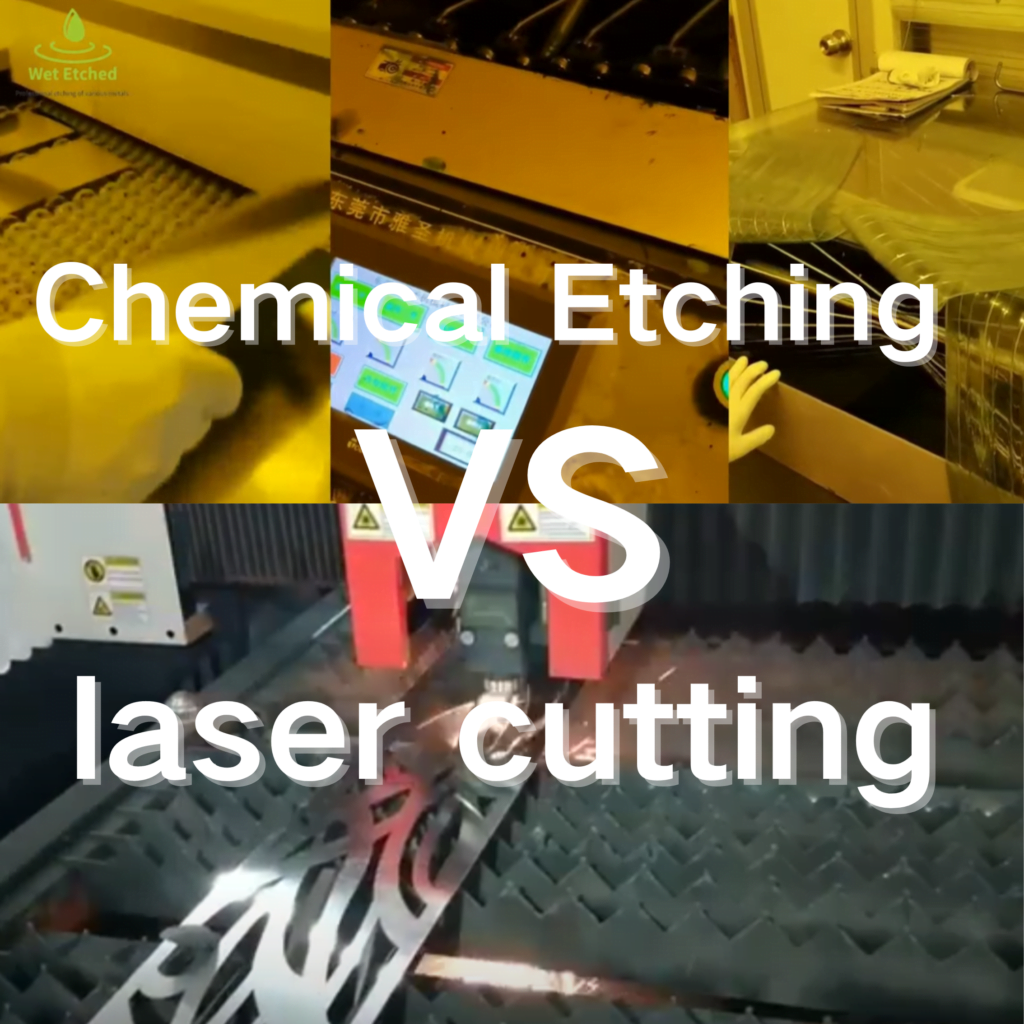
Non-Thermal Process (Etching) vs. Thermal (Laser)
The most fundamental difference between chemical etching and laser cutting is the type of energy they use. Etching is a non-thermal, chemical process, while laser cutting is a thermal process that relies on focused light to cut through materials.
Aspect | Chemical Etching | Laser Cutting |
---|---|---|
Energy Source | Non-thermal (chemical reaction) | Thermal (high-intensity laser beam) |
Material Interaction | No heat generated, no thermal stress | High heat input, causing thermal effects |
Tool Wear | No tool wear | Wear of the laser nozzle may occur |
Best for | Fine, intricate designs | Thick materials (over 3mm) |
Chemical etching works by using acidic solutions to selectively remove material, while laser cutting uses intense heat to vaporize the material. This key difference influences precision and material integrity, with etching typically being better for intricate designs and laser cutting excelling in thicker materials.
Tolerance Comparison (±0.003mm vs. ±0.015mm)
Precision is one of the most critical factors when selecting between chemical etching and laser cutting.
- Chemical etching can achieve a tolerance as fine as ±0.003mm, which makes it ideal for applications that require extremely precise, intricate designs such as micro-perforations, logos, and fine patterns.
