Electroforming and chemical etching are both precision manufacturing processes, but they differ fundamentally in their principles, applications, and outcomes. Here’s an analysis comparing Veco precision Advanced Electroforming process with chemical etching:
Table of Contents
View or download our Photochemical Metal Etching White Paper How-to Guide
1. Principle
- Electroforming: Electroforming is an additive process where metal is deposited onto a mandrel (substrate) using an electrolytic bath. Metal builds up on the patterned areas of the mandrel, creating a new metal structure that can later be separated.
- Chemical Etching: Chemical etching is a subtractive process that removes material from a metal surface through the application of acids or alkaline etchants. A photoresist protects the areas not to be etched, leaving precise shapes and patterns by selectively dissolving exposed areas.
2. Material Application
- Electroforming: Often used for applications requiring high precision and complex geometries, such as high-quality filters, meshes, optical components, microelectronic parts, and microfluidic devices. Electroforming can produce very thin or very thick metal layers, making it versatile for both fine and large-scale parts.
- Chemical Etching: While chemical etching is commonly associated with simpler, flat parts like signs, labels, and nameplates, it can also be used to produce filters, meshes, and microelectronic components with very high precision. Just like electroforming, chemical etching can create fine holes and complex patterns for applications such as fuel cell plates, RF shielding, and MEMS components (Micro-Electro-Mechanical Systems). The advantage of chemical etching here is that it doesn’t introduce any thermal or mechanical stress into the material, preserving the integrity of the components.
- Conclusion: Both electroforming and chemical etching can produce filters, meshes, and microelectronic components, but electroforming excels in cases where the structural strength and thickness are critical, while chemical etching is faster and less costly for large-scale production of thinner components.
3. Precision and Detail
- Electroforming: Electroforming allows for the creation of intricate 3D structures and high aspect ratios with extremely fine details. Due to the layer-by-layer deposition of metal, the process can achieve features down to microns in size, making it ideal for highly detailed parts.
- Chemical Etching: While chemical etching can produce highly detailed 2D shapes with sharp edges and fine resolution, it is primarily limited to flat or slightly contoured surfaces. Chemical etching achieves fine detail through the control of etchant exposure, allowing for etched holes as small as a few microns.
4. Thickness Control
- Electroforming: Thickness control in electroforming is excellent, as the thickness of the electroformed part is directly related to the duration of metal deposition in the electrolytic bath. Electroforming can create very thin layers (in the micron range) or thicker parts depending on the requirements. It is particularly useful when consistent wall thickness across a complex 3D shape is essential.
- Chemical Etching: Thickness control is more limited, as the process depends on how deep the etchant penetrates the exposed areas. While it is effective for thin sheet materials, achieving thicker components is difficult because the process is designed for removal rather than build-up.
5. Dimensional Tolerances (Expanded)
- Electroforming: Due to the precise control over the deposition process, electroforming can achieve extremely tight dimensional tolerances, typically within ±1 to 3 microns. This makes it ideal for applications where exact dimensions are critical, such as in precision optical components, microfilters, and microelectronic parts. The electrolytic deposition process is uniform, ensuring that the final product meets strict geometric and tolerance requirements.
- Chemical Etching: While chemical etching can also achieve fine tolerances for thin materials, the dimensional tolerance is generally less precise compared to electroforming. Typical tolerances for chemical etching range from ±10 microns to ±50 microns, depending on the material thickness and the complexity of the design. However, this is often sufficient for parts like precision shims, stencils, and electronic components. It can also achieve tight tolerances across large production runs.
6. Mechanical Properties
- Electroforming: Since electroforming builds the part through metal deposition, the final structure has mechanical properties close to bulk material. Electroformed parts exhibit high strength, durability, and excellent surface smoothness. The deposition process produces dense and void-free metal layers, making it suitable for parts that need to withstand mechanical stress or harsh environments.
- Chemical Etching: The mechanical properties of the part depend entirely on the original material used, as chemical etching simply removes material from the surface. It’s generally used for thinner components and might weaken structural integrity if very fine features are etched away. However, this process is gentle and does not introduce any heat or stress, which is beneficial for maintaining the material’s original properties.
