Chemical etching excels in providing designers with unmatched flexibility for creating complex geometries and customized designs. Whether working with stainless steel, aluminum, or other materials, etching allows for precise control over fine details and pattern creation. This makes it an excellent option for creating micro-perforations, logos, and intricate patterns with high precision.
Complex Geometries (Micro-Perforations, Fine Logos)
Chemical etching is ideal for creating complex geometries, such as micro-perforations or fine logos, which can be challenging for other manufacturing processes. The high precision of the etching process allows for the creation of small holes, detailed patterns, and logos on a variety of materials, including stainless steel, without compromising quality.
For example: Stainless Steel Shower Head Filter Mesh Etching
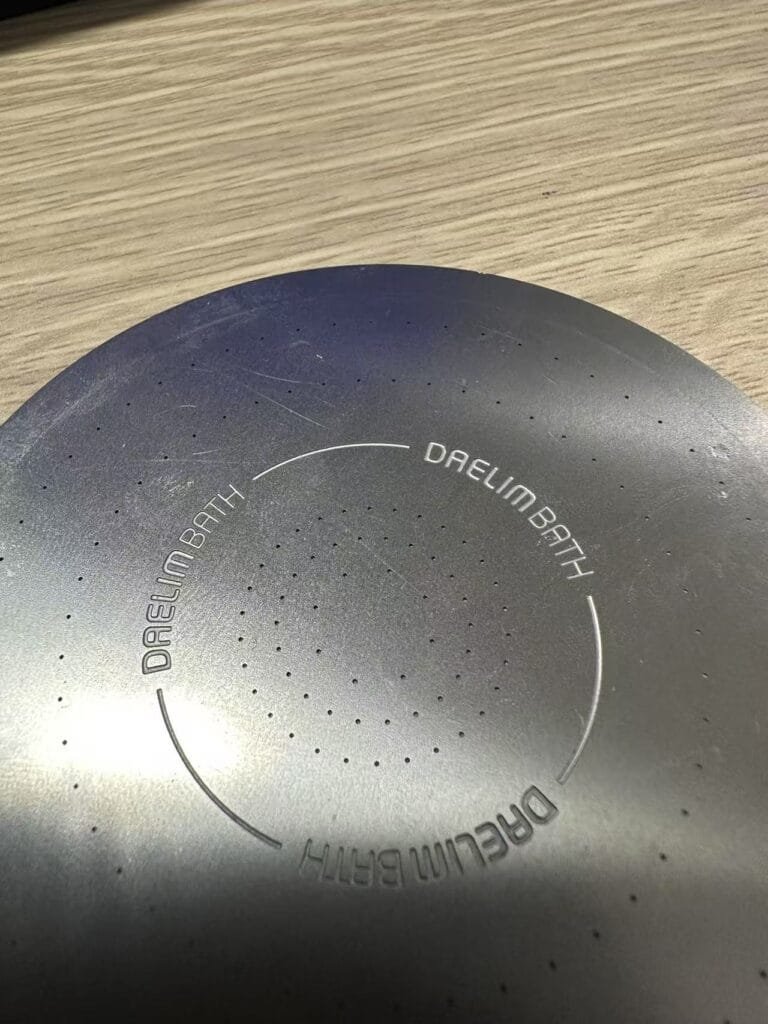
Etching Depth Control (Shallow vs. Deep Etching)
Another advantage of chemical etching is the ability to control the etching depth, offering versatility for different types of designs. Designers can opt for shallow etching for surface designs or deep etching for more complex, functional components. The process allows precise depth control, ensuring that etching requirements are met based on the project’s needs.
