Why Choose Chemical Etching for Aluminum Prototypes?
For product designers and startups looking to create custom aluminum parts, chemical etching offers an affordable and efficient solution for prototyping. This process enables the production of highly detailed and precise designs while keeping costs low and turnaround times fast. Here’s why chemical etching is an ideal choice for aluminum prototypes.
Low Tooling Costs and Rapid Turnaround
One of the primary advantages of chemical etching over traditional manufacturing methods is its low tooling costs. Unlike methods such as CNC machining or die casting, which require expensive molds and tooling, chemical etching only needs a photoresist mask, making it an affordable option for small to medium runs.
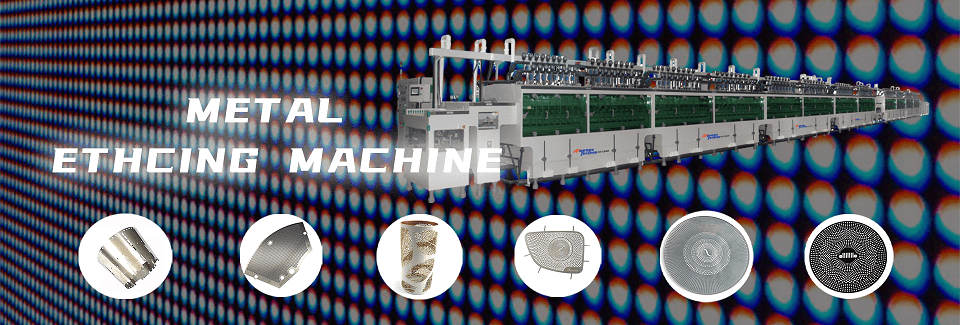
Additionally, chemical etching allows for rapid turnaround on prototypes. Since there’s no need for extensive tooling or machine setup, designers can quickly iterate on their designs, testing multiple versions in a short amount of time. This rapid prototyping capability is crucial for startups or projects that require quick market entry.
Complex Geometries (Micro-Perforations, Intricate Logos)
Chemical etching excels in creating complex geometries with high precision. It’s particularly effective for micro-perforations, intricate logos, and detailed patterns that would be difficult or costly to achieve with other manufacturing methods like laser cutting or CNC milling.
Feature | Chemical Etching | Laser Cutting | CNC Milling |
---|---|---|---|
Precision | High (up to 0.025mm) | Medium (depends on material and design) | Medium (requires tooling) |
Best for | Micro-perforations, fine details, logos | Simple cuts on thicker material | Complex shapes and thick materials |
Material Flexibility | Great for thin aluminum | Works for thicker materials | Works for thicker materials |
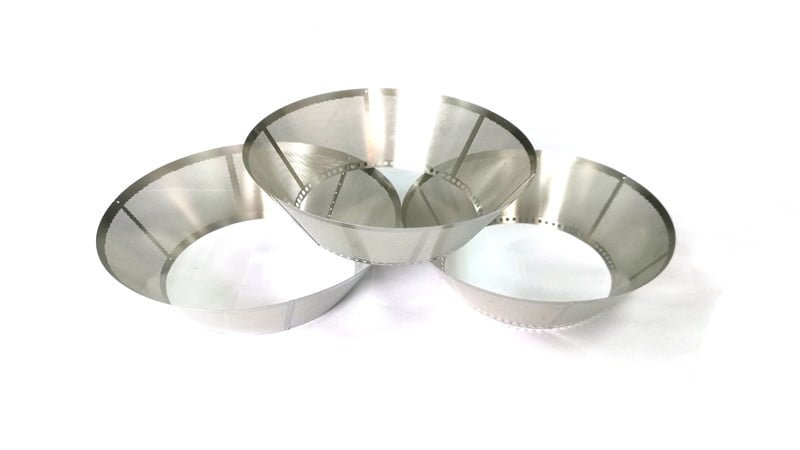
Chemical etching allows for precise, intricate designs on thin aluminum parts, making it an ideal choice for creating custom logos and unique patterns in industries like electronics and automotive.
Material Efficiency and Cost Savings
For startups and product designers looking to minimize costs and maximize material use, chemical etching offers several advantages in material efficiency.
