Photo Chemical Machining has revolutionized the way stainless steel products are prototyped and produced. With low tooling costs, significantly reduced lead times, and high material efficiency, PCM stands out as a strategic enabler for cost-effective prototyping. By selecting the right suppliers and leveraging advanced PCM techniques, product managers and entrepreneurs can accelerate product development, minimize costs, and ensure scalability from prototype to mass production.
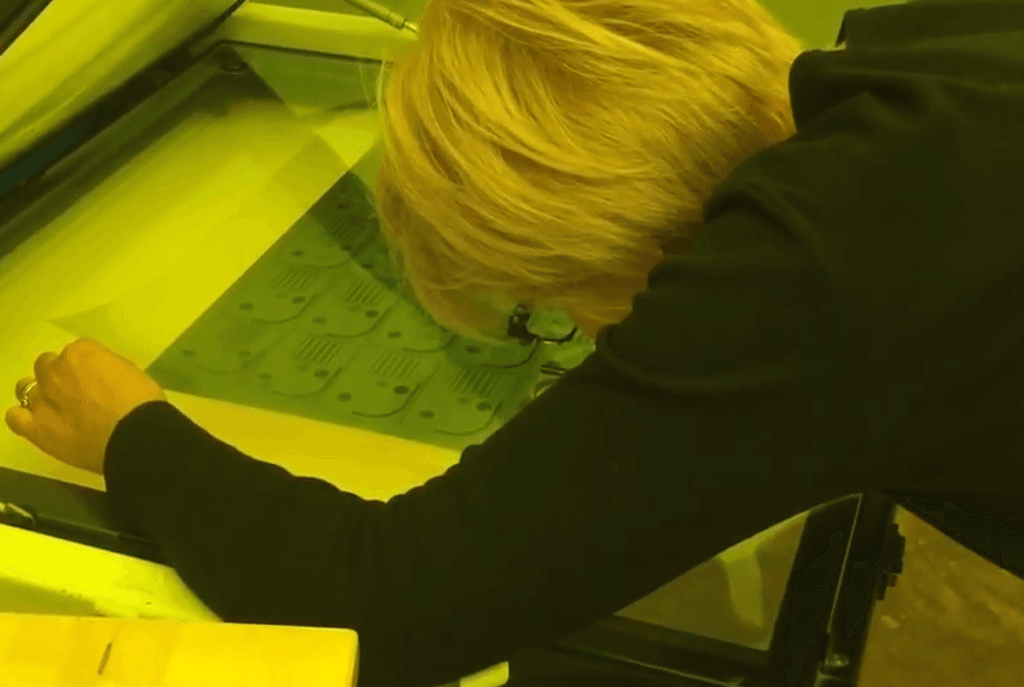
PCM is more than just a manufacturing process; it’s a transformative approach that redefines rapid prototyping and production efficiency in the stainless steel industry. Embracing this technology paves the way for innovation while maintaining a competitive edge in today’s fast-paced market.
ROI Analysis: Minimizing Tooling Costs
One of the most compelling benefits of PCM is its remarkably low tooling cost compared to traditional manufacturing methods. When using PCM for small batches, the tooling expenses can be nearly negligible compared to the $15k–$50k typically associated with hard tooling. This reduction in upfront investment not only improves the return on investment (ROI) but also opens the door for rapid experimentation and iterative design changes.
Timeline Breakdown: Accelerating Time to Market
Time is money, and PCM dramatically reduces production lead times. For example, aerospace sensor plates manufactured with PCM can achieve a 72-hour lead time, compared to the 6 weeks required with conventional machining methods. This swift turnaround is particularly vital for industries requiring rapid prototyping and agile development cycles. By shortening the production cycle, product managers can iterate faster and bring products to market much more quickly.
Material Efficiency Metrics: Maximizing Stainless Steel Utilization
Material waste can significantly impact overall production costs. PCM is known for its exceptional material efficiency, boasting a 95% stainless steel utilization rate. In stark contrast, conventional CNC milling techniques often yield only a 60% utilization rate. This high level of efficiency not only contributes to cost savings but also aligns with sustainable manufacturing practices—a key consideration for today’s environmentally conscious market.
Real-World Example: Marine Hardware Scaling
A compelling example of PCM’s scalability is seen in the production of corrosion-resistant marine hardware. A marine component manufacturer successfully scaled production from 10 units to 10,000 units using PCM. This transition was achieved without the high capital expenditure typically required for scaling with traditional manufacturing processes. The case illustrates how PCM can effectively support both small-scale prototypes and large-scale production runs, providing a versatile solution for complex manufacturing needs.
Supplier Selection Checklist: Ensuring Quality and Compliance
When considering PCM for product development, it is crucial to work with suppliers that meet industry standards. A robust supplier selection checklist should include:
- Certifications: Look for suppliers with AS9100 for aerospace or ISO 13485 for medical applications.
- Quality Assurance: Ensure that the supplier maintains rigorous quality control protocols to support the high precision required by PCM.
- Experience: Prioritize suppliers with a track record in delivering PCM services for both small prototypes and large production runs.
- Support and Collaboration: Evaluate the supplier’s willingness to engage in a collaborative process, providing insights and guidance on process optimization.
For additional guidance on supplier selection and best practices, resources from Thomas Insights provide in-depth articles and expert opinions on manufacturing partnerships.
Comparative Analysis: PCM vs. Traditional CNC Milling
To better understand the advantages of PCM over conventional methods, consider the table below which details a side-by-side comparison:
Aspect | Photo Chemical Machining (PCM) | CNC Milling |
---|---|---|
Tooling Cost | Minimal to near zero tooling costs | $15k–$50k for hard tooling in small batches |
Lead Time | 72-hour lead time for aerospace sensor plates | 6 weeks for similar components |
Material Efficiency | Up to 95% utilization of stainless steel | Approximately 60% utilization |
Scaling Capability | Easily scalable from prototypes to large production runs | Scaling can be cost-prohibitive due to tooling expenses |
This table clearly illustrates how PCM offers substantial benefits over CNC milling, particularly in cost savings and efficiency—factors that are critical for rapid prototyping and agile product development.