Silver, a versatile and highly conductive metal with remarkable antimicrobial properties, finds extensive use in various industries, from electronics to jewelry.
Our Packages
- From 1000pcs
- Samples from 100pcs
- Approx. 30 days (may vary depending on the difficulty of the drawing)
View our Silver etching production facility
Types of Silver and Alloys: Advantages and Disadvantages in Wet Processing
Silver comes in different forms, and alloying it with other metals can enhance specific properties. Let’s explore the advantages and disadvantages of each alloy for wet processing:
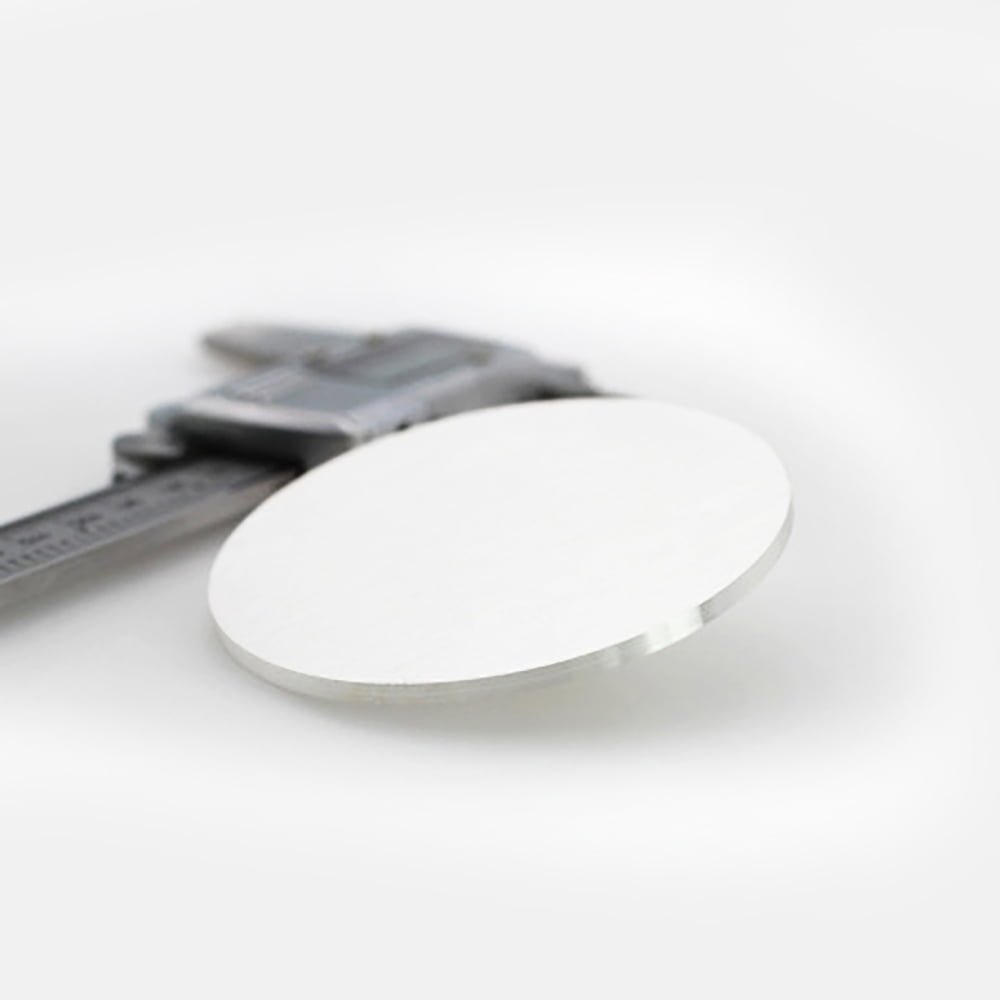
- Pure Silver: Pure silver, known for its high electrical and thermal conductivity, is widely used in electronics and jewelry. However, its softness can pose challenges during certain wet processing methods, leading to deformation or scratching.
- Silver Copper (Ag-Cu): The addition of copper enhances the hardness and strength of silver, making it more suitable for industrial applications. However, the increased copper content may require specialized etching solutions during wet processing.
- Silver-Zinc (Ag-Zn): Silver-zinc alloys offer improved corrosion resistance and are commonly used in electrical contacts. However, care must be taken to avoid excessive zinc content, which can lead to brittleness.
Metal Etching of Silver
Metal etching in the wet processing process involves using metal etching machines. The choice of etchant, such as Hydrofluoric Acid (HF), Ferric Chloride Etchant, or Cupric Chloride Etchant, impacts processing difficulty. Let’s explore key aspects of metal etching for silver:
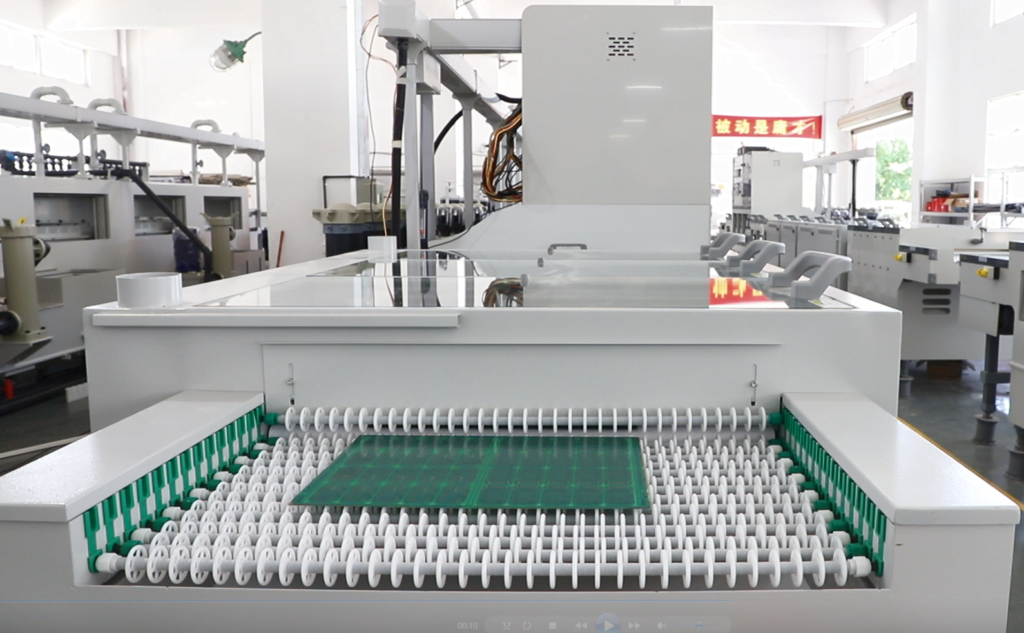
- Etching Difficulty: Silver’s reactivity with certain etchants poses challenges during the etching process. Hydrofluoric Acid (HF) is highly corrosive and requires careful handling to achieve precise etching. Ferric Chloride Etchant offers deep and well-defined patterns, while Cupric Chloride Etchant provides controlled etching and is commonly used in electronic applications.
- Precautions: Due to the corrosive nature of etchants, strict safety precautions are essential. Proper ventilation, personal protective equipment, and adherence to handling protocols prevent exposure to hazardous fumes and chemical burns.
Some of the common etchants for silver include:
- Ferric Nitrate (Fe(NO3)3) Etchant: Ferric nitrate solution can be used to etch silver by dissolving the metal and creating well-defined patterns.
- Potassium Dichromate (K2Cr2O7) Etchant: Potassium dichromate in a suitable solution can effectively etch silver, particularly in applications where high selectivity is required.
- Nitric Acid (HNO3) Etchant: Dilute nitric acid is sometimes used for etching silver. However, it should be used with caution as it can be aggressive and may also dissolve the substrate material.
- Ammonium Persulfate ((NH4)2S2O8) Etchant: Ammonium persulfate solution is also effective for etching silver and can provide controlled etching rates.
- Thiourea ((NH2)2CS) Etchant: Thiourea-based etchants can be used to etch silver, especially in applications where higher selectivity and slower etching rates are desired.
- Potassium Iodide (KI) Etchant: Potassium iodide solutions are sometimes used for etching silver, particularly when etching photographic films.
The choice of etchant depends on the specific application, desired etching rate, selectivity, and safety considerations. It’s essential to follow proper safety precautions and dispose of the etchants responsibly, especially those containing hazardous chemicals like nitric acid or potassium dichromate. As with any etching process, test etching on sample pieces is recommended to optimize the process for your particular requirements.
Silver etching equipment
Photo Etching Silver
Photo etching, also known as chemical milling, offers precise and intricate patterns on silver surfaces. The process involves using light-sensitive masks to protect specific areas while etching the exposed regions. Let’s explore key aspects of photo etching for silver:
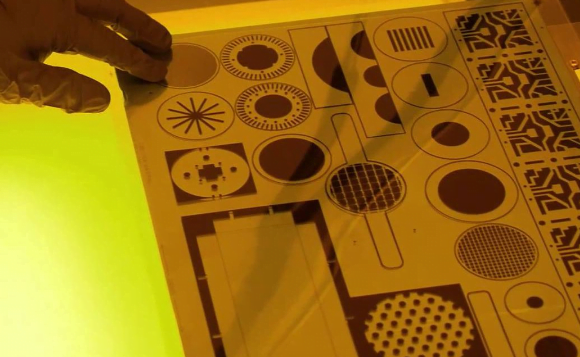
- Processing Difficulty: Photo etching demands exceptional accuracy and control. Applying and developing the photoresist carefully ensures accurate pattern transfer onto the silver surface. Advanced photolithography techniques and skilled expertise are crucial for achieving desired precision.
- Precautions: Handling the photoresist requires a clean and controlled environment to prevent contamination. Adhering to processing times and temperatures during development ensures precise pattern transfer without overetching or underetching.
Etching precision machined silver materials requires a comprehensive understanding of the different types and alloys of silver, as well as the intricacies of electroforming, surface treatment, metal cleansing, and etching techniques. By selecting the most suitable processes and adhering to stringent precautions, manufacturers and engineers can fully leverage the unique properties of silver, contributing to advancements in critical industries such as electronics, jewelry, and industrial applications.
View our metal etching products
how to etch Silver?
Etching Silver Processing Guidelines
Metal Alloy | Etchant | Etching Temperature (°C) | Etching Concentration (%) | Estimated Etching Depth (microns) | Etching Quality |
---|---|---|---|---|---|
Etching Pure Silver | Ferric Nitrate (Fe(NO3)3) | Room temperature | 10-20% Fe(NO3)3 | 5-25 | High-quality (smooth) |
Etching Silver Copper (Ag-Cu) | Potassium Dichromate (K2Cr2O7) | Room temperature | 10-15% K2Cr2O7 | 5-25 | High-quality (smooth) |
Etching Silver-Zinc (Ag-Zn) | Nitric Acid (HNO3) | Room temperature | 10-15% HNO3 | 5-25 | High-quality (smooth) |
Etching Silver-Zinc (Ag-Zn) | Ammonium Persulfate ((NH4)2S2O8) | Room temperature | 10-15% (NH4)2S2O8 | 5-25 | High-quality (smooth) |
Etching Silver-Zinc (Ag-Zn) | Thiourea ((NH2)2CS) | Room temperature | 5-10% (NH2)2CS | 5-25 | High-quality (smooth) |
Etching Silver-Zinc (Ag-Zn) | Potassium Iodide (KI) | Room temperature | 10% KI | 5-25 | High-quality (smooth) |
The values provided are approximate and can vary depending on specific etching conditions, including exposure time and the condition of the silver or silver alloy surface. Always conduct test etches and adjust parameters as needed to achieve your desired results. Additionally, safety precautions should be followed when handling these chemicals, especially in the case of nitric acid and other strong oxidizing agents.
If you have metal wet etching Silver needs, please feel free to contact us.
FAQs
What metals can you use to customize my goods?
- Wet Etching Germanium
- Wet Etching Gallium Nitride (GaN)
- Wet Etching Indium
- Wet Etching Cobalt
- Wet Etching Tungsten
- Wet Etching Stainless Steel
- Wet Etching Aluminum
- Wet Etching Kovar
- Wet Etching Copper
- Wet Etching Steel
- Wet Etching Nickel
- Wet Etching Platinum
- Wet Etching Silver
- Wet Etching Rhodium
- Wet Etching Hafnium
- Wet Etching Vanadium
- Wet Etching Zirconium
- Wet Etching Titanium
- Wet Etching Niobium
- Wet Etching Tantalum
- Wet Etching Molybdenum
- Wet Etching Brass
- Wet Etching Rhenium
How quickly can I get your response?
Within 24 hours.
Will you do 100% inspection before shipping out the orders?
Yes we do.
Can I have prototypes or samples before placing the order?
Samples are always available.
Etching Silver Samples
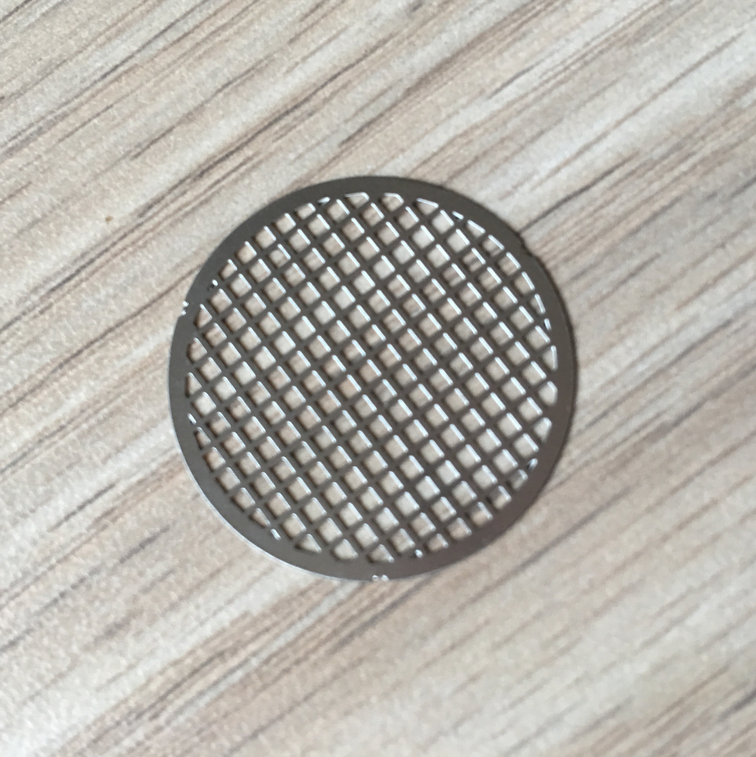
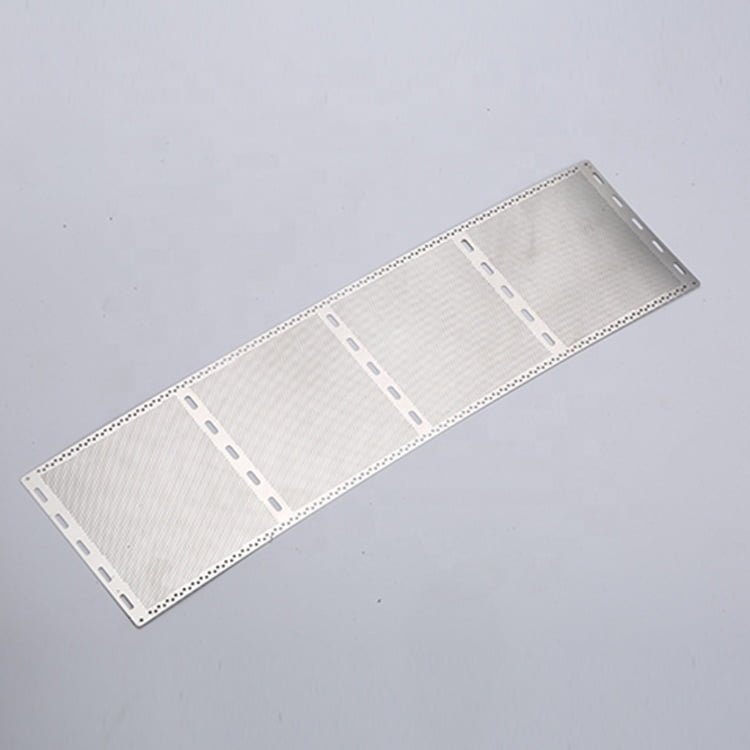
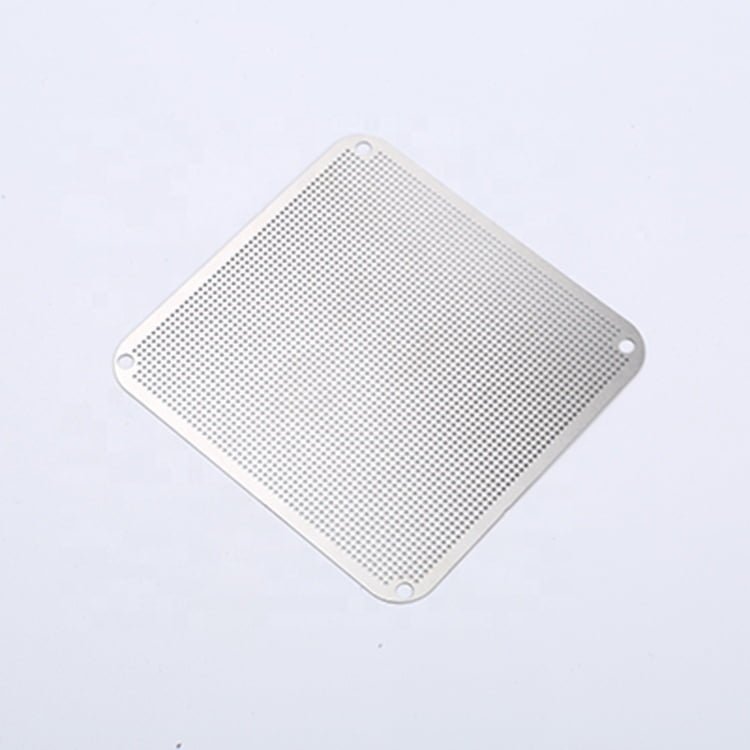
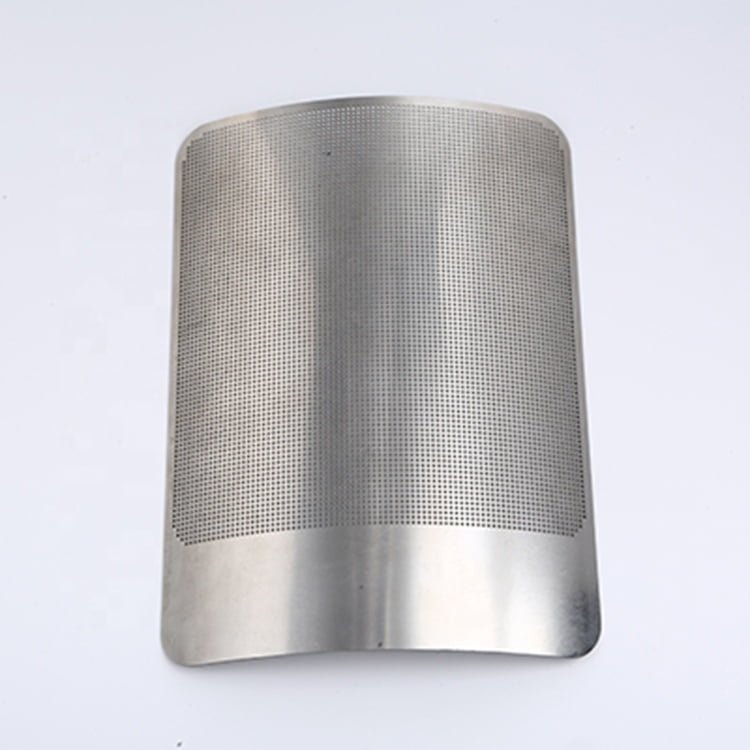
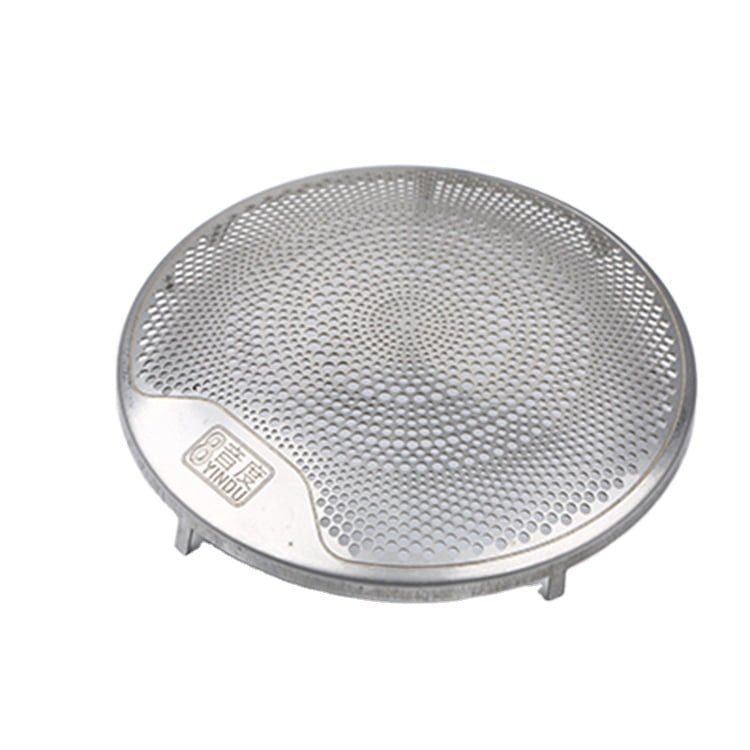
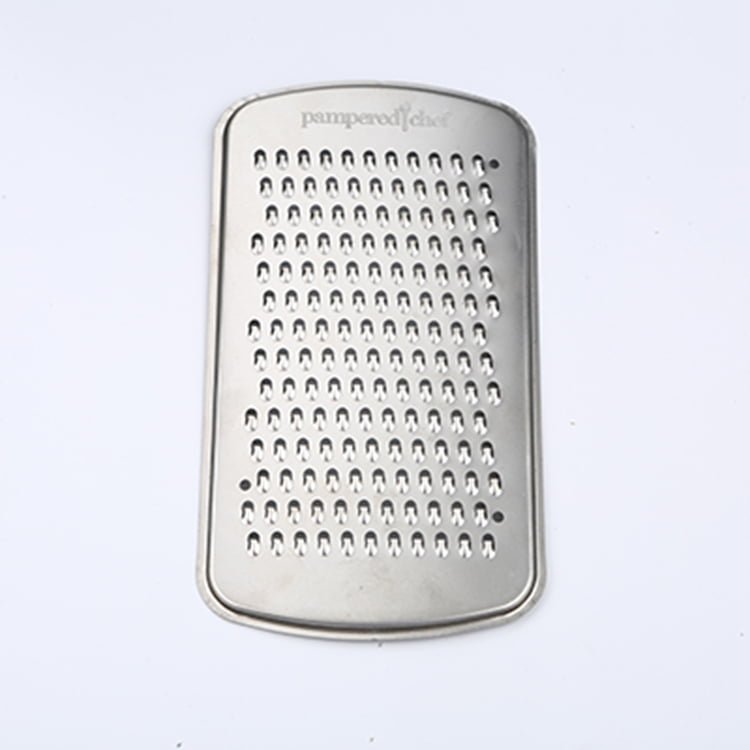
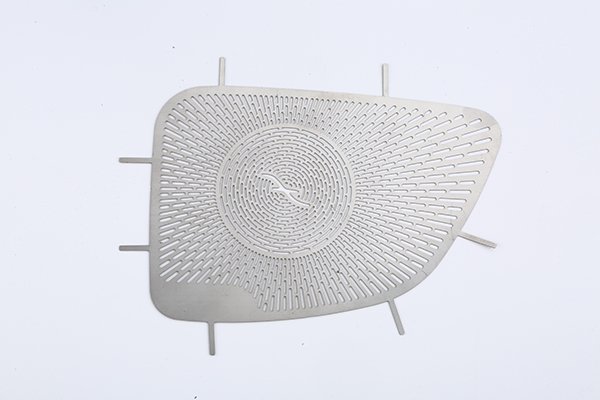
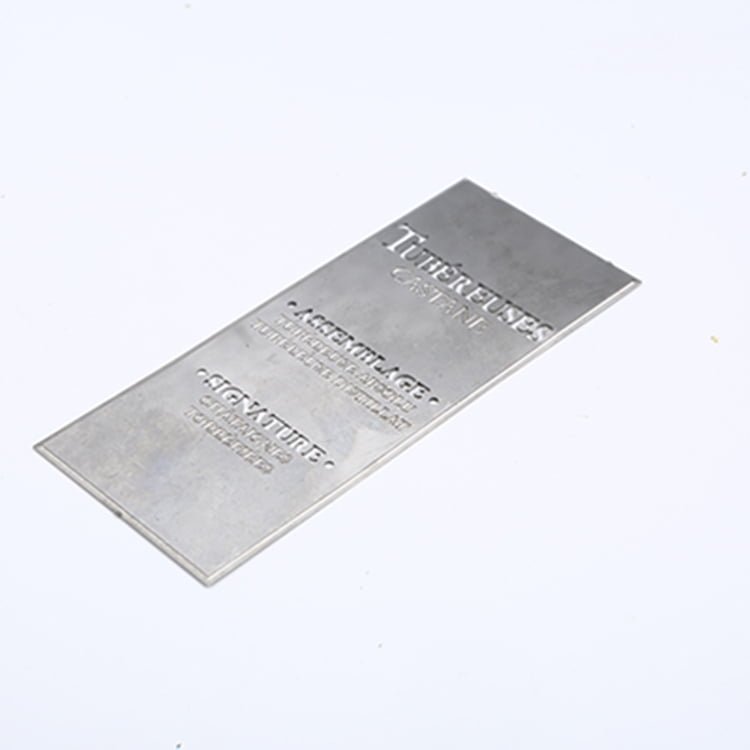
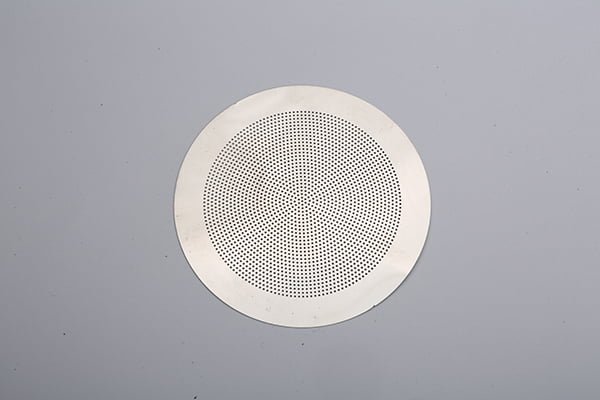
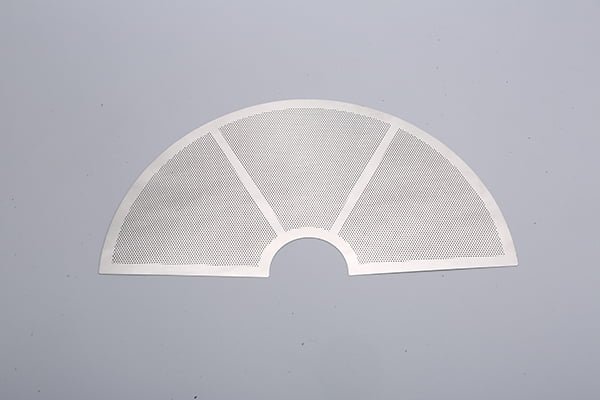
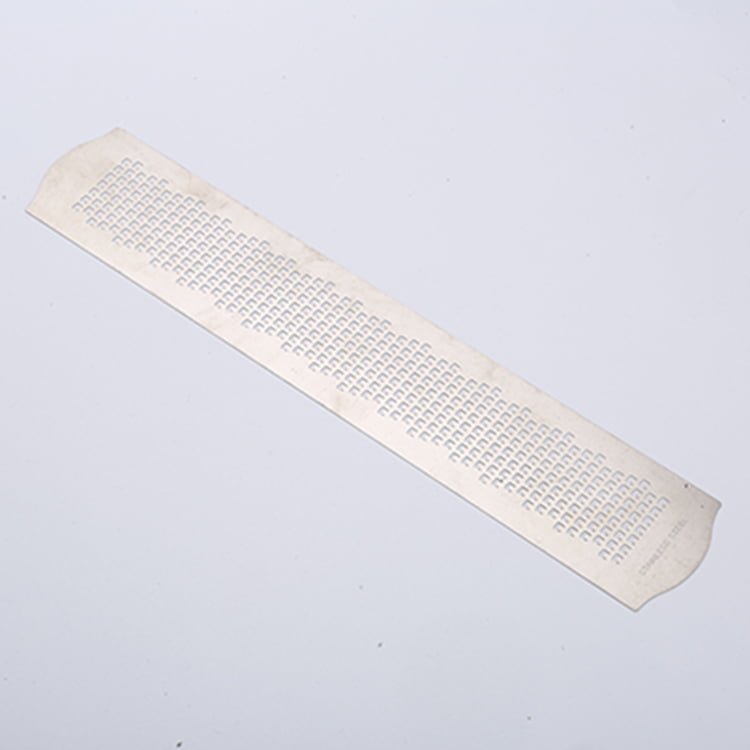
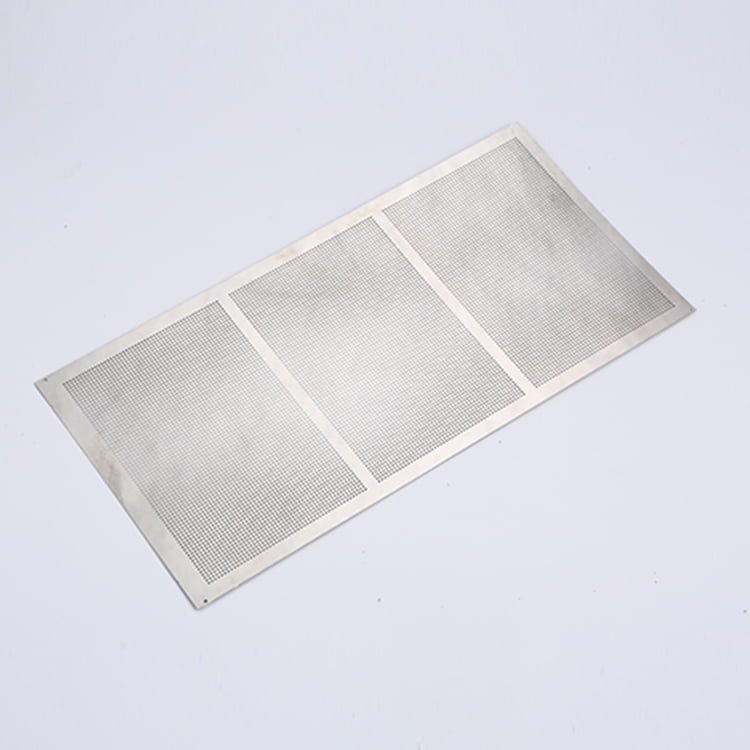
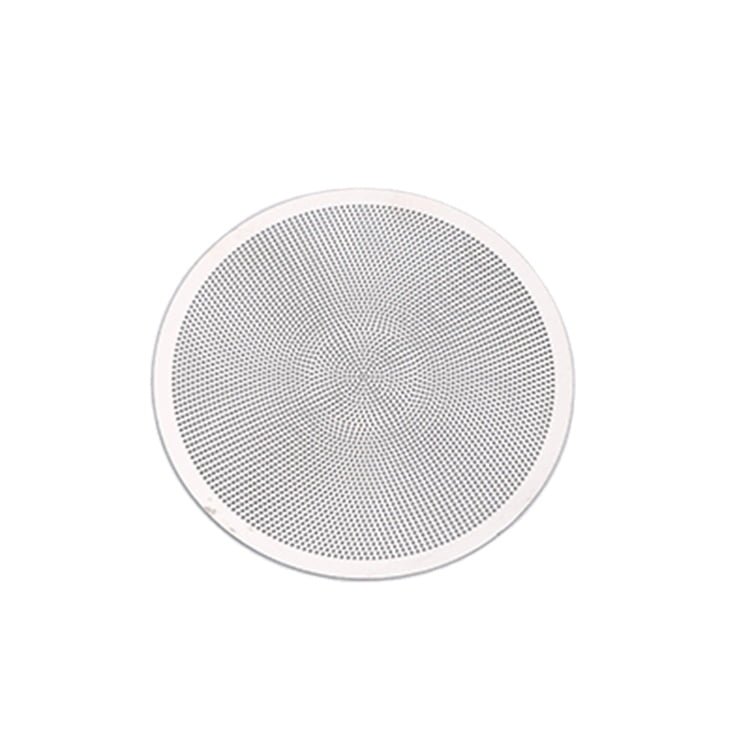
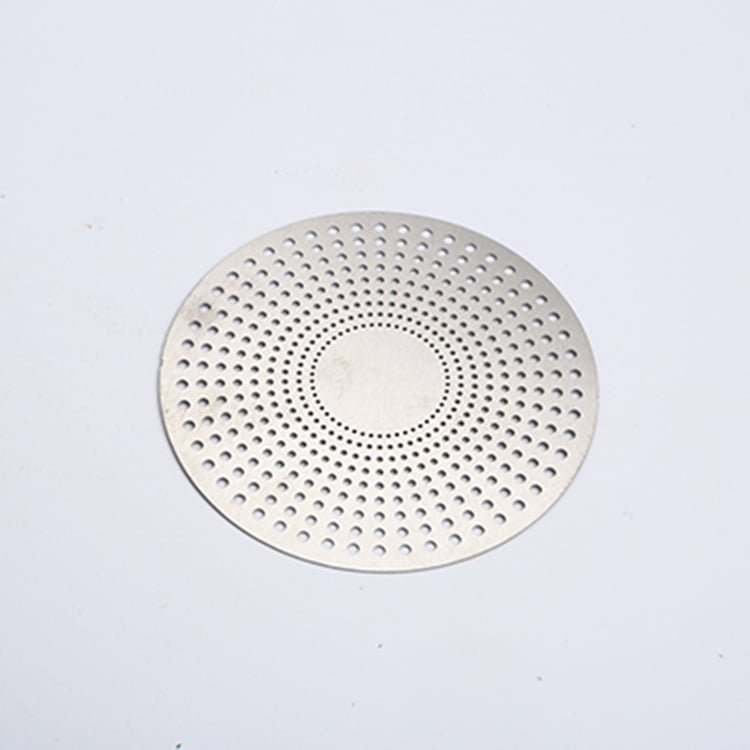
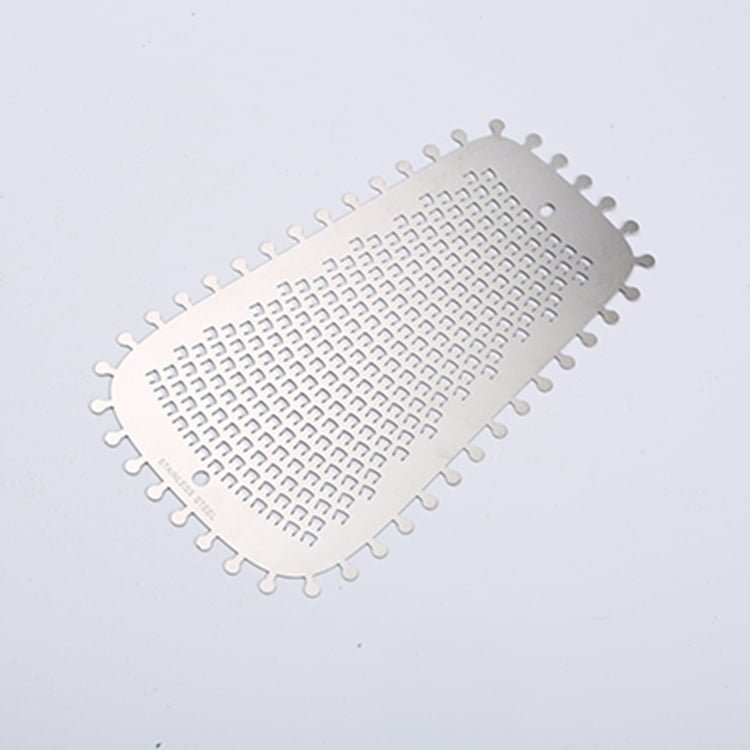
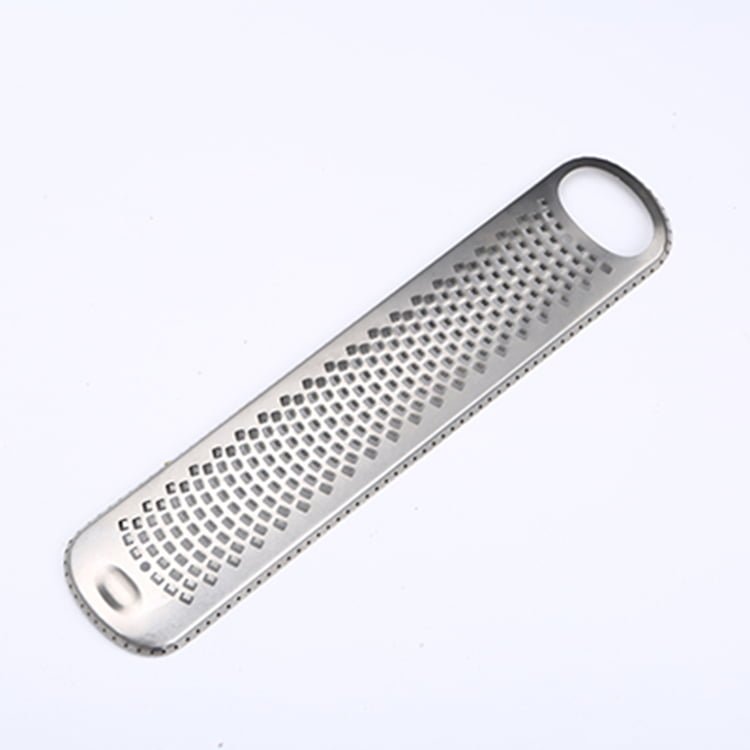
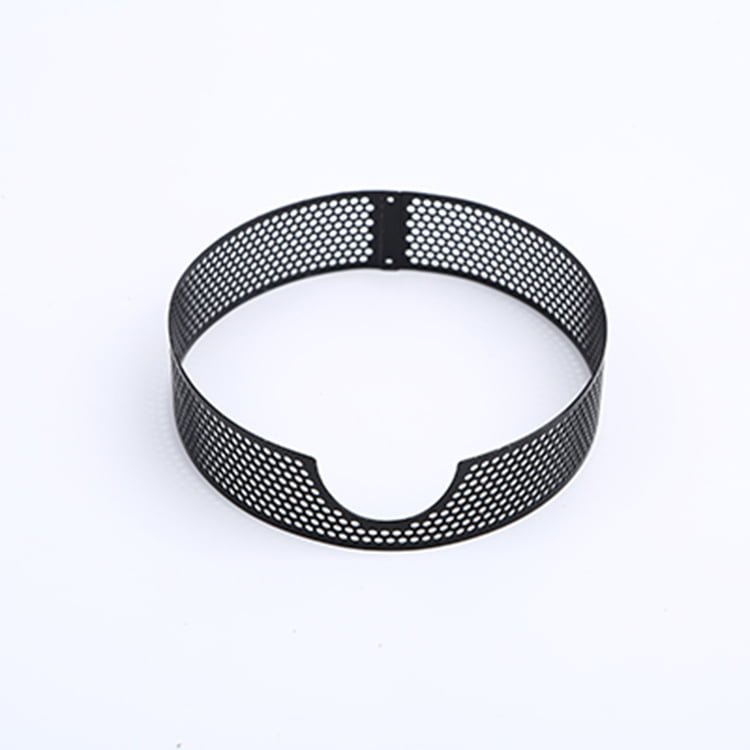

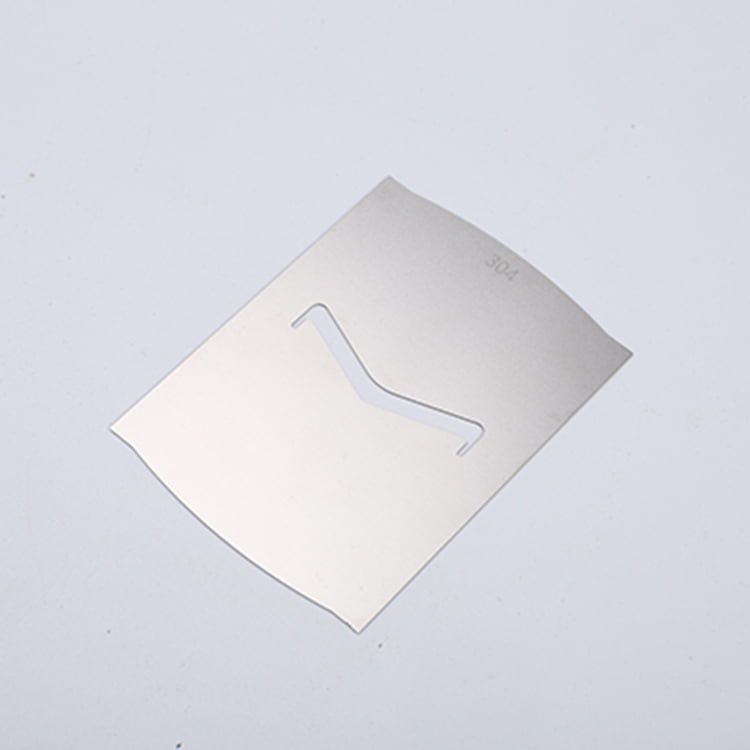

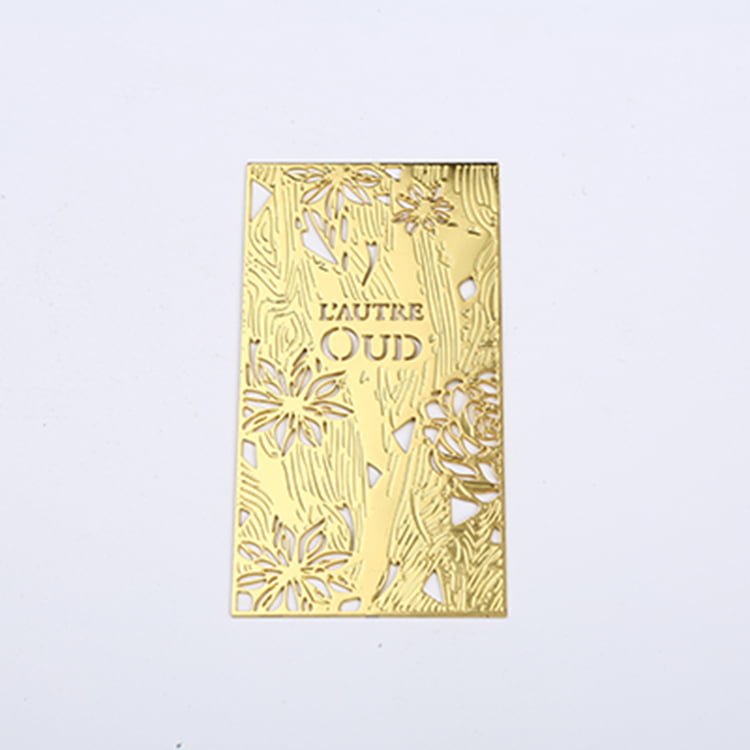

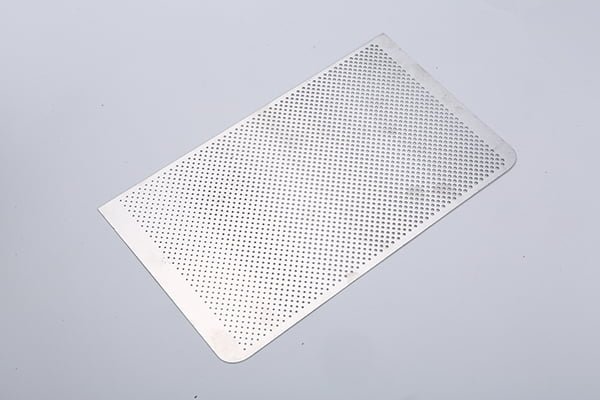