- Laser cutting, while still precise, typically has a tolerance of ±0.015mm. This is still highly accurate but is better suited for structural parts and thicker materials.

For projects requiring the highest levels of precision in thin materials, chemical etching is the better choice. For more robust applications where tolerance is important but not as stringent, laser cutting is a viable option.
Precision and Complexity Capabilities
Both methods can create high-precision designs, but the capabilities differ in terms of complexity.
Chemical Etching:
- Ideal for micro-features and intricate details.
- Can produce small holes as tiny as <0.2mm, which is difficult for laser cutting.
- Best for flat surfaces or thin materials.
Laser Cutting:
- Can handle larger, thicker parts with precision.
- Not suitable for micro-features like small holes or complex patterns that require the removal of very fine material.
Etching for Micro-Features (<0.2mm Holes)
One of the standout advantages of chemical etching is its ability to produce micro-features, such as holes smaller than 0.2mm, which are difficult or impossible to achieve with laser cutting.
Feature | Chemical Etching | Laser Cutting |
---|---|---|
Micro-Hole Capability | <0.2mm (ideal for fine perforations) | Limited for holes under 0.5mm |
Precision | Extremely high for fine features | Less precise for small holes |
Best for | Micro-electronics, sensors, medical devices | Structural cuts in thicker materials |
For industries like medical devices, electronics, or any application that requires fine features on thin materials, chemical etching is the preferred method.
Laser Cutting for Thick Materials (>3mm)
Laser cutting excels in cutting through thicker materials, especially those over 3mm thick, which would be more challenging for chemical etching.
Material Thickness | Chemical Etching | Laser Cutting |
---|---|---|
Material <3mm | Ideal for precision parts | Can be used, but not optimal for fine details |
Material >3mm | Not suitable for deep cuts | Excellent for cutting thick metals |
For applications involving thicker stainless steel, laser cutting offers superior results.
Surface Finish and Material Integrity
When it comes to surface finish and material integrity, the two processes differ significantly:
- Chemical etching provides burr-free, stress-free results, preserving the integrity of the material. The non-thermal nature of etching ensures that the surface is not affected by heat, avoiding the risk of warping or distortion.
- Laser cutting often results in heat-affected zones (HAZ), where the edges of the cut material are exposed to high temperatures, potentially leading to material hardening, cracking, or oxidation.
Heat-Affected Zones (HAZ) in Laser Cutting
The heat-affected zones (HAZ) produced in laser cutting can lead to changes in material properties, such as micro-cracks, oxidation, and material hardening. These effects can reduce the material integrity in the cut area.
Factor | Chemical Etching | Laser Cutting |
---|---|---|
Heat-Affected Zones | None (no heat used) | Yes, can cause material changes |
Material Integrity | No distortion | Possible (due to heat) |
For industries that require material integrity to be maintained, such as aerospace, medical, and electronics, chemical etching is often the preferred choice.
Etching’s Burr-Free, Stress-Free Results
Another key advantage of chemical etching is that it produces burr-free and stress-free results. Because no mechanical cutting or heat application is involved, the edges remain clean, smooth, and consistent. This reduces the need for secondary finishing processes and ensures the parts are ready for use right after the etching process.
Cost Analysis for High-Volume Production
When considering the costs of high-volume production, it’s important to evaluate both tooling costs and per-part pricing.
Tooling Costs (Etching Masks vs. Laser Programming)
Process | Tooling Costs | Best for |
---|---|---|
Chemical Etching | Low (mask creation) | Small to medium runs, custom designs |
Laser Cutting | Medium to High (programming laser) | Large runs with standard designs |
Chemical etching offers lower tooling costs for small or custom runs since it only requires a photoresist mask. On the other hand, laser cutting requires more expensive programming and equipment for each design.
Per-Part Pricing at Scale
At scale, per-part pricing for chemical etching tends to be more economical for highly customized parts with complex designs. However, laser cutting can be more cost-effective at very high volumes of simpler parts, as its setup costs are amortized over larger quantities.
Industry-Specific Recommendations
Different industries will find one process more advantageous than the other depending on the requirements of the parts.
Medical (Etching for Biocompatibility)
In the medical industry, chemical etching is preferred for creating biocompatible parts such as surgical instruments, implantable devices, and medical sensors. The burr-free, stress-free nature of etching makes it ideal for these sensitive applications, ensuring there is no risk of material distortion.
Automotive (Laser for Structural Parts)
For automotive applications, especially when dealing with thick stainless steel for structural parts, laser cutting is often the better option. It excels at cutting thick materials with precision and can handle high-volume production of simple geometric parts such as brackets, frames, and body panels.