The precision and flexibility of chemical etching play a pivotal role in the production of thin film heating elements. By leveraging advanced manufacturing techniques like laser cutting, pattern optimization, and material compatibility management, manufacturers can create highly efficient, customizable heating solutions. The ability to scale production—from prototyping to mass manufacturing—ensures that thin film heaters continue to meet the evolving needs of industries like automotive, medical, and consumer electronics.
The Role of Chemical Etching in Heater Fabrication
Chemical etching is one of the most critical processes in the manufacturing of thin film heating elements. This technique involves selectively removing material from a metal surface to create intricate patterns, ensuring precise heat distribution. During the chemical etching process, a photoresist is applied to a metal substrate, which is then exposed to UV light and developed to reveal the desired pattern. The metal is then exposed to a chemical etchant that removes the unprotected material, leaving behind the etched design.
The key benefit of chemical etching is its ability to produce high-precision patterns on thin metal films, which is essential for optimizing heat transfer and ensuring uniform heating across the element. This process can be used with metals like aluminum, copper, and stainless steel, which are commonly used in thin film heaters for their excellent thermal conductivity and durability.
Chemical etching allows for the creation of complex, fine features in the heater’s pattern, such as serpentine or grid structures, which maximize the surface area and enhance thermal efficiency. This precision is critical in applications requiring exact temperature control, such as medical devices and automotive systems.
Laser Cutting vs. Etching: Pros and Cons
While chemical etching is widely used for thin metal films, another popular method is laser cutting. Both techniques have their strengths, and choosing the right one depends on the specific requirements of the application.
- Laser Cutting:
- Pros: Laser cutting is ideal for thicker metals or when intricate patterns are required in a non-thin film design. It offers precision in cutting complex geometries and can work with a wide variety of metals.
- Cons: Laser cutting tends to be more expensive than chemical etching, especially for mass production. It is also less efficient when dealing with ultra-thin materials due to the potential for heat distortion.
- Chemical Etching:
- Pros: For thin films, chemical etching is generally more cost-effective and faster than laser cutting. The process doesn’t introduce heat into the material, preventing thermal distortion. It’s ideal for high-precision patterns in thin metals like aluminum and copper.
- Cons: While it’s highly effective for thin materials, chemical etching becomes less viable for thicker substrates where it may not provide the same clean cut as laser cutting.
In general, chemical etching is the preferred technique for fabricating thin film heating elements because of its superior precision, efficiency, and cost-effectiveness in mass production. However, laser cutting may be used for thicker metal layers or certain applications where higher thickness tolerance is required.
Optimizing Heat Distribution Through Patterning
The key to efficient heating with thin film heaters lies in the design of the etched pattern. Chemical etching allows for highly intricate and uniform designs that optimize the heat distribution across the heating element.
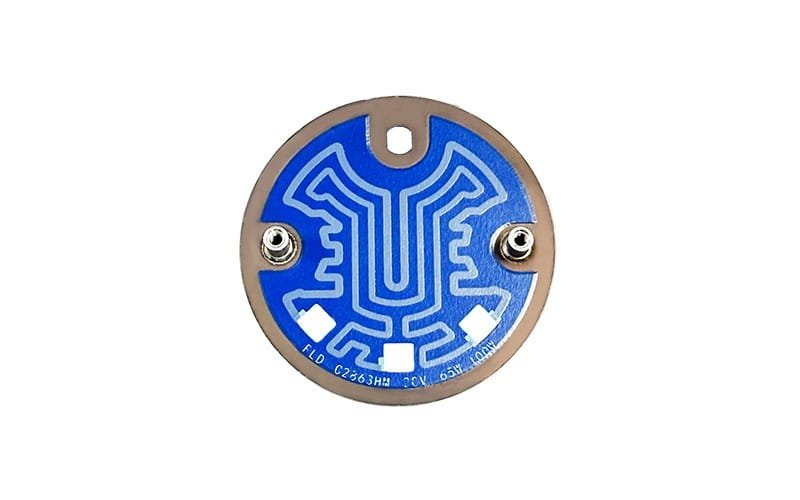
- Serpentine Patterns: One of the most commonly used patterns in thin film heating elements is the serpentine design. This zig-zag shape maximizes the surface area, providing more efficient heat transfer. The longer path length ensures that heat is distributed more evenly over a larger area.
- Grid Patterns: In some applications, grid patterns are used to further improve the uniformity of heat distribution. Grid designs also help in controlling the current flow more precisely, allowing for optimized heating performance.