7. Cost and Scalability
- Electroforming: The process is typically more expensive and time-consuming than chemical etching due to the complexity of electroplating and the need for precise controls. Electroforming is often reserved for high-precision, low-volume production, where the unique benefits of the process justify the higher cost. It’s commonly used in aerospace, optics, micro-electronics, and medical applications.
- Chemical Etching: Chemical etching is generally more cost-effective for producing high volumes of parts, especially in industries like automotive, electronics, and signage. The relatively simple setup and faster cycle times make it ideal for mass production, especially when working with thin metal sheets.
8. Surface Finish
- Electroforming: Parts produced through electroforming typically have smooth, high-quality surface finishes, often requiring little to no post-processing. The deposition process ensures a uniform surface, which is particularly beneficial for parts with optical properties or aesthetic requirements.
- Chemical Etching: Surface finishes from chemical etching are generally good but may require additional post-processing to achieve a polished appearance. The chemical reaction can leave a slightly rough surface depending on the material and the type of etchant used, though additional steps like polishing or passivation can improve this.
If you have metal wet etching needs, please feel free to contact us.
FAQs
What metals can you use to customize my goods?
- Wet Etching Germanium
- Wet Etching Gallium Nitride (GaN)
- Wet Etching Indium
- Wet Etching Cobalt
- Wet Etching Tungsten
- Wet Etching Stainless Steel
- Wet Etching Aluminum
- Wet Etching Kovar
- Wet Etching Copper
- Wet Etching Steel
- Wet Etching Nickel
- Wet Etching Platinum
- Wet Etching Silver
- Wet Etching Rhodium
- Wet Etching Hafnium
- Wet Etching Vanadium
- Wet Etching Zirconium
- Wet Etching Titanium
- Wet Etching Niobium
- Wet Etching Tantalum
- Wet Etching Molybdenum
- Wet Etching Brass
- Wet Etching Rhenium
How quickly can I get your response?
Within 24 hours.
Will you do 100% inspection before shipping out the orders?
Yes we do.
Can I have prototypes or samples before placing the order?
Samples are always available.
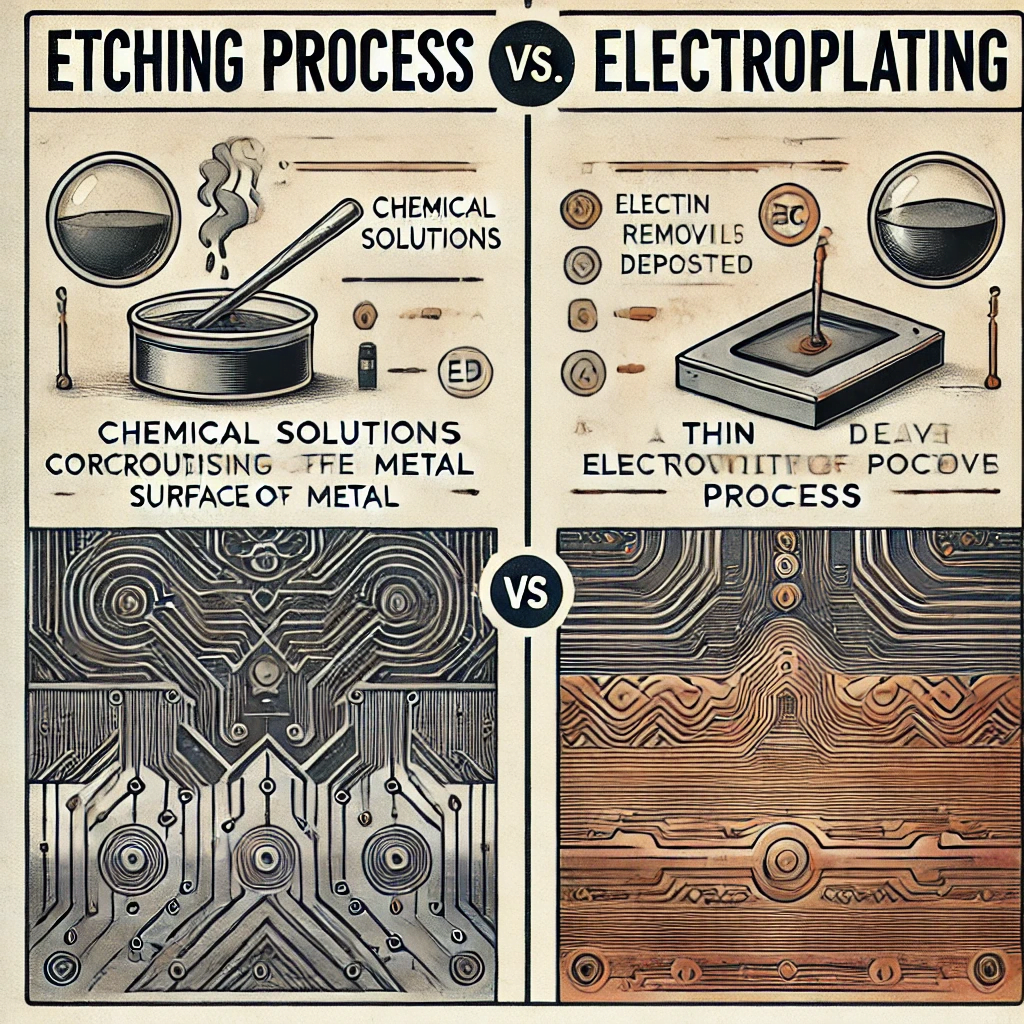
For metal processing factories
To discuss the differences between building a precision etching factory and a precision electroforming factory, we will look at several cost factors such as labor, utilities (water and electricity), environmental controls, rent, auxiliary equipment (ventilation, exhaust systems), technical workforce, research & development (R&D), and more.
1. Cost to Build a Precision Etching Factory
1.1 Machinery & Equipment:
