Chemical etching is a precision process that plays a significant role in modern manufacturing, especially when it comes to intricate patterns and designs on materials such as stainless steel. This method is highly valued for its ability to produce complex geometries, fine details, and burr-free edges. In industries such as aerospace, automotive, and medical devices, where the highest level of accuracy is required, chemical etching offers an excellent alternative to mechanical cutting techniques.
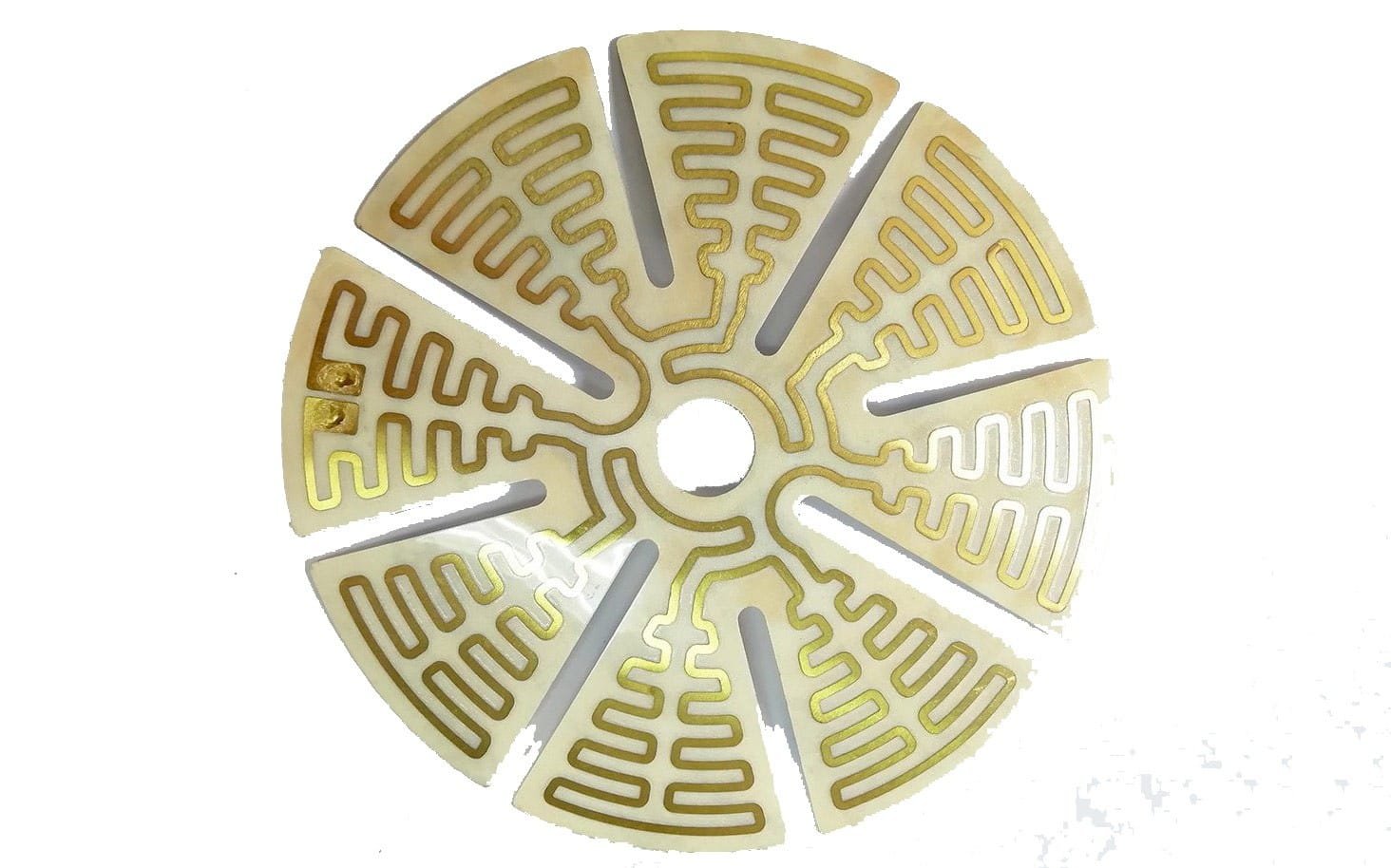
What Is Chemical Etching Stainless Steel?
Chemical etching, also referred to as photochemical machining (PCM) or chemical milling, is a technique used to remove material from stainless steel surfaces using acidic solutions. This process is not only precise but also cost-effective, providing a clean and highly accurate alternative to traditional mechanical cutting methods. By using chemicals such as Ferric Chloride or Nitric Acid, manufacturers can achieve intricate designs with tight tolerances on stainless steel parts. The process is highly adaptable, making it suitable for producing parts with a wide range of thicknesses and complexities.
The ability to create high-precision features without inducing stress in the material is one of the key advantages of this process. Unlike mechanical methods, chemical etching eliminates tool wear and distortion, resulting in a more efficient and environmentally friendly manufacturing solution.
Definition and Core Principles
At its core, chemical etching is a process that involves using a photoresist mask to protect certain areas of the stainless steel, while exposing others to an etching solution. The exposed metal reacts with the etching solution, dissolving the material in the exposed areas, leaving behind the desired pattern or design.
The core principles behind this process include:
- Precision: The ability to create detailed and fine patterns with very tight tolerances (up to 0.002 mm).
- Efficiency: Faster production times compared to traditional mechanical methods, especially for high-volume manufacturing.
- No Material Stress: Unlike cutting or grinding, chemical etching does not cause stress or distortion in the material.
- Environmentally Friendly: The process can be optimized to produce less waste and requires less energy than traditional methods.