Nesting Strategies for Sheet Optimization
To optimize material use, nesting strategies can be employed during the etching process. Nesting refers to the arrangement of parts on the aluminum sheet in such a way that waste is minimized. By strategically placing parts, designers can ensure that every inch of the material is used efficiently.
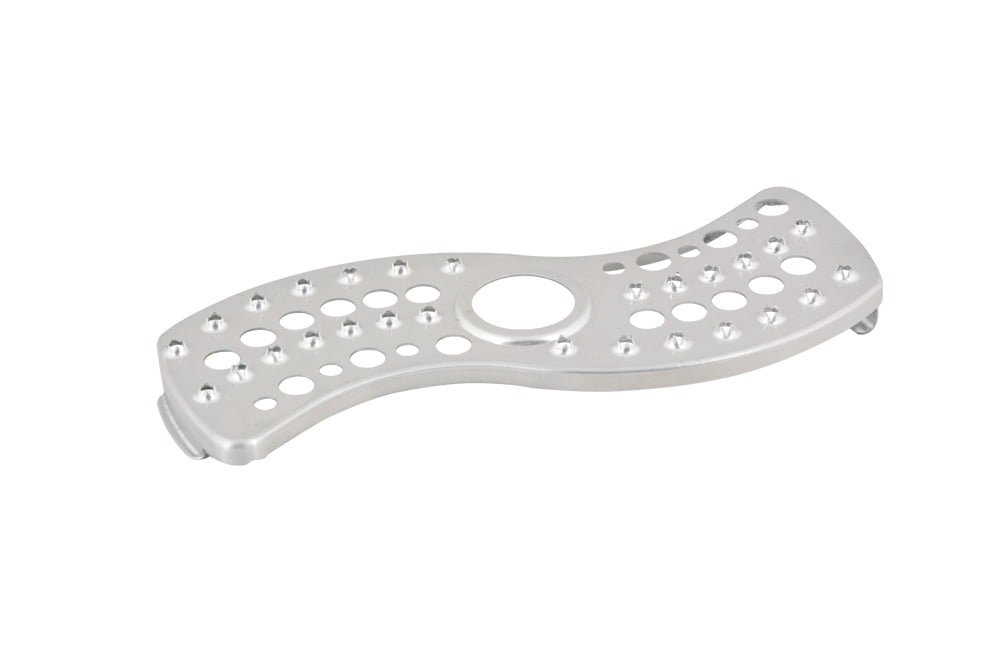
Strategy | Description | Benefits |
---|---|---|
Optimal Layout | Arrange parts close together to reduce waste | Maximizes material usage, reduces cost |
Repetitive Patterns | Use identical or similar parts to reduce cutting time | Reduces material scrap |
Part Orientation | Place parts in orientations that minimize voids | Reduces edge waste |
These strategies are particularly beneficial for low-volume production, as they reduce the cost per part by making full use of the material.
Recyclability of Aluminum Scrap
Aluminum is highly recyclable, making it an excellent material for sustainable manufacturing. Any aluminum scrap generated during the etching process can be easily recycled, reducing the overall environmental impact and contributing to a circular economy. This is particularly important for companies that prioritize eco-friendly practices in their supply chain.
By recycling aluminum scrap, manufacturers can reduce their demand for new aluminum, lowering both material costs and their carbon footprint.
Case Studies
Let’s explore a few examples of how chemical etching is being used in real-world applications, providing valuable insights into the versatility of this process.
Consumer Electronics (Etched Aluminum Phone Casings)
In the consumer electronics industry, etching aluminum is frequently used for phone casings and other electronic enclosures. Chemical etching allows for the creation of detailed patterns and logos that enhance the aesthetic appeal of the product while keeping it lightweight and durable.