- Etching Equipment: Precision etching machinery varies depending on the materials and thicknesses involved. High-end machines with automated resist coating, etching tanks, and waste treatment systems can range from $50,000 to $500,000. This also includes photoresist application machines and etchant regeneration systems.
- Auxiliary Equipment: Ventilation systems, exhaust gas scrubbers, and waste disposal systems are essential to ensure environmental safety. These systems can range from $30,000 to $200,000 depending on the factory’s size and local environmental standards.
1.2 Labor:
- Technicians & Operators: Skilled workers are needed to operate the machines and handle chemicals. Labor costs vary by location, but for a medium-sized etching factory, labor may be around $40,000 to $60,000 per worker annually.
- R&D and Quality Control: Precision etching requires continuous improvement, especially for custom or high-precision parts. Additional R&D and quality control workers can raise labor costs, adding another $100,000 to $300,000 annually depending on the team size.
1.3 Utilities (Water, Electricity, Chemicals):
- Water: Water is needed for rinsing etched components. A medium-sized etching facility might require 100,000 to 200,000 gallons of water monthly, translating into a monthly cost of $1,000 to $5,000, depending on location.
- Electricity: Power consumption is relatively moderate compared to electroforming. Expect monthly electricity bills around $5,000 to $20,000 for a small-to-medium-sized facility, depending on the machines’ power requirements.
- Chemicals: The cost of etchants (such as ferric chloride or other acids) is a major ongoing expense, ranging from $10,000 to $50,000 per month based on the scale of production.
1.4 Rent and Environmental Controls:
- Factory Rent: Industrial rent varies greatly by region, but a typical facility for chemical etching may require 10,000 to 30,000 sq. ft. of space. Rent could range from $10,000 to $100,000 per month depending on location.
- Environmental Controls: Strict environmental regulations are associated with chemical etching. Costs for ventilation, exhaust systems, and waste treatment can be significant, adding $50,000 to $200,000 in upfront investment, and $2,000 to $10,000 per month in operating costs.
2. Cost to Build a Precision Electroforming Factory
2.1 Machinery & Equipment:
- Electroforming Equipment: Electroforming requires specialized electroplating tanks, mandrels, power supplies, and automation controls for precise deposition. High-end systems can cost from $100,000 to $1 million or more, depending on the size of the factory and the complexity of parts being produced.
- Auxiliary Equipment: Electroforming also requires ventilation systems and waste management, though the chemicals used (such as nickel, copper, or gold) are generally less harmful than those in etching. Costs for these systems can range from $20,000 to $150,000.
