Wet chemical etching remains a foundational process in PCB manufacturing due to its precision, scalability, and cost-effectiveness. By understanding the nuances of the process, including etchant selection, temperature control, and proper maintenance, manufacturers can optimize their etching operations for better performance, fewer defects, and more reliable results. With the addition of automation and advanced monitoring systems, wet chemical etching continues to evolve, making it an indispensable method in the creation of high-quality printed circuit boards used in everything from consumer electronics to industrial machinery.
Chapter 1: The Role of Wet Chemical Etching in PCB Production
Wet chemical etching plays a critical role in the production of Printed Circuit Boards (PCBs), which are the backbone of modern electronics. The process is essential for creating intricate patterns and conductive traces on copper-clad boards, which are then used in everything from smartphones to industrial machinery.
In PCB manufacturing, the etching process allows manufacturers to precisely remove unneeded copper from the board, leaving behind fine patterns that form the circuits. According to a 2017 article by PCB manufacturer JLCPCB, wet chemical etching remains one of the most popular methods for PCB production due to its cost-effectiveness and ability to produce high-precision designs. The precision achieved through wet etching is crucial for today’s high-density PCBs, especially those used in high-frequency applications where accuracy is paramount.
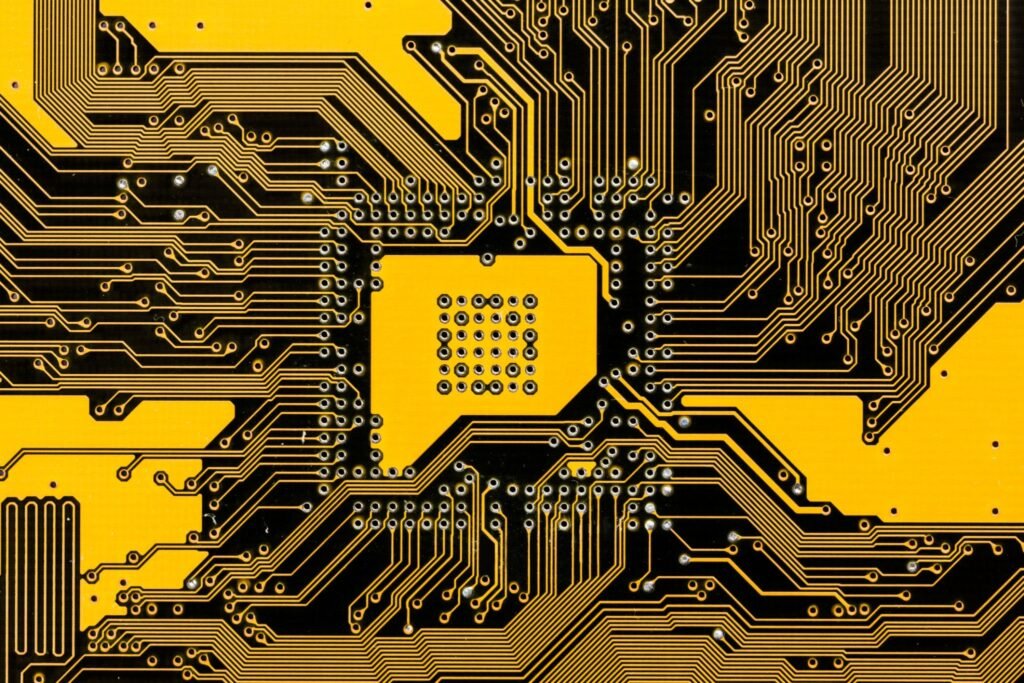
Chapter 2: Comparing Wet Chemical Etching with Other PCB Etching Methods
While wet chemical etching is commonly used in PCB manufacturing, it’s important to understand how it compares to other etching methods, such as laser etching and mechanical milling.
- Wet Chemical Etching: In this process, the PCB is coated with a light-sensitive photoresist that is exposed to UV light through a photomask. The exposed areas are then chemically etched away, leaving behind the desired copper traces. Wet etching is favored for its high precision, repeatability, and lower costs, particularly for large-scale production runs.