These patterns are often designed using computer-aided design (CAD) software to ensure that the heating element meets the specific requirements of the application. Through precise etching, manufacturers can fine-tune the distribution of heat to ensure it matches the needs of the device, whether it’s for heating a small component like a battery or a large surface like a windshield.
Material Compatibility and Etching Challenges
Not all metals are created equal when it comes to chemical etching. The choice of material for the substrate directly impacts the quality of the etching process and the performance of the final product. For example, metals like aluminum and copper are commonly used in thin film heating elements because of their excellent thermal conductivity. However, these metals present unique challenges during etching.
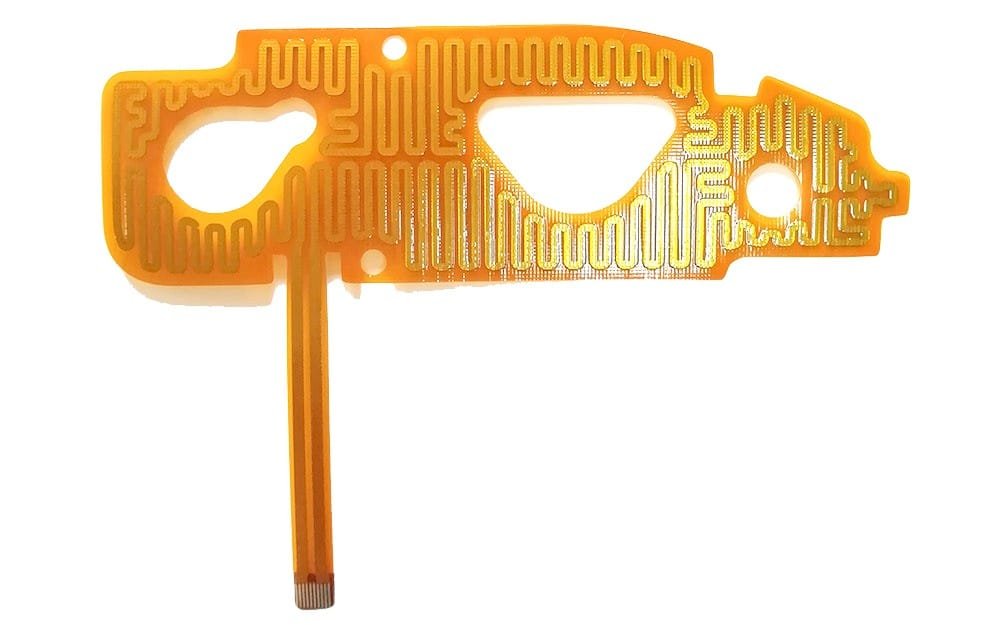
- Aluminum:
Aluminum is highly reactive with acids, so it requires careful control of the etching solution to prevent over-etching or unwanted surface roughness. To overcome this, manufacturers may use a two-step process that includes a pre-treatment phase to prepare the surface. - Copper:
Copper is another popular choice due to its high thermal conductivity, but it can also be prone to oxidation, which can impact the quality of the etching. Copper surfaces need to be carefully cleaned and prepared before etching to ensure a clean, precise cut. - Stainless Steel:
Stainless steel is durable and resistant to corrosion, making it ideal for high-temperature applications. However, stainless steel requires more aggressive etchants and longer exposure times, which can increase production costs and lead time.
Manufacturers need to carefully select etching solutions and adjust process parameters to ensure that they don’t compromise the quality or performance of the material.
Scaling Production: From Prototyping to Mass Manufacturing
Scaling the production of thin film heating elements requires careful consideration of the manufacturing process. Once a prototype is developed and tested, the next step is to transition to high-volume manufacturing.
- Prototyping:
In the prototyping phase, photochemical machining is often used to create small batches of thin film heaters. This method is highly effective for low-volume production, allowing designers to test different materials, patterns, and configurations. - Mass Manufacturing:
For large-scale production, stamping or automated chemical etching processes are often used. Stamping involves using a die to create patterns on metal sheets, which is an efficient method for high-volume orders. While the initial setup cost can be high, stamping is very cost-effective for producing large quantities of thin film heaters. - Cost and Lead Time Considerations:
While photochemical machining is faster for prototyping, it can be more expensive for large batches compared to stamping. Manufacturers must weigh the benefits of each process depending on the scale of the production run and the desired lead time.