2.2 Labor:
- Technicians & Operators: Like etching, skilled workers are needed to operate electroforming machinery and monitor the electroplating process. However, electroforming requires highly skilled workers due to the need for precise control of plating thickness and uniformity. Annual labor costs may range from $50,000 to $80,000 per worker.
- R&D and Quality Control: Since electroforming is more sensitive to variations in thickness and uniformity, additional investment in R&D and quality control is necessary. This can range from $150,000 to $500,000 annually for a medium-sized factory.
2.3 Utilities (Water, Electricity, Chemicals):
- Water: Water consumption for electroforming is lower compared to etching, mainly needed for rinsing between electroplating steps. Monthly water costs could range from $500 to $3,000.
- Electricity: Electroforming consumes more power due to the use of electrolytic baths and power supplies for metal deposition. Monthly electricity costs might be $10,000 to $30,000 for a medium-sized factory.
- Chemicals: Electroforming requires electrolytes and metals (such as nickel, copper, and gold), which are expensive. Monthly chemical costs could range from $20,000 to $100,000 depending on the scale of production and the type of metals used.
2.4 Rent and Environmental Controls:
- Factory Rent: Electroforming facilities may require similar space to etching plants, but due to the need for strict temperature and humidity controls, rent might be slightly higher, ranging from $15,000 to $120,000 per month for a 10,000 to 30,000 sq. ft. factory.
- Environmental Controls: Electroforming is generally less harmful to the environment than etching but still requires proper ventilation and chemical disposal systems. Upfront investments in environmental systems might be $30,000 to $150,000, with monthly costs for operation ranging from $1,000 to $8,000.
Comparison Table: Precision Etching vs. Electroforming Factory Setup Costs
Cost Factor | Precision Etching | Precision Electroforming |
---|---|---|
Machinery & Equipment | $50,000 to $500,000 (etching machines, resist, waste systems) | $100,000 to $1 million (electroplating systems, automation) |
Auxiliary Equipment | $30,000 to $200,000 (ventilation, exhaust, waste disposal) | $20,000 to $150,000 (ventilation, disposal systems) |
Labor Costs | $40,000 to $60,000 per worker annually | $50,000 to $80,000 per worker annually |
R&D and Quality Control | $100,000 to $300,000 annually | $150,000 to $500,000 annually |
Water Costs | $1,000 to $5,000 monthly | $500 to $3,000 monthly |
Electricity Costs | $5,000 to $20,000 monthly | $10,000 to $30,000 monthly |
Chemical Costs | $10,000 to $50,000 monthly | $20,000 to $100,000 monthly |
Factory Rent | $10,000 to $100,000 monthly | $15,000 to $120,000 monthly |
Environmental Controls | $50,000 to $200,000 (upfront); $2,000 to $10,000 monthly | $30,000 to $150,000 (upfront); $1,000 to $8,000 monthly |
Etching tends to be more cost-effective in terms of initial setup, especially for high-volume production. The chemical costs are significant, but the overall utility consumption is lower than
electroforming.Electroforming has higher initial costs due to the need for more complex machinery and higher electricity consumption. However, it produces parts with more consistent thickness and is better suited for applications where precision and surface finish are paramount.
If you have metal wet etching needs, please feel free to contact us.
FAQs
What metals can you use to customize my goods?
- Wet Etching Germanium
- Wet Etching Gallium Nitride (GaN)
- Wet Etching Indium
- Wet Etching Cobalt
- Wet Etching Tungsten
- Wet Etching Stainless Steel
- Wet Etching Aluminum
- Wet Etching Kovar
- Wet Etching Copper
- Wet Etching Steel
- Wet Etching Nickel
- Wet Etching Platinum
- Wet Etching Silver
- Wet Etching Rhodium
- Wet Etching Hafnium
- Wet Etching Vanadium
- Wet Etching Zirconium
- Wet Etching Titanium
- Wet Etching Niobium
- Wet Etching Tantalum
- Wet Etching Molybdenum
- Wet Etching Brass
- Wet Etching Rhenium
How quickly can I get your response?
Within 24 hours.
Will you do 100% inspection before shipping out the orders?
Yes we do.
Can I have prototypes or samples before placing the order?
Samples are always available.