Thin film heaters represent a modern, efficient, and customizable solution to heating challenges. By leveraging advanced materials like PI and PET, combined with flexible designs and precise heat distribution, these heaters are revolutionizing the way industries approach heating solutions. Whether you’re designing cutting-edge automotive systems or consumer electronics, thin film heaters offer unparalleled performance and flexibility.
What Makes Thin Film Heaters Unique?
Thin film heaters are a cutting-edge solution in the world of heating technology. Unlike traditional heating methods that use bulky, rigid materials, thin film heaters offer a flexible and compact design, making them ideal for space-constrained applications. These heaters are constructed from thin, flexible materials like Polyimide (PI) or Polyethylene Terephthalate (PET), which can be combined with conductive metals such as aluminum, copper, or stainless steel.
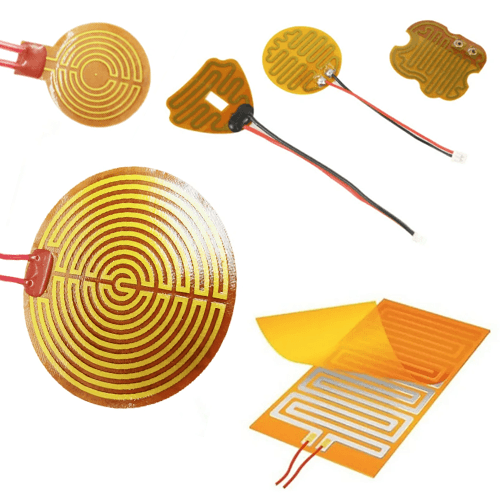
The key feature of thin film heaters is their ability to distribute heat evenly across a surface, providing high thermal efficiency. Their flexibility allows them to be molded or shaped into various configurations, enabling heating in areas where traditional heaters cannot be used. Additionally, thin film heaters are energy-efficient, with quick heat-up times and low power consumption, making them a popular choice in a wide range of industries.
Material Combinations: PI vs. PET with Metals
Two of the most commonly used substrates for thin film heaters are Polyimide (PI) and Polyethylene Terephthalate (PET). These materials, when combined with metals such as aluminum, copper, or stainless steel, offer different benefits depending on the specific heating needs.
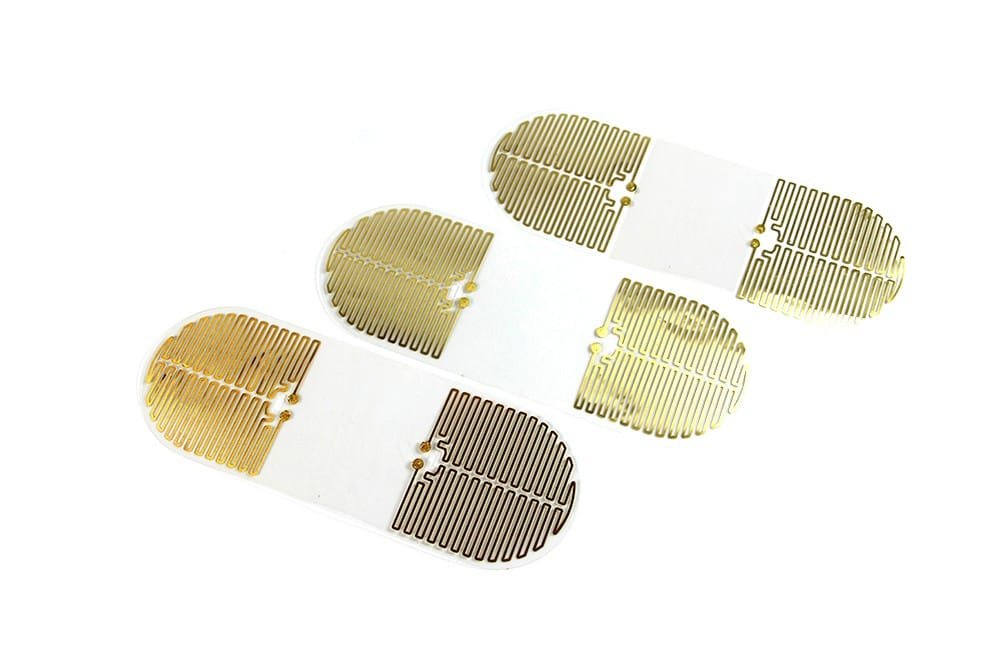
- PI-based heaters are known for their ability to withstand higher temperatures (up to 260°C), making them ideal for applications that require durability in extreme environments, such as in automotive or aerospace industries. The high thermal stability of PI allows it to maintain its performance at elevated temperatures without degradation.
- PET-based heaters, on the other hand, are more affordable and flexible, with a lower maximum operating temperature (~90°C). These heaters are often used in consumer electronics like beauty devices and heated clothing, where flexibility and lightweight design are key.
The combination of these substrates with various metals allows manufacturers to customize the heater’s performance, tailoring the material choice to the intended application and operating conditions.
Core Applications Across Industries
Thin film heaters are used in a variety of industries, each taking advantage of the technology’s flexibility, efficiency, and precise temperature control. Here are some common applications:
- Automotive: One of the most popular applications of thin film heaters in the automotive industry is in wiper blade heaters. These heaters ensure that the windshield wipers remain clear of ice or fog, even in harsh weather conditions. The PI heating film used in this application is durable and energy-efficient, offering a compact solution for a critical vehicle function.
- Medical: In the medical field, thin film heaters are widely used in IV tube warmers and CPAP machines. These heaters help maintain a consistent and comfortable temperature for medical fluids or respiratory gases, ensuring patient comfort and safety.
- Consumer Electronics: From heated beauty devices to handwarmers, thin film heaters provide a space-saving solution for heating elements in small electronics. The flexibility of these heaters makes them ideal for use in curved or compact devices.
These are just a few examples—thin film heaters can be found in countless other applications, from food warming to energy storage systems in electric vehicles.
Key Benefits: Efficiency, Safety, and Customization
Thin film heaters offer a wide array of benefits that make them stand out from traditional heating elements:
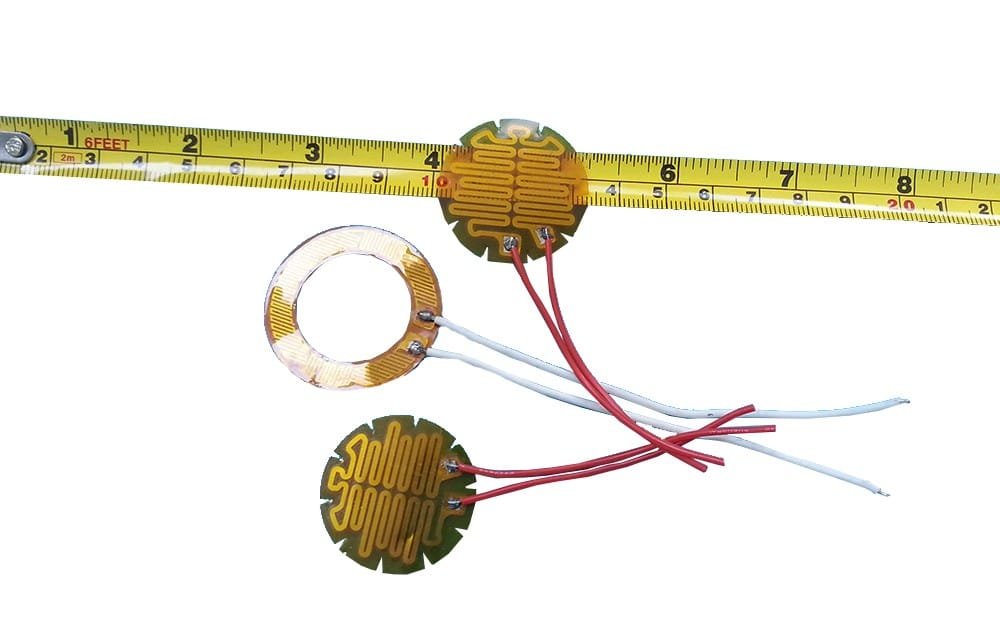
- Efficiency: Thin film heaters heat up quickly and efficiently. Their design ensures even heat distribution, reducing energy loss and ensuring consistent temperatures across the heated area. This results in lower overall energy consumption and faster heating times, making them cost-effective in both the short and long term.
- Safety: The use of high-quality materials, combined with modern safety features like built-in temperature sensors and fuses, makes thin film heaters safer than traditional options. Their thin, lightweight design also reduces the risk of overheating or causing damage in surrounding materials.
- Customization: One of the standout features of thin film heaters is their flexibility. They can be tailored to meet a variety of needs, from shape and size to voltage and wattage. Whether it’s a custom round heater for a camera lens or a long, narrow strip heater for a battery pack, the possibilities are virtually endless.
Why Choose Thin Film Heaters Over Alternatives?
When comparing thin film heaters to other heating technologies, such as resistive wire heaters or ceramic heaters, there are several key advantages:
- Space Efficiency: Thin film heaters are lightweight and flexible, allowing them to be installed in tight or irregular spaces where traditional heaters would be too bulky or rigid.
- Durability: Unlike resistive wire heaters, which can degrade over time, thin film heaters are made from durable materials that are resistant to wear and tear, providing longer service life with minimal maintenance.
- Precision Heat Distribution: Thin film heaters provide a more uniform heat distribution compared to ceramic or wire heaters. This allows for more controlled heating, which is essential in applications like medical devices and electronic products, where precise temperature regulation is critical.
Thin film heating elements provide superior versatility, efficiency, and customization, making them an ideal choice across various industries, including automotive, medical, consumer electronics, and more.