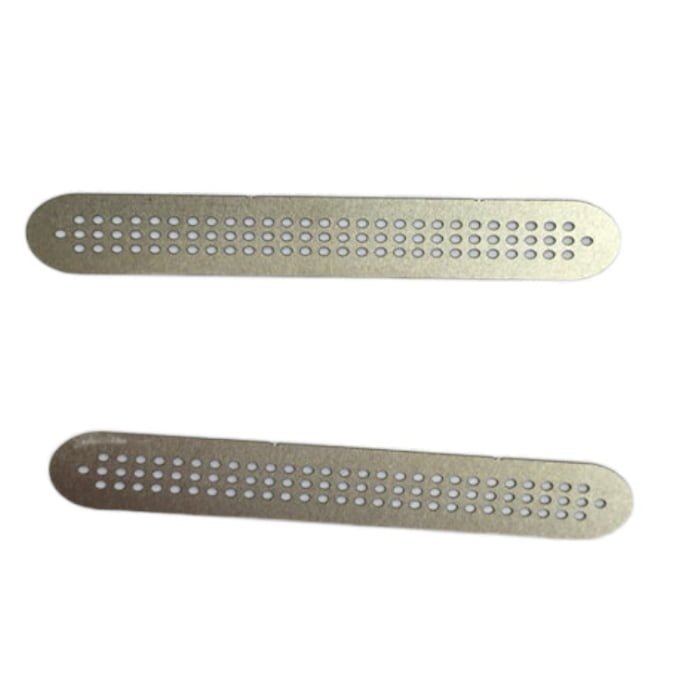
For instance, smartphone manufacturers use chemical etching to create textured or logo-engraved aluminum casings that are both functional and visually striking. The process ensures that intricate designs can be produced without the need for expensive tooling or long setup times.
Automotive (Decorative Trim, Lightweight Brackets)
Automotive manufacturers also benefit from chemical etching for creating decorative trim and lightweight brackets. Chemical etching allows for the precise formation of complex patterns on aluminum parts that are used for both functional and aesthetic purposes.
For example, etched aluminum can be used for exterior trim on vehicles, as it provides a high-quality finish and allows for custom patterns or logos. The lightweight nature of aluminum also helps improve fuel efficiency, making it a popular choice for automotive manufacturers focused on reducing weight.
Partnering with Etching Suppliers
Choosing the right etching supplier is crucial for ensuring that your custom aluminum parts meet the required specifications and are produced efficiently. Here’s how to evaluate potential suppliers and ensure they’re the right fit for your needs.
Evaluating Expertise in Thin-Film Etching
Thin-film etching is a specialized area of chemical etching, particularly important for electronics and aerospace industries. When evaluating suppliers, ensure that they have experience with thin-film etching and can achieve the precision needed for aluminum prototypes.
Look for suppliers who have demonstrated expertise in creating intricate designs with tight tolerances, as this will ensure that the final product meets both functional and aesthetic requirements.
MOQs and Lead Time Negotiation Tips
When working with an etching supplier, it’s important to understand their Minimum Order Quantities (MOQs) and negotiate lead times based on your needs. Since chemical etching is ideal for low to medium-volume production, many suppliers offer flexibility in order size.
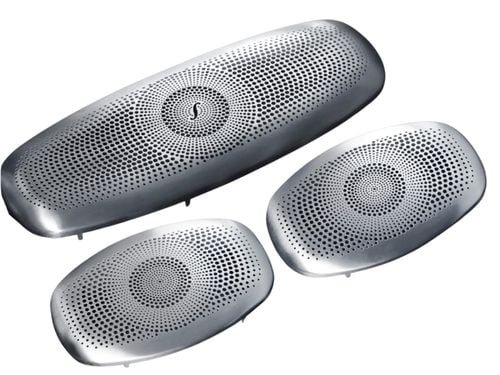
Lead Time Negotiation Tips:
- Set realistic expectations: Know your lead time needs in advance and communicate them clearly to the supplier.
- Consider batch production: For multiple prototypes or design variations, negotiate batch production to save on setup time and costs.
- Work closely with your supplier: Build a strong relationship to ensure quick adjustments to your project timeline if needed.
Scaling from Prototype to Production
As your design evolves from a prototype to high-volume production, chemical etching can scale to meet your needs. Here’s how to transition to large-scale etching systems without compromising quality.
Transitioning to High-Volume Etching Systems
When scaling production, consider upgrading to automated etching systems that can handle larger quantities. These systems can improve efficiency, reduce lead times, and lower costs by automating the masking, etching, and rinsing processes.
Some manufacturers also offer custom solutions for high-volume runs, allowing you to maintain the design flexibility of prototypes while ensuring consistency and precision in large batches.