How Acid-Based Etching Works on Stainless Steel
Acid-based etching works by using strong acid solutions, typically Ferric Chloride or Nitric Acid, to etch the exposed areas of the stainless steel. The process is initiated once a photoresist mask is applied to the material. Areas not covered by the mask are then exposed to the etching solution, which dissolves the metal in a controlled manner.
Here is a simplified explanation of the acid-based etching process:
- Coating: The stainless steel is coated with a photoresist material.
- Exposure: The coated material is exposed to UV light through a photomask, which defines the pattern to be etched.
- Developing: The exposed areas are chemically removed, revealing the pattern.
- Etching: The stainless steel is immersed in an etching solution, removing the unprotected metal areas.
- Post-etching: The surface is cleaned and, if necessary, passivated to prevent corrosion.
Key Advantages Over Mechanical Cutting
Chemical etching offers several significant advantages over traditional mechanical cutting methods, particularly for applications requiring precision and intricate designs.
Advantage | Chemical Etching | Mechanical Cutting |
---|---|---|
Precision | Can achieve fine details with high accuracy (up to 0.002mm tolerance) | Limited precision for intricate patterns |
Edge Quality | Produces burr-free edges, requiring less finishing | Often results in burrs or rough edges |
Tool Wear | No tool wear – consistent results | Tools wear out and require frequent replacement |
Speed | Faster for high-volume production | Slower for intricate and high-volume work |
Material Stress | No material stress or distortion | Potential for material distortion due to cutting forces |
Step-by-Step Process Breakdown
The chemical etching process involves several carefully controlled steps, each of which contributes to the creation of a high-quality, precise etched part. Below is an overview of the essential stages:
Material Preparation (Cleaning, Coating)
Before the etching process begins, the stainless steel needs to be thoroughly cleaned to remove any oils, dirt, or oxidation. This ensures that the etching solution can properly adhere to the exposed areas. After cleaning, a light coating of photoresist is applied to the material to protect areas that should remain unetched.
Photolithography and Mask Alignment
In this step, photolithography is used to create the design pattern on the stainless steel. The photoresist layer is exposed to UV light through a photomask that defines the pattern. This step requires precise alignment to ensure that the pattern is accurately transferred to the material.
Etching Solutions (Ferric Chloride, Nitric Acid)
The next step is immersing the stainless steel in an etching solution, usually Ferric Chloride or Nitric Acid. These acids react with the exposed areas, dissolving the metal and leaving behind the protected areas of the pattern. The etching time and temperature are carefully controlled to achieve the desired depth and precision.
Post-Etching Treatments (Passivation, Rinsing)
After the etching process is complete, the stainless steel is thoroughly rinsed to remove any remaining chemicals. Passivation is then performed to enhance the material’s corrosion resistance. This post-treatment ensures that the etched parts are durable and ready for use in demanding applications.
Material Compatibility and Selection
Selecting the appropriate material for chemical etching is crucial for achieving optimal results. Different grades of stainless steel offer varying properties that affect their performance in etching.
Best Stainless Steel Grades for Etching (304, 316, 430)
When choosing stainless steel for chemical etching, 304, 316, and 430 are commonly used grades. Below is a comparison table of their key properties and applications:
Grade | Properties | Applications |
---|---|---|
304 | Excellent corrosion resistance, good formability | General industrial applications, kitchenware |
316 | Superior corrosion resistance, especially in marine environments | Marine, pharmaceutical, food processing industries |
430 | Good formability, cost-effective | Decorative applications, automotive trim |
Thickness Guidelines (0.1mm to 2.0mm)
Chemical etching is effective on stainless steel sheets ranging from 0.1mm to 2.0mm in thickness. Thinner materials are typically etched with higher precision, making them suitable for delicate designs, while thicker materials allow for deeper etching but may require longer exposure times.
Surface Finish Options (Brushed, Mirror, Satin)
The surface finish of the stainless steel also plays a critical role in the etching process. Different finishes affect both the etching quality and the final appearance of the part. Common finishes include:
- Brushed: Provides a matte texture, ideal for non-reflective parts.
- Mirror: A highly reflective finish, often used in decorative applications.
- Satin: A semi-gloss finish that is less reflective than mirror finishes.
Industrial Applications of Etched Stainless Steel
Chemical etching of stainless steel is applied in many industries due to its versatility and precision. Below are some notable applications:
Aerospace (Fuel Cell Components, Sensor Meshes)
In the aerospace industry, etched stainless steel is used for components like fuel cell parts and sensor meshes, which require high precision to withstand extreme temperatures and pressures.
Medical Devices (Surgical Tools, Implant Markings)
Medical devices such as surgical tools and implant markings benefit from the high biocompatibility and precision of etched stainless steel, ensuring that these critical devices meet stringent regulatory standards.
Automotive (EMI Shields, Decorative Trims)
In the automotive sector, etched stainless steel is used to produce EMI shields and decorative trims. The process allows for the creation of complex geometries that are essential for electromagnetic interference protection and aesthetic components.
Solving Common Etching Challenges
Despite its many benefits, chemical etching comes with its own set of challenges. Proper control and understanding of the process can mitigate these issues.
Over-Etching and Undercutting Prevention
To avoid over-etching (where excess material is removed) and undercutting (where material beneath the mask is also etched), it’s essential to control the etching time, temperature, and chemical concentration precisely.
Burr-Free Edge Requirements
One of the key benefits of chemical etching is burr-free edges, but improper etching can still result in rough or jagged edges. Ensuring the right balance of etching conditions will help maintain the clean, smooth edges required for many applications.
Environmental Compliance (Waste Acid Disposal)
The use of acidic etching solutions requires careful handling and disposal. Environmental compliance is crucial, and manufacturers must ensure that waste chemicals are neutralized and disposed of according to local regulations to minimize the environmental impact.