Etching Depth | Applications | Benefits |
---|---|---|
Shallow Etching | Decorative patterns, logos, text | High precision, ideal for surface designs |
Deep Etching | Functional components, thicker materials | Stronger structural components, high-depth accuracy |
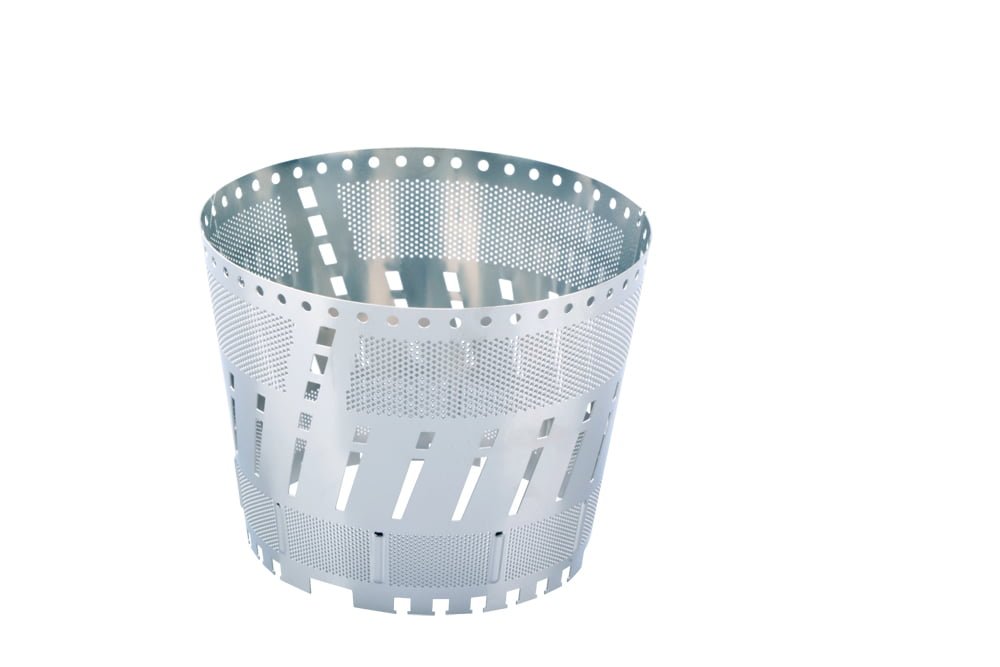
Material Efficiency and Waste Reduction
As raw material costs rise, material efficiency becomes a top priority. Chemical etching offers a subtractive process, meaning that it only removes the material that needs to be etched, minimizing waste. Unlike laser cutting, which can produce large amounts of scrap material, etching generates less waste, contributing to cost savings and environmental benefits.
Nesting Strategies for Sheet Optimization
One way to further optimize material usage in chemical etching is through nesting strategies. Nesting refers to arranging parts efficiently on the material to reduce unused space. By nesting designs carefully, designers can maximize the material’s potential, ensuring that less metal is wasted during the etching process.
Recyclability of Stainless Steel Scrap
An added benefit of chemical etching is the recyclability of stainless steel scrap. Since etching only removes the desired material, the remaining metal is left intact and can be recycled. This makes chemical etching a more sustainable choice compared to processes that produce non-recyclable waste. Designers and manufacturers benefit from the reduced environmental impact and cost savings associated with recycling stainless steel scrap.
Case Studies: Real-World ROI Examples
In order to understand the real-world return on investment (ROI) for chemical etching, it’s important to look at some case studies. These examples highlight how chemical etching can offer substantial cost savings, time efficiency, and high-quality results across various industries.
Consumer Electronics (Branded Speaker Grilles)
In the consumer electronics industry, chemical etching is used to create branded speaker grilles that feature fine, intricate patterns. The precision of chemical etching allows for detailed logos and designs that are difficult to achieve using other methods like laser cutting or stamping. This not only improves the aesthetic appeal of the product but also reduces the cost associated with creating custom speaker grilles at low volumes.
Luxury Packaging (Etched Decorative Inserts)
Luxury packaging often requires decorative inserts with intricate patterns, and chemical etching offers the perfect solution. The ability to create detailed designs on stainless steel or other metals provides a premium look without the high tooling costs associated with traditional methods like die-cutting or laser engraving. This is particularly valuable in industries such as luxury cosmetics, perfume packaging, and high-end gift items, where visual appeal is key.
Partnering with Etching Suppliers
Choosing the right supplier is crucial for achieving successful results. When working with an etching supplier, it’s essential to evaluate their expertise, capacity, and ability to meet your specific needs.
How to Evaluate Supplier Expertise
When evaluating potential etching suppliers, it’s essential to consider their experience and technical capabilities. Look for suppliers who specialize in precision chemical etching and have a proven track record in your industry. Inquire about the machines they use, their quality control processes, and whether they offer post-etching services such as passivation or cleaning.
MOQs and Lead Time Negotiation
It’s also important to discuss minimum order quantities (MOQs) and lead times with potential suppliers. Some suppliers may have high MOQs that may not be suitable for prototyping or low-volume production. By discussing lead time negotiation, you can ensure that your project progresses on schedule without unnecessary delays.