- Laser Etching: Laser etching uses high-powered lasers to burn away material from the PCB. While laser etching offers faster turnaround times and is ideal for low-volume production, it lacks the precision of wet chemical etching when it comes to fine traces. Laser etching also causes heat damage to the substrate material, which can impact the integrity of the PCB.
- Mechanical Milling: Mechanical milling, which involves using rotary tools to carve away material, is commonly used for prototyping and in applications where deep cuts are needed. However, it lacks the fine resolution and smoothness provided by wet chemical etching, making it less suitable for high-density, microcircuit design.
According to an article by PCB manufacturer Advanced Circuits, wet chemical etching is particularly suitable for high-volume production where precision and reduced manufacturing costs are critical.
Chapter 3: Key Parameters of Wet Chemical Etching for PCBs
Achieving optimal results with wet chemical etching requires careful control of several parameters. These include:
- Etchant Selection: The type of chemical solution used for etching is crucial to achieving the desired results. Common etchants for PCB etching include Cupric Chloride, Ferric Chloride, and Hydrofluoric Acid (HF). Each etchant has its own strengths, with Cupric Chloride being popular for its ability to regenerate, making it cost-effective for large-scale production.
- Temperature Control: The etching solution’s temperature affects the speed and quality of the etching process. Higher temperatures generally lead to faster etching, but they must be carefully controlled to prevent over-etching and ensure uniformity.
- Rinse and Drying Systems: After etching, PCBs must be thoroughly rinsed to remove any chemical residue. Drying systems must ensure that moisture does not remain on the PCB, as water can cause damage or corrosion.
- Masking and Exposure: The quality of the photomask and the exposure process can significantly impact the precision of the etching. High-quality masks and accurate exposure processes are key to achieving fine features on the PCB without under-etching or over-etching.
According to PCB supplier PCBWay, proper control of these parameters not only ensures high-quality etching but also extends the lifespan of equipment by reducing unnecessary wear from poor process control.
Chapter 4: Common Issues and How to Resolve Them
Despite its advantages, wet chemical etching can encounter several issues, such as over-etching, under-etching, and residue buildup. Understanding these common issues and knowing how to resolve them can help optimize the process.
- Over-Etching: Over-etching occurs when the etchant removes more material than intended, leading to thinner traces that could break or fail. This can be caused by overly aggressive etching solutions, incorrect temperature settings, or too long of an etching time. To prevent over-etching, ensure that the etching bath is carefully controlled, and the etching time is consistent.
- Under-Etching: Under-etching happens when some areas of the PCB aren’t fully etched, leaving behind unwanted copper. This is often due to improper exposure to light during the photomask process or insufficient etching time. To avoid under-etching, it’s crucial to ensure uniform exposure and proper etching time.
- Residue Buildup: Residue from the etching solution or photoresist can accumulate on the PCB, affecting quality and potentially causing short circuits. This can be solved by regularly cleaning the equipment and ensuring proper rinsing procedures.
As noted in a case study by PCB manufacturer PCB International, improving the cleanliness of the etching bath and ensuring regular maintenance of equipment can significantly reduce defects and improve the overall production yield.
Chapter 5: Optimizing the Etching Process for High-Volume PCB Production
When scaling up for high-volume PCB production, wet chemical etching can be optimized by integrating automation and continuous monitoring systems. Automated machines that can monitor parameters such as etching speed, chemical concentration, and bath temperature provide a significant advantage in achieving consistent results.
Several manufacturers, including Eurocircuits, have adopted automated wet etching systems that allow for precise control over each batch, reducing variability and ensuring that each PCB meets high-quality standards. These systems use recipe-driven operation to ensure consistency across different production runs and minimize the likelihood of human error.
The integration of data collection systems further enhances this process, allowing manufacturers to analyze historical data and optimize future runs based on real-time feedback. According to NCAB Group, this data-driven approach has helped improve production yield and reduce downtime by identifying potential issues